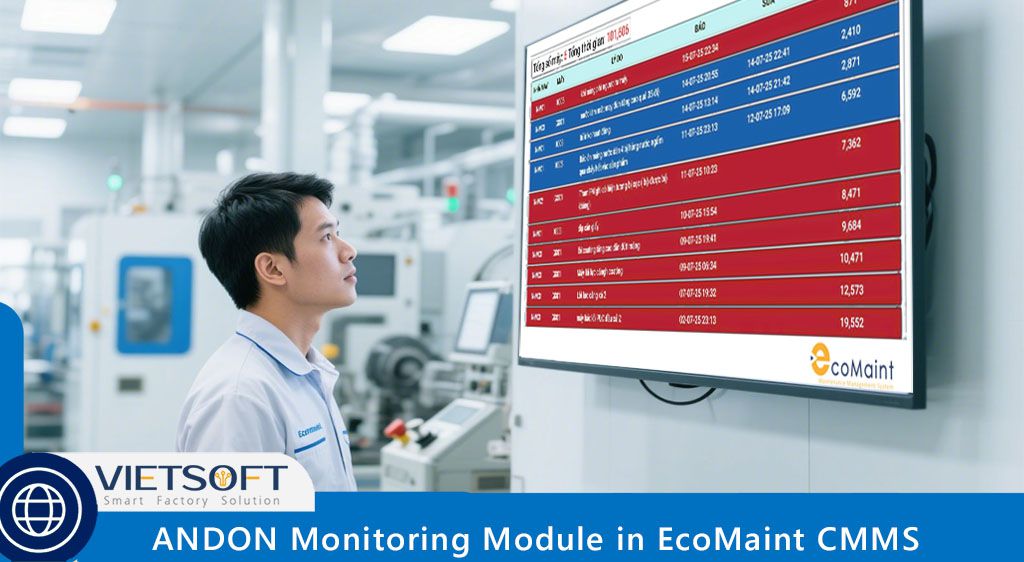
In the era of Industry 4.0, optimizing manufacturing and maintenance efficiency is paramount for any business aiming for success. Achieving this hinges on the ability to grasp the real-time operational status of machinery and equipment. That’s why Vietsoft proudly introduces the advanced ANDON Monitoring Module within its EcoMaint CMMS software—a groundbreaking solution designed to significantly enhance maintenance management and streamline operational processes for factories across Vietnam.
I. Unpacking the ANDON Monitoring Module in Modern Production
The Andon system is a well-established concept in the manufacturing sector, particularly within facilities embracing lean manufacturing philosophies. Fundamentally, Andon is a visual signaling system that provides immediate notifications regarding status, quality, or urgent issues on a production line or with specific equipment. With technological advancements, Andon has become deeply integrated into Computerized Maintenance Management Systems (CMMS) to offer a comprehensive and instantaneous overview.
The ANDON Monitoring Module in CMMS EcoMaint Software goes beyond simple alerts. It delivers a holistic view of equipment status through an intuitive web-application interface. This ensures that real-time information is displayed on LCD screens strategically placed throughout the factory, giving operational and maintenance teams quick, accurate insights into any issues or changes.
According to a 2023 report from the Vietnam Association of Supporting Industries (VASI), an average of 60% of manufacturing incidents are not detected promptly, leading to significant waste of time and resources. The Andon system is precisely the key to overcoming this pervasive challenge.
II. Why the ANDON Monitoring Module is Crucial for Your Factory
In today’s dynamic manufacturing landscape, unexpected equipment shutdowns are a primary cause of substantial losses in productivity and increased costs. The average cost per hour of unplanned downtime in large manufacturing plants in Vietnam can amount to tens, or even hundreds, of millions of Vietnamese Dong, depending on the industry. Delays in detecting and resolving these issues not only inflate expenses but also disrupt production schedules and damage a company’s reputation.
The ANDON Monitoring Module within EcoMaint provides an effective solution to mitigate these risks. By offering immediate and visual information, this module helps:
- Boost Response Capabilities: When an incident occurs, information is displayed instantly, enabling maