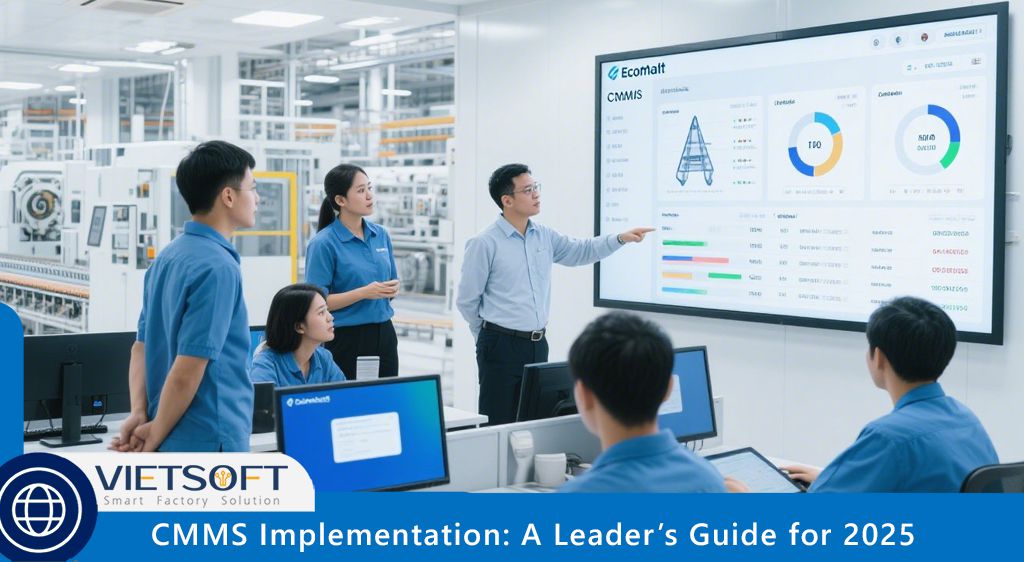
In today’s fast-paced industrial landscape, effective maintenance management is the backbone of operational success. A Computerized Maintenance Management System (CMMS) is no longer a luxury but a necessity for organizations striving to optimize asset performance, reduce downtime, and enhance productivity. For leaders in manufacturing, facilities management, or any asset-intensive industry, implementing a CMMS is a transformative step toward operational excellence. This comprehensive guide explores the CMMS implementation process, its critical role, key steps, challenges, and best practices, tailored for 2025’s evolving technological and industrial demands.
I. What Is a CMMS and Why Does It Matter?
A Computerized Maintenance Management System (CMMS) is a software solution designed to streamline maintenance operations by centralizing asset data, automating work order processes, and enabling proactive maintenance strategies. Unlike traditional methods relying on spreadsheets or paper-based systems, a CMMS provides real-time insights into equipment health, maintenance schedules, and resource allocation, empowering organizations to make data-driven decisions.
II. The Role of CMMS in Modern Maintenance
In 2025, industries face mounting pressure to minimize downtime, comply with stringent regulations, and optimize costs. A CMMS addresses these challenges by:
- Centralizing Data: Consolidates asset information, maintenance histories, and work orders into a single platform, eliminating scattered records.
- Automating Workflows: Streamlines task assignments, scheduling, and tracking, reducing manual errors and inefficiencies.
- Enabling Preventive Maintenance: Shifts teams from reactive to proactive maintenance, preventing costly breakdowns.
- Enhancing Compliance: Provides auditable records for regulatory requirements, such as OSHA, FDA, or ISO standards.
- Driving Cost Savings: Optimizes spare parts inventory, reduces overtime, and extends asset lifespans.
For example, a manufacturing plant using a CMMS can reduce unplanned downtime by scheduling preventive maintenance based on real-time equipment data, saving thousands of dollars annually.
III. Why CMMS Implementation Is Critical
A CMMS is only as effective as its implementation. A poorly executed rollout can lead to user resistance, data inaccuracies, or misaligned workflows, resulting in wasted resources and missed opportunities. A structured CMMS implementation ensures the system aligns with organizational goals, integrates seamlessly with existing processes, and delivers long-term value.
IV. Key Phases of CMMS Implementation
A successful CMMS implementation follows a phased approach, balancing planning, execution, and continuous improvement. Below is a detailed timeline and key phases to guide your journey in 2025.
1. Phase 1: Planning and Needs Assessment (1-2 Months)
The foundation of a successful CMMS implementation lies in thorough planning. This phase involves:
- Defining Objectives: Identify specific goals, such as reducing downtime by 15%, improving work order completion rates, or achieving compliance with industry standards.
- Assessing Current Processes: Conduct an audit of existing maintenance workflows, asset inventories, and data sources. Identify pain points, such as delayed repairs or incomplete records.
