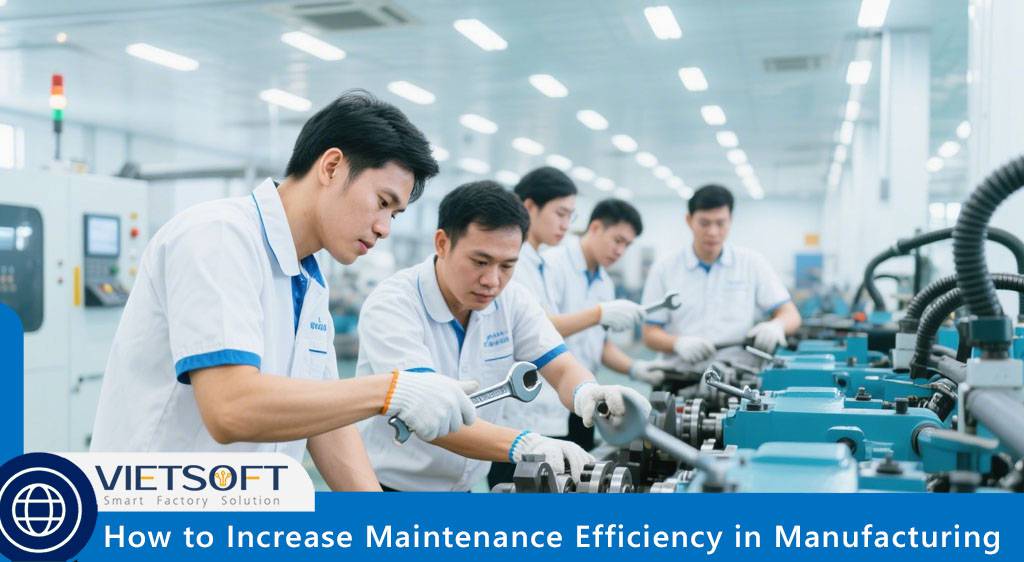
In today’s fast-paced manufacturing landscape, increasing maintenance efficiency is a critical goal for organizations aiming to optimize operations, reduce costs, and ensure long-term sustainability. By adopting strategic approaches, leveraging modern technologies, and implementing data-driven practices, companies can transform their maintenance processes into a competitive advantage.
This guide explores the concept of maintenance efficiency, key metrics for measurement, critical factors affecting performance, and actionable strategies to enhance efficiency, with a focus on practical insights for maintenance professionals in Vietnam’s industrial sector.
I. What Is Maintenance Efficiency?
Maintenance efficiency refers to the ability to manage and maintain physical assets—such as machinery, equipment, and facilities—in optimal condition while minimizing waste of time, labor, and resources. It’s about achieving maximum equipment uptime, extending asset lifespan, and reducing operational costs through streamlined processes.
In manufacturing, maintenance efficiency is pivotal because it directly impacts production output, safety, and profitability. For example, inefficient maintenance practices can lead to unplanned downtime, costing companies thousands of dollars per hour. By contrast, efficient maintenance ensures smooth operations, fewer breakdowns, and a safer workplace.
To increase maintenance efficiency, organizations must balance proactive strategies (like preventive and predictive maintenance) with reactive approaches, while leveraging technology to automate and optimize workflows. The ultimate goal is to keep assets performing at their best with minimal disruption to production.
II. Why Maintenance Efficiency Matters
Efficient maintenance is more than just fixing machines—it’s about creating a sustainable, high-performing operation. Here are three key reasons why increasing maintenance efficiency should be a priority:
1. Reduced Downtime
Unplanned downtime is a major challenge in manufacturing, halting production and incurring significant costs. According to industry studies, 69% of facilities experience unexpected downtime at least once a month, with costs averaging $124,669 per hour. By improving maintenance efficiency, organizations can prevent small issues from escalating into major failures, ensuring continuous production and minimizing financial losses.
2. Prolonged Asset Lifespan
Regular, well-planned maintenance reduces wear and tear, extending the operational life of equipment. Research indicates that consistent maintenance can increase asset lifespan by 20–40%. This not only improves return on investment (ROI) but also delays the need for costly replacements, freeing up capital for other priorities.
3. Enhanced Workplace Safety
Inefficient maintenance increases the risk of equipment failures, which can lead to accidents. Data from the European Agency for Safety and Health at Work shows that 14–20% of workplace accidents occur during maintenance activities. By prioritizing efficiency, companies can reduce emergency repairs, ensure compliance with safety standards, and create a safer environment for technicians and operators.
