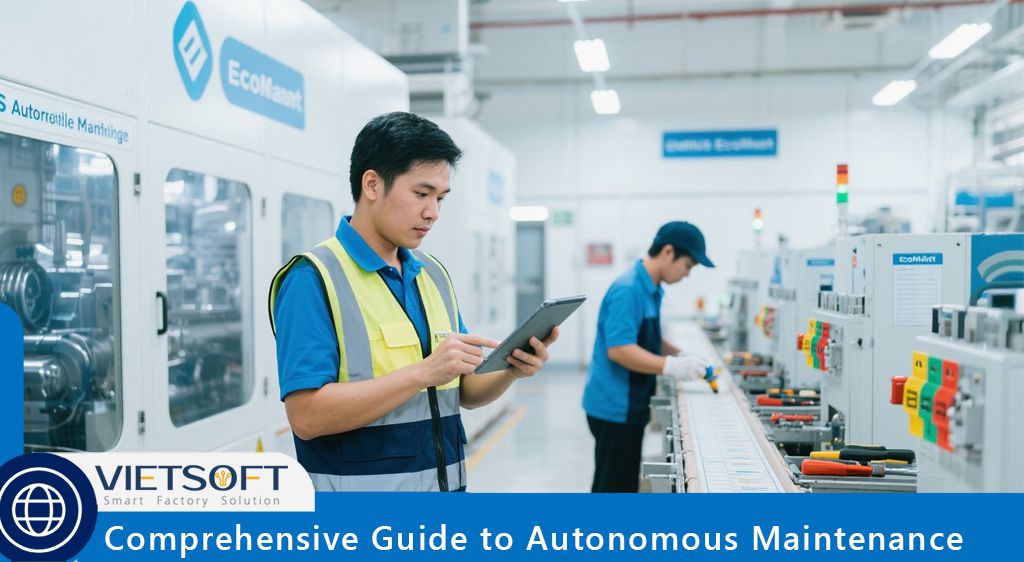
Autonomous Maintenance (AM) is a transformative strategy within Total Productive Maintenance (TPM) that empowers machine operators to take ownership of routine equipment upkeep. By fostering a culture of shared responsibility, AM enhances equipment reliability, reduces downtime, and drives operational excellence. This guide provides an in-depth exploration of Autonomous Maintenance, including its principles, implementation steps, best practices, and the role of modern tools like CMMS EcoMaint in sustaining success. Designed for maintenance professionals, operators, and plant managers, this article offers actionable insights to achieve long-term results.
I. What is Autonomous Maintenance?
Autonomous Maintenance, often referred to as Jishu Hozen in Japanese, is a core pillar of TPM that shifts basic maintenance tasks—such as cleaning, lubrication, and inspection—from specialized maintenance teams to equipment operators. Unlike traditional maintenance models where operators solely focus on production and maintenance teams handle repairs, AM promotes a collaborative approach. Operators become proactive stewards of their machines, ensuring they remain in optimal condition, while maintenance technicians focus on complex tasks.
II. Key Principles of Autonomous Maintenance
1. Proper Equipment Operation: Operators use machines correctly to minimize wear and prevent breakdowns.
2. Like-New Condition: Regular cleaning, lubrication, and inspections maintain equipment in pristine condition.
3. Operator Ownership: Operators take responsibility for routine tasks, fostering pride and accountability.
4. Standardized Procedures: Clear, consistent maintenance protocols ensure efficiency and quality.
5. Continuous Improvement: Operators and teams continuously refine processes to enhance reliability.
AM likens equipment to a “child,” with production staff as “parents” handling daily care and maintenance staff as “doctors” addressing specialized needs. This analogy, from the SMEDA guide, underscores the shared goal of keeping machines “happy and healthy.”
III. Why Autonomous Maintenance Matters
In industries like manufacturing, energy, and transportation, equipment reliability is critical to productivity and safety. Autonomous Maintenance addresses common challenges such as unexpected breakdowns, high maintenance costs, and production delays. Here’s why AM is essential:
- Reduces Downtime: Early detection of issues prevents costly stoppages.
- Lowers Maintenance Costs: Routine tasks handled by operators reduce the need for specialized interventions.
- Enhances Safety: Well-maintained equipment minimizes workplace hazards.
- Boosts Employee Engagement: Operators gain a sense of ownership, improving morale and teamwork.
- Extends Equipment Life: Proper care slows natural deterioration, maximizing asset value.
For example, in a food processing plant, operators trained in AM can clean and inspect packaging machines daily, preventing contamination and ensuring compliance with safety standards.
