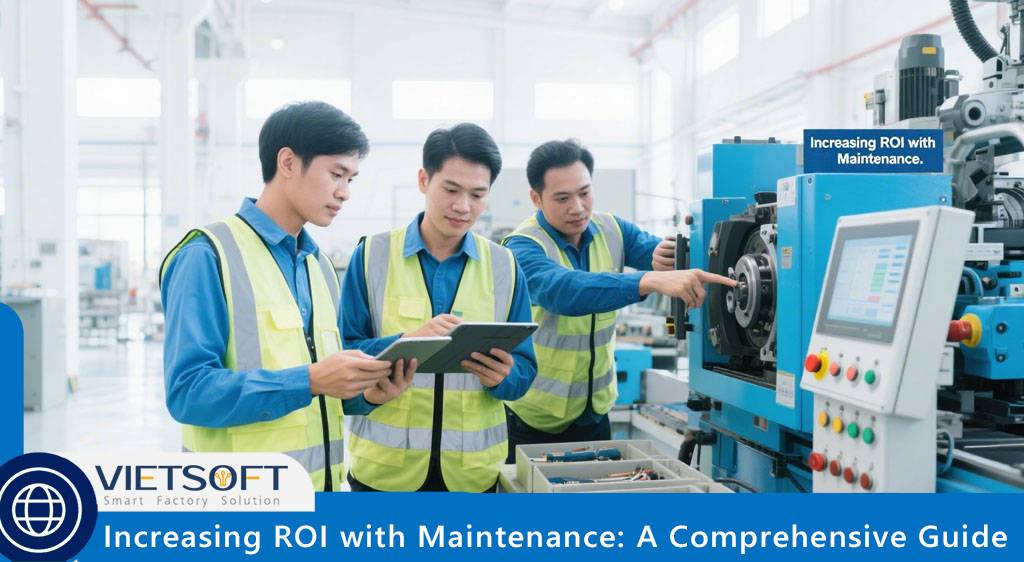
In the competitive world of manufacturing, optimizing operations to maximize profitability is a constant pursuit. One powerful strategy to achieve this is through effective maintenance management, which directly contributes to Increasing ROI with Maintenance. Return on Investment (ROI) is a critical metric that measures the efficiency and profitability of investments, and in manufacturing, maintenance plays a pivotal role in enhancing this metric. By implementing strategic maintenance practices, businesses can reduce costs, improve equipment reliability, and boost overall productivity. This article explores the concept of ROI, how maintenance impacts it, and actionable strategies to increase ROI through maintenance.
I. Understanding ROI in Manufacturing
What is ROI?
Return on Investment (ROI) is a performance measure used to evaluate the efficiency or profitability of an investment or to compare the efficiency of different investments. In manufacturing, ROI is calculated to assess the financial returns generated from assets, equipment, or operational strategies. The formula for ROI is straightforward:
ROI = (Net Profit / Investment Cost) x 100
For example, if a company invests $100,000 in new machinery and generates $120,000 in profit, the ROI would be:
ROI = (120,000 – 100,000) / 100,000 x 100 = 20%
In the context of maintenance, ROI is often measured as Return on Assets (ROA), which evaluates how effectively a company uses its assets to generate profit. The formulas for ROA are:
- ROA = (Net Income / Replacement Asset Value) x 100
- ROA = (Operating Profit (EBIT) / Total Assets) x 100
By focusing on Increasing ROI with Maintenance, manufacturers can optimize their asset utilization, reduce operational costs, and enhance profitability.
II. Why Maintenance Matters for ROI
Maintenance directly influences ROI by minimizing downtime, extending equipment lifespan, and improving operational efficiency. Unplanned equipment failures can lead to costly production halts, increased repair expenses, and missed delivery deadlines, all of which erode profitability. A well-executed maintenance strategy, particularly preventive and predictive approaches, mitigates these risks and ensures assets perform at their peak, thereby Increasing ROI with Maintenance.