III. Key Metrics to Measure Maintenance Efficiency
To increase maintenance efficiency, you need to measure it. Tracking key performance indicators (KPIs) provides insights into current performance and highlights areas for improvement. Below are five essential metrics to monitor:
1. Mean Time to Repair (MTTR)
MTTR measures the average time required to repair equipment after a failure. A lower MTTR indicates a well-organized team that responds quickly, reflecting high maintenance efficiency. For example, reducing MTTR from 30 minutes to 15 minutes for a conveyor belt repair could save $125,000 per hour in production losses.
2. Mean Time Between Failures (MTBF)
MTBF calculates the average time an asset operates before failing. A higher MTBF signifies greater reliability and effective maintenance practices. Tracking MTBF helps identify underperforming assets that may require more frequent inspections or upgrades.
3. Planned Maintenance Percentage (PMP)
PMP measures the proportion of maintenance activities that are planned versus reactive. A high PMP (e.g., 80%) indicates a proactive approach, reducing downtime and costs. Aim for a PMP of 70–90% to optimize efficiency.
4. Preventive Maintenance Compliance (PMC)
PMC tracks the percentage of scheduled maintenance tasks completed on time. High compliance ensures that preventive tasks are executed as planned, preventing unexpected failures. For instance, completing 95% of scheduled inspections reflects strong maintenance discipline.
5. Overall Equipment Effectiveness (OEE)
OEE is a comprehensive metric that combines availability, performance, and quality to measure equipment productivity. Calculated as OEE = Availability × Performance × Quality, a higher OEE (e.g., 85%) indicates efficient maintenance and production processes.
By monitoring these metrics through a CMMS like EcoMaint, maintenance teams can gain real-time insights, identify bottlenecks, and make data-driven decisions to increase maintenance efficiency.
IV. Critical Factors Influencing Maintenance Efficiency
Several factors can impact maintenance efficiency, ranging from planning to technology adoption. Understanding these challenges is essential for developing effective strategies. Below are the key factors to consider:
1. Poor Planning and Scheduling
Inadequate planning leads to delays, resource shortages, and unplanned downtime. For example, scheduling maintenance during peak production hours can disrupt operations. Effective planning involves prioritizing tasks based on asset criticality and aligning schedules with production needs.
2. Over-Reliance on Reactive Maintenance
Excessive corrective maintenance—fixing equipment only after it fails—increases costs and downtime. Shifting to preventive or predictive maintenance reduces the need for emergency repairs, improving efficiency. Studies show that proactive maintenance can save 12–18% in costs compared to reactive approaches.
3. Insufficient Staff Training
Untrained technicians may perform tasks inefficiently or incorrectly, compromising safety and quality. Continuous training on modern equipment, safety protocols, and CMMS usage is vital to enhance skills and confidence.
4. Ineffective Inventory Management
Running out of spare parts or overstocking materials can disrupt maintenance workflows. Poor inventory management delays repairs, increasing downtime. A CMMS can automate inventory tracking, ensuring parts are available when needed without excess costs.
5. Outdated Technology
Manual processes or obsolete systems limit efficiency and accuracy. Adopting technologies like IoT sensors, predictive analytics, and cloud-based CMMS enables real-time monitoring and data-driven maintenance, significantly boosting performance.
6. Lack of Collaboration
Poor communication between maintenance, production, and procurement teams can lead to misaligned priorities and delays. Collaborative strategies, supported by digital tools, ensure seamless coordination and faster issue resolution.
Addressing these factors is the foundation for increasing maintenance efficiency and achieving operational excellence.
V. Strategies to Increase Maintenance Efficiency
To transform maintenance operations, organizations must adopt proven strategies that optimize processes, leverage technology, and empower teams. Below are seven practical approaches to increase maintenance efficiency, tailored for Vietnam’s manufacturing sector.
1. Implement a Preventive Maintenance Program
Preventive maintenance (PM) involves regular inspections, cleaning, lubrication, and adjustments to prevent failures. By scheduling tasks based on manufacturer recommendations or usage patterns, PM reduces downtime and extends asset life. For example, changing engine oil every 3,000 miles or inspecting a CNC machine monthly ensures reliability.
Key Actions:
- Create a PM schedule using a CMMS to automate task assignments.
- Prioritize critical assets that impact production or safety.
- Track PM compliance to ensure tasks are completed on time.
Studies show that PM can save 12–18% in maintenance costs, making it a cornerstone of efficient operations.
2. Adopt Predictive Maintenance (PdM)
Predictive maintenance uses sensors, IoT devices, and data analytics to monitor equipment conditions in real time and predict failures before they occur. For instance, vibration sensors on a pump can detect misalignment, triggering maintenance at the optimal time. PdM minimizes over-maintenance and reduces downtime by 10–20%, according to Deloitte.
Key Actions:
- Install IoT sensors on high-value assets to monitor parameters like temperature, vibration, or pressure.
- Integrate sensor data with a CMMS for automated alerts and work order creation.
- Train technicians to interpret predictive data and act on insights.