- Forming a Project Team: Assemble a cross-functional team, including maintenance technicians, IT specialists, operations managers, and executive sponsors. Designate a project manager to oversee the process.
- Budgeting and Resource Allocation: Estimate costs for software, training, and data migration. Secure executive buy-in to ensure funding and support.
2. Phase 2: System Selection and Configuration (1-3 Months)
Choosing the right CMMS and configuring it to fit your needs is pivotal. This phase includes:
- Selecting a CMMS Vendor: Evaluate platforms based on scalability, user-friendliness, mobile access, and integration capabilities with ERP, IoT, or SCADA systems. Request demos and trials to assess functionality.
- Data Preparation: Clean and standardize asset data, including equipment lists, maintenance histories, and spare parts inventories. Remove duplicates and outdated records to ensure accuracy.
- System Customization: Configure workflows, user roles, and preventive maintenance schedules to reflect your operational reality. For instance, set up condition-based triggers for assets requiring frequent inspections.
Integration Tip: Ensure the CMMS integrates with existing systems, such as SAP for inventory management or IoT sensors for real-time condition monitoring, to maximize data flow and usability.
3. Phase 3: Training and Pilot Testing (1 Month)
Training and testing are critical to user adoption and system reliability.
- Role-Based Training: Provide hands-on training tailored to each user group—technicians for work order management, supervisors for scheduling, and managers for reporting. Use real-world scenarios to make training relevant.
- Pilot Testing: Launch the CMMS in a single department or facility to identify issues. For example, test the system on a production line to ensure work orders are assigned and closed correctly.
- Feedback Collection: Gather user feedback to refine configurations, address usability concerns, and optimize workflows.
Example: A pilot test in a manufacturing facility might reveal that technicians need a simplified mobile interface to log work orders, prompting adjustments before full rollout.
4. Phase 4: Full Rollout and Support (1-2 Months)
The go-live phase transitions the organization to full CMMS usage.
- Soft Launch: Start with limited functionality, such as work order management, before scaling to preventive maintenance or inventory tracking.
- Ongoing Support: Establish a helpdesk or support team to address user issues. Provide quick-reference guides and SOPs for common tasks.
- Monitoring: Track key metrics, such as work order completion rates and user logins, to ensure adoption and system performance.
5. Phase 5: Continuous Optimization (Ongoing)
A CMMS is a living system that evolves with your organization.
- Performance Evaluation: Regularly assess KPIs, such as Mean Time to Repair (MTTR) or preventive maintenance compliance, to measure impact.
- User Feedback: Conduct quarterly surveys to identify pain points and opportunities for improvement.
- System Updates: Stay updated with vendor releases to leverage new features, such as AI-driven analytics or enhanced mobile capabilities.
V. Essential Steps for a Successful CMMS Implementation
To ensure a smooth CMMS implementation, follow these actionable steps:
1. Step 1: Set Clear Goals and KPIs
Define measurable objectives, such as reducing downtime by 20% or increasing preventive maintenance compliance to 95%. Use KPIs like MTTR, Mean Time Between Failures (MTBF), and Overall Equipment Effectiveness (OEE) to track progress. For example, OEE can be calculated as:
OEE = Availability × Performance × Quality
Where:
- Availability = (Operating Time / Planned Production Time) × 100
- Performance = (Actual Output / Standard Output) × 100
- Quality = (Good Units / Total Units Produced) × 100
A manufacturing plant might aim for an OEE of 85%, a benchmark for world-class operations.
2. Step 2: Build a Dedicated Implementation Team
Form a team with representatives from maintenance, IT, operations, and finance. Appoint a project manager to coordinate tasks and an “implementation champion” to drive user adoption. For example, a maintenance supervisor could serve as the champion, ensuring technicians embrace the system.
3. Step 3: Choose the Right CMMS Solution
Select a CMMS that aligns with your needs. Key criteria include:
- Scalability: Supports multi-site operations and growing asset fleets.
- Mobile Access: Allows technicians to update tasks in real-time from the field.
- Integration: Connects with ERP, IoT, or SCADA systems for seamless data flow.
- User-Friendliness: Features an intuitive interface to minimize training time.
EcoMaint by Vietsoft, for instance, offers a scalable, mobile-friendly solution tailored for Vietnamese industries, with robust integration capabilities and user-friendly workflows.
4. Step 4: Ensure Data Quality and Migration
Accurate data is the backbone of a CMMS. Steps include:
- Asset Inventory: Create a detailed register of assets, including IDs, locations, and maintenance histories.
- Data Cleansing: Remove duplicates, standardize naming conventions, and validate data integrity.
- Migration Strategy: Use automated tools to import data from spreadsheets or legacy systems, ensuring compatibility with the CMMS.