III. Key Strategies for Increasing ROI with Maintenance
1. Implementing Preventive Maintenance Programs
Preventive maintenance (PM) involves scheduling regular maintenance tasks to prevent equipment failures before they occur. This proactive approach reduces the likelihood of unplanned downtime, which can cost manufacturers thousands of dollars per hour. Key benefits of PM include:
- Reduced Downtime: Regular inspections and maintenance keep equipment running smoothly, minimizing unexpected breakdowns.
- Extended Equipment Lifespan: Routine care prevents excessive wear and tear, delaying the need for costly replacements.
- Cost Savings: PM reduces emergency repair costs, which are often significantly higher than planned maintenance expenses.
- Improved Safety: Well-maintained equipment reduces workplace hazards, enhancing employee safety and reducing liability costs.
To implement an effective PM program, follow these steps:
1. Catalog Critical Assets: Identify and prioritize equipment essential to production. Use a CMMS like EcoMaint to maintain detailed asset records.
2. Set Maintenance Intervals: Determine optimal maintenance frequencies based on manufacturer recommendations, usage patterns, and historical data.
3. Automate Work Orders: Use a CMMS to schedule recurring maintenance tasks, ensuring timely execution.
4. Monitor and Adjust: Regularly review maintenance outcomes to refine schedules and improve efficiency.
By adopting a preventive maintenance strategy, manufacturers can significantly reduce operational disruptions, directly contributing to Increasing ROI with Maintenance.
2. Leveraging Key Performance Indicators (KPIs)
KPIs are quantifiable metrics that help manufacturers track and optimize performance. By measuring maintenance-related KPIs, businesses can identify inefficiencies, allocate resources effectively, and make data-driven decisions to increase ROI. Key maintenance KPIs include:
- Mean Time Between Failures (MTBF): Measures the average time between equipment breakdowns. A higher MTBF indicates better reliability.
- Planned Maintenance Percentage (PMP): Tracks the proportion of completed scheduled maintenance tasks versus total tasks.
- Overall Equipment Effectiveness (OEE): Combines availability, performance, and quality to assess equipment productivity.
- Mean Time to Repair (MTTR): Measures the average time required to repair equipment, indicating maintenance efficiency.
- Unscheduled Downtime: Tracks the time assets are unavailable due to unplanned repairs, highlighting areas for improvement.
3. Minimizing Equipment Downtime
Downtime is one of the biggest threats to profitability in manufacturing. According to industry studies, unplanned downtime can cost manufacturers up to $50,000 per hour. By minimizing downtime, businesses can maintain production schedules, meet customer demands, and improve ROI. Strategies to reduce downtime include:
- Proactive Maintenance: Regular PM tasks address minor issues before they escalate into major failures.
- Real-Time Monitoring: Use IoT sensors to monitor equipment health and detect potential issues early.
- Spare Parts Management: Maintain an inventory of frequently replaced parts to reduce repair times.
- Data-Driven Decisions: Analyze historical downtime data to identify recurring issues and implement corrective actions.
For instance, a factory experiencing frequent motor failures can use a CMMS to track downtime events, identify root causes, and schedule targeted maintenance, thereby Increasing ROI with Maintenance through reduced disruptions.
4. Adopting Predictive and Prescriptive Maintenance
While preventive maintenance is effective, predictive and prescriptive maintenance take ROI optimization to the next level. Predictive maintenance uses data analytics and IoT sensors to predict when equipment is likely to fail, allowing for timely interventions. Prescriptive maintenance goes further by providing specific recommendations for maintenance actions based on real-time data and machine learning algorithms.
Key components of predictive and prescriptive maintenance include:
- IoT Sensors: Monitor equipment parameters like temperature, vibration, and pressure to detect anomalies.
- AI and Machine Learning: Analyze historical and real-time data to predict failures and suggest optimal maintenance actions.
- Integration with CMMS: Tools like EcoMaint integrate IoT data with maintenance workflows, enabling seamless execution of predictive and prescriptive strategies.