In Vietnam’s manufacturing hubs, PdM is gaining traction as companies invest in Industry 4.0 technologies to stay competitive.
3. Optimize Spare Parts Inventory
Effective inventory management ensures that spare parts are available without tying up capital in excess stock. Delays in accessing parts can extend downtime by 30%, impacting efficiency. A CMMS like EcoMaint streamlines inventory by tracking stock levels, usage, and reorder points in real time.
Key Actions:
- Conduct an inventory audit to identify critical parts for key assets.
- Set minimum and maximum stock levels to prevent shortages or overstocking.
- Use barcode scanning or RFID tags for accurate inventory updates.
4. Standardize Workflows with SOPs
Standard Operating Procedures (SOPs) ensure consistency and repeatability in maintenance tasks. Digital SOPs, stored in a CMMS, provide technicians with step-by-step instructions, checklists, and safety protocols, reducing errors and improving efficiency.
Key Actions:
- Involve technicians in drafting SOPs to capture practical insights.
- Use simple, actionable language and include visuals like diagrams or videos.
- Automate SOP delivery through a CMMS for real-time access.
For instance, an SOP for inspecting a hydraulic press might include steps for checking fluid levels, pressure settings, and safety guards, ensuring thorough and consistent execution.
5. Leverage Data for Decision-Making
Data from CMMS, IoT sensors, and work orders provides valuable insights for optimizing maintenance. By analyzing trends, managers can identify underperforming assets, adjust schedules, and allocate resources effectively. For example, frequent breakdowns of a specific machine may indicate the need for replacement or enhanced PM.
Key Actions:
- Use CMMS dashboards to monitor KPIs like MTTR, PMP, and OEE.
- Generate automated reports to track performance over time.
- Conduct root cause analysis (RCA) for recurring issues using tools like the 5 Whys or Fishbone Diagrams.
Data-driven decisions empower teams to increase maintenance efficiency by focusing efforts where they matter most.
6. Enhance Team Skills Through Training
A skilled workforce is essential for efficient maintenance. In Vietnam, where manufacturing is rapidly adopting automation, technicians need training on modern equipment, IoT systems, and CMMS platforms like EcoMaint. Well-trained teams work faster, make fewer errors, and contribute to safety.
Key Actions:
- Identify skill gaps through performance reviews or feedback.
- Offer regular training on technical skills, safety, and software usage.
- Encourage cross-functional training to increase team flexibility.
For example, training technicians to use predictive analytics tools can improve their ability to interpret sensor data and prevent failures.
7. Foster Collaboration and Communication
Effective communication between maintenance, production, and procurement teams ensures aligned priorities and faster issue resolution. A CMMS with in-app chat or collaboration tools, like EcoMaint, eliminates miscommunication and keeps everyone on the same page.
Key Actions:
- Hold daily or weekly meetings to discuss maintenance schedules and production needs.
- Use a CMMS to share real-time updates on task progress.
- Create feedback loops to incorporate insights from technicians and operators.
For instance, coordinating with production to schedule maintenance during low-demand periods minimizes disruptions and enhances efficiency.
VI. The Role of CMMS EcoMaint in Increasing Maintenance Efficiency
To achieve the strategies outlined above, a modern CMMS is indispensable. Vietsoft’s CMMS EcoMaint is a cloud-based solution designed to streamline maintenance operations, empower teams, and drive efficiency in Vietnam’s manufacturing sector. With features like automated work order management, real-time inventory tracking, predictive maintenance integration, and mobile access, EcoMaint transforms how maintenance is performed.
How EcoMaint Helps:
- Automates Preventive Maintenance: Schedules tasks based on time or usage, ensuring timely interventions.
- Enhances Data Insights: Provides customizable dashboards to monitor KPIs like MTTR, PMP, and OEE.
- Streamlines Inventory: Tracks spare parts in real time, preventing delays and overstocking.
- Improves Collaboration: Offers in-app communication tools for seamless team coordination.
- Supports Predictive Maintenance: Integrates with IoT sensors for real-time condition monitoring.
By adopting EcoMaint, companies can reduce downtime by up to 40%, extend asset life, and save significant costs. Curious to see how EcoMaint can transform your maintenance operations? Discover the CMMS EcoMaint solution here.
Contact us for consultation via hotline: 0986778578 or email: sales@vietsoft.com.vn.
VII. Conclusion
Increasing maintenance efficiency is a journey that requires a combination of proactive strategies, modern technology, and a skilled workforce. By implementing preventive and predictive maintenance, optimizing inventory, standardizing workflows, leveraging data, and fostering collaboration, organizations can reduce downtime, extend asset lifespans, and enhance safety. Tools like Vietsoft’s CMMS EcoMaint play a pivotal role in making these strategies accessible and effective, empowering maintenance teams to achieve operational excellence.