IV. Benefits of Autonomous Maintenance
Implementing Autonomous Maintenance yields measurable advantages across operational, financial, and cultural dimensions. Below are key benefits:
1. Increased Equipment Uptime: Regular inspections catch minor issues before they escalate, reducing unplanned downtime by up to 20–30%, according to industry studies.
2. Cost Savings: By shifting routine tasks to operators, maintenance labor costs can decrease significantly.
3. Improved Safety: Clean, well-maintained machines reduce risks of accidents caused by leaks, loose parts, or malfunctions.
4. Early Problem Detection: Operators’ proximity to equipment enables them to spot abnormalities like unusual vibrations or oil leaks early.
5. Enhanced Team Collaboration: AM fosters a unified approach between production and maintenance teams, eliminating silos.
6. Empowered Workforce: Operators gain new skills, boosting confidence and job satisfaction.
For instance, a manufacturing facility in Vietnam that adopted AM reported a 15% reduction in maintenance costs and a 25% increase in production efficiency within the first year.
V. Understanding Equipment Deterioration
The SMEDA guide identifies two types of equipment deterioration, both addressed by AM:
1. Natural Deterioration
This occurs due to normal wear from friction, stress, or usage over time, even with proper operation.
Countermeasures:
- Time-based maintenance (e.g., replacing bearings after 10,000 hours).
- Design improvements for longer component life.
2. Forced/Accelerated Deterioration
This results from improper operation, neglect, or harsh conditions, accelerating wear. Examples include:
- Loose nuts and bolts causing misalignments.
- Improper cleaning leading to dust buildup.
- Oil leaks or rusting due to poor maintenance.
Countermeasures: Implement AM to enforce proper operation, regular cleaning, and timely inspections.
By addressing both types, AM ensures equipment remains reliable and cost-effective throughout its lifecycle.
VI. The Seven Steps to Implement Autonomous Maintenance
Implementing Autonomous Maintenance requires a structured approach to ensure buy-in, training, and sustainability. Below are the seven steps, enriched with practical insights:
1. Step 1: Build Operator Knowledge and Skills
Operators need a deep understanding of their equipment to perform maintenance effectively. Training should cover:
- Machine components and their functions.
- Common signs of deterioration (e.g., loose bolts, leaks).
- Basic troubleshooting and maintenance techniques.
- Safety protocols for handling equipment.
Best Practice: Use a mix of hands-on workshops, digital training modules, and one-point lessons (OPLs). For example, a 5-minute OPL on “How to Lubricate a Conveyor Belt” can reinforce learning.
2. Step 2: Conduct Initial Cleaning and Inspection
The goal is to restore equipment to a “like-new” state. This step involves:
- Thorough cleaning to remove dust, dirt, and debris.
- Inspecting for signs of wear, such as cracks, rust, or misalignments.
- Tightening loose fasteners and replacing minor parts.
Example: In a textile factory, operators cleaned spinning machines and discovered clogged air filters, which were replaced to improve performance.
3. Step 3: Eliminate Contamination Sources
Prevent recontamination by addressing root causes. Actions include:
- Installing seals or covers to protect against dust or moisture.
- Improving workplace organization using 5S principles (Sort, Set in Order, Shine, Standardize, Sustain).
- Ensuring safe access to hard-to-reach areas for cleaning.
Tip: Use visual aids like color-coded tags to mark contamination-prone areas.
4. Step 4: Establish Cleaning, Lubrication, and Inspection Standards
Develop clear standards for routine tasks, specifying:
- What to clean, lubricate, or inspect.
- How to perform each task (e.g., type of lubricant, frequency).
- Who is responsible for each task.
Best Practice: Document standards in digital checklists accessible via a CMMS like EcoMaint, ensuring consistency across shifts.
5. Step 5: Perform Regular Inspections
Operators conduct daily or shift-based inspections to monitor equipment health. Key activities include:
- Checking for abnormalities using the five senses (sight, sound, touch, smell, hearing).
- Recording findings in a CMMS for trend analysis.
- Reporting issues to maintenance teams promptly.
Example: An operator in a paper mill detected a faint buzzing sound in a motor, logged it in the CMMS, and prevented a potential failure.
6. Step 6: Standardize Visual Maintenance
Simplify maintenance tasks with visual cues, such as:
- Labels indicating valve directions or lubricant types.
- Transparent covers to monitor fluid levels.
- Color-coded gauges showing safe operating ranges.
Tip: Use augmented reality (AR) tools to overlay digital instructions on equipment, enhancing operator efficiency.