For example, a predictive maintenance system might detect unusual vibrations in a conveyor belt motor, prompting a maintenance team to replace a worn bearing before it causes a breakdown. This proactive approach minimizes downtime and repair costs, significantly Increasing ROI with Maintenance.
5. Building a Data-Driven Maintenance Culture
A data-driven maintenance culture empowers teams to make informed decisions, optimize processes, and maximize ROI. Key elements of this culture include:
- Training and Education: Equip maintenance teams with skills to interpret data and use CMMS tools effectively.
- Collaboration: Foster communication between maintenance, operations, and management teams to align goals.
- Continuous Improvement: Regularly review KPI data to identify trends, refine strategies, and address inefficiencies.
- Accountability: Set clear performance goals and use CMMS dashboards to track progress.
By cultivating a data-driven approach, manufacturers can ensure maintenance efforts are aligned with business objectives, leading to sustained ROI improvements.
IV. How CMMS EcoMaint Drives ROI
To achieve the full potential of Increasing ROI with Maintenance, manufacturers need robust tools to streamline processes and provide actionable insights. CMMS EcoMaint, developed by Vietsoft, is a cloud-based solution designed to optimize maintenance management and boost profitability. Key features of EcoMaint include:
- Asset Management: Maintain detailed records of equipment, including maintenance history and performance data.
- Work Order Automation: Schedule and track maintenance tasks with ease, reducing administrative overhead.
- Real-Time Reporting: Access dashboards to monitor KPIs like OEE, MTBF, and downtime in real time.
- IoT Integration: Connect with IoT sensors to enable predictive and prescriptive maintenance.
- Mobile Accessibility: Allow technicians to access work orders, report issues, and communicate on the go.
By implementing EcoMaint, manufacturers can reduce downtime by up to 30%, extend equipment lifespan by 20%, and achieve significant cost savings. Curious about how EcoMaint can transform your maintenance strategy? Explore EcoMaint’s features and see how it can drive Increasing ROI with Maintenance for your organization.
V/ Calculating ROI with Maintenance Strategies
To quantify the impact of maintenance on ROI, manufacturers can use the following approach:
· Identify Costs: Calculate the total investment in maintenance, including labor, parts, and software costs.
· Measure Benefits: Quantify savings from reduced downtime, lower repair costs, and extended equipment life.
· Apply ROI Formula: Use the ROI formula to determine the return on maintenance investments.
For example, suppose a manufacturer invests $50,000 in EcoMaint and preventive maintenance programs. Over a year, the company reduces downtime costs by $80,000 and repair expenses by $20,000. The ROI would be:
ROI = (80,000 + 20,000 – 50,000) / 50,000 x 100 = 100%
This calculation demonstrates the substantial financial benefits of strategic maintenance, reinforcing the importance of Increasing ROI with Maintenance.
VI. Overcoming Common Maintenance Challenges
Despite the benefits, manufacturers may face challenges in implementing effective maintenance strategies. Common issues include:
- Resistance to Change: Employees may resist adopting new technologies or processes. Address this through training and clear communication of benefits.
- Data Overload: Collecting too much data without proper analysis can overwhelm teams. Use a CMMS to filter and prioritize actionable insights.
- Resource Constraints: Limited budgets or staffing can hinder maintenance efforts. Prioritize high-impact assets and leverage automation to maximize efficiency.
By addressing these challenges proactively, manufacturers can ensure their maintenance strategies deliver maximum ROI.
VII. Conclusion: Unlock the Power of Maintenance for ROI
Increasing ROI with Maintenance is not just a goal but an achievable reality for manufacturers who adopt proactive, data-driven maintenance strategies. By implementing preventive and predictive maintenance, leveraging KPIs, and using advanced tools like CMMS EcoMaint, businesses can reduce costs, enhance equipment reliability, and boost productivity. These efforts translate into substantial financial returns, making maintenance a cornerstone of manufacturing success.
Ready to take your maintenance strategy to the next level? Discover the CMMS EcoMaint solution here.
Contact us for consultation via hotline: 0986778578 or email: sales@vietsoft.com.vn