5. Step 5: Customize for Operational Fit
Tailor the CMMS to match your workflows. For example, configure preventive maintenance schedules based on equipment usage (e.g., every 500 hours) or condition (e.g., vibration thresholds). Set up role-specific dashboards for technicians, supervisors, and managers.
6. Step 6: Train and Empower Users
Offer role-specific training sessions, supplemented by cheat sheets and video tutorials. Pair early adopters with hesitant users to foster peer support. For instance, a technician struggling with mobile work order updates could shadow a trained colleague.
7. Step 7: Conduct Rigorous Testing
Run a pilot program to test workflows, notifications, and reporting. Address issues like incorrect asset hierarchies or delayed notifications before scaling up. A successful pilot ensures the system is ready for organization-wide use.
8. Step 8: Launch and Monitor
Execute a phased rollout, starting with core functions like work order management. Monitor adoption metrics, such as daily logins or task completion rates, and provide ongoing support to address challenges.
VI. Common Challenges in CMMS Implementation
Despite careful planning, CMMS implementation can face hurdles. Here are the most common challenges and how to overcome them:
1. Challenge 1: Poor Data Quality
Inconsistent or incomplete data undermines system reliability. For example, missing maintenance histories can lead to inaccurate preventive schedules.
Solution: Invest time in data cleansing before migration. Use mobile apps to capture real-time data from the field, ensuring accuracy.
2. Challenge 2: User Resistance
Employees may resist adopting a new system due to unfamiliarity or fear of change.
Solution: Communicate the benefits clearly—e.g., reduced overtime or faster task completion. Involve users in the configuration process to build ownership.
3. Challenge 3: Lack of Executive Support
Without leadership backing, projects can stall due to budget constraints or competing priorities.
Solution: Present a business case highlighting ROI, such as a 15% reduction in maintenance costs or 10% uptime improvement, to secure buy-in.
4. Challenge 4: Integration Issues
A CMMS that doesn’t integrate with existing systems can create data silos.
Solution: Choose a CMMS with robust API support, like EcoMaint, which integrates seamlessly with ERP and IoT platforms. Test integrations during the pilot phase to ensure compatibility.
VII. Best Practices for CMMS Implementation Success
To maximize the impact of your CMMS implementation, adopt these best practices:
· Engage Stakeholders Early: Involve technicians, supervisors, and executives in planning to ensure the system meets diverse needs.
· Prioritize Data Integrity: Clean and standardize data before migration to ensure reliable reporting and analytics.
· Invest in Training: Provide ongoing, role-specific training to boost confidence and adoption.
· Monitor and Optimize: Use KPIs to track performance and gather user feedback to refine the system.
· Leverage Vendor Support: Partner with a vendor offering hands-on onboarding and 24/7 support, such as Vietsoft’s EcoMaint team.
VIII. Benefits of a Well-Executed CMMS Implementation
A successful CMMS implementation delivers transformative benefits:
- Reduced Downtime: Proactive maintenance prevents unexpected failures, improving uptime by up to 30%.
- Cost Savings: Optimized spare parts inventory and reduced overtime can lower maintenance costs by 15-20%.
- Improved Compliance: Digital records simplify audits, ensuring adherence to regulations like ISO 9001 or FDA standards.
- Enhanced Productivity: Automated workflows free up technicians to focus on high-value tasks, boosting efficiency.
- Data-Driven Decisions: Real-time analytics enable leaders to predict failures and optimize resource allocation.
IX. Introducing EcoMaint by Vietsoft: Your Partner in CMMS Success
For organizations in Vietnam seeking a reliable, scalable, and user-friendly CMMS, EcoMaint by Vietsoft stands out as a premier solution. Designed with the unique needs of Vietnamese industries in mind, EcoMaint offers:
- Mobile Accessibility: Technicians can manage work orders and update tasks from anywhere, even offline.
- Seamless Integration: Connects with ERP, IoT, and SCADA systems for real-time data flow.
- Intuitive Interface: Simplifies adoption with minimal training, ideal for diverse teams.
- Local Support: Vietsoft’s dedicated team provides hands-on onboarding and 24/7 support in Vietnamese.
Ready to transform your maintenance operations? Discover how EcoMaint can streamline your workflows and drive results. Learn more about CMMS EcoMaint here. Contact us for consultation via hotline: 0986778578 or email: sales@vietsoft.com.vn.
X. Conclusion
Implementing a CMMS in 2025 is a strategic investment in operational efficiency, cost savings, and regulatory compliance. By following a structured CMMS implementation process—encompassing planning, system selection, training, and continuous optimization—organizations can unlock the full potential of their maintenance operations. Despite challenges like data quality or user resistance, adopting best practices and partnering with a reliable vendor like Vietsoft ensures success. With EcoMaint, Vietnamese businesses can achieve seamless CMMS implementation, driving productivity and resilience in an increasingly competitive landscape. Start your journey today and transform maintenance from a cost center to a strategic asset.