7. Step 7: Drive Continuous Improvement
AM is an ongoing process requiring regular evaluation. Strategies include:
- Analyzing maintenance data to identify trends (e.g., frequent failures).
- Soliciting operator feedback to refine standards.
- Celebrating successes to maintain motivation.
Best Practice: Use the Plan-Do-Check-Act (PDCA) cycle to iteratively improve processes.
VII. Best Practices for Successful Autonomous Maintenance
To maximize the impact of AM, adopt these industry-proven best practices:
1. Engage Operators Early
Involve operators in planning and standard-setting to foster ownership. Their frontline insights can identify practical challenges and solutions.
2. Invest in Comprehensive Training
Provide role-specific training tailored to equipment types. For critical assets, pair operators with maintenance technicians for mentorship.
3. Leverage Technology
A CMMS like EcoMaint streamlines AM by:
- Scheduling tasks and sending reminders.
- Tracking work orders and inspection results.
- Analyzing data to predict failures.
4. Align with TPM and Lean Principles
Integrate AM with other TPM pillars (e.g., planned maintenance) and lean practices like 5S to create a cohesive strategy.
5. Monitor Key Metrics
Track metrics like:
- Mean Time Between Failures (MTBF): Measures equipment reliability.
- Mean Time to Repair (MTTR): Gauges maintenance efficiency.
- Overall Equipment Effectiveness (OEE): Combines availability, performance, and quality.
Formula: OEE = Availability × Performance × Quality
Example: If a machine is available 90% of the time, operates at 85% of its maximum speed, and produces 95% defect-free output, OEE = 0.90 × 0.85 × 0.95 = 72.7%.
6. Recognize and Reward
Celebrate operator contributions, such as identifying a critical issue, to boost morale. Simple gestures like public recognition or small incentives can go a long way.
VIII. Tips for Sustaining Autonomous Maintenance
Sustaining AM as your organization scales requires ongoing commitment. Here are actionable tips:
1. Clarify Roles: Define responsibilities for operators, technicians, and supervisors to avoid confusion.
2. Continuous Training: Offer refresher courses and cross-training to accommodate new equipment or staff.
3. Robust Reporting System: Use a CMMS to log abnormalities and track resolutions, ensuring no issues are overlooked.
4. Foster a Culture of Improvement: Encourage operators to suggest process enhancements and reward innovative ideas.
5. Leverage Predictive Tools: Integrate sensors and IoT devices to monitor equipment health in real-time, complementing operator inspections.
IX. The Role of CMMS EcoMaint in Autonomous Maintenance
A Computerized Maintenance Management System (CMMS) is a game-changer for Autonomous Maintenance. Vietsoft’s CMMS EcoMaint, designed for the Vietnamese market, empowers organizations to streamline AM processes with features like:
- Work Order Management: Operators can create and track work orders for routine tasks, ensuring accountability.
- Asset Tracking: Maintains a digital history of equipment maintenance, aiding in root cause analysis.
- Preventive Maintenance Scheduling: Automates task reminders, ensuring timely inspections and lubrication.
- Inventory Control: Tracks spare parts, preventing delays due to unavailable components.
- Data Analytics: Provides insights into equipment performance, helping optimize maintenance strategies.
To explore how CMMS EcoMaint can transform your maintenance operations, Learn more about CMMS EcoMaint here.
Contact us via hotline: 0986778578 or email: sales@vietsoft.com.vn.
X. Common Challenges and Solutions
Implementing Autonomous Maintenance isn’t without hurdles. Here are common challenges and how to address them:
1. Resistance to Change:
o Solution: Communicate the benefits of AM clearly and involve operators in decision-making to build buy-in.
2. Lack of Training:
o Solution: Develop a structured training program with regular refreshers and hands-on practice.
3. Overwhelming Workload:
o Solution: Start with pilot projects on select equipment to gradually scale AM without overloading staff.
4. Data Overload:
o Solution: Use a CMMS to filter and prioritize data, focusing on actionable insights.
XI. Conclusion: Building a Sustainable Autonomous Maintenance Program
Autonomous Maintenance is a powerful strategy for enhancing equipment reliability, reducing costs, and fostering a culture of ownership. By following the seven steps, adopting best practices, and leveraging tools like CMMS EcoMaint, organizations can achieve lasting success. The key lies in empowering operators, aligning with broader operational goals, and committing to continuous improvement.
Ready to elevate your maintenance program? Discover how Vietsoft’s CMMS EcoMaint can support your Autonomous Maintenance journey, delivering real-time insights and streamlined workflows for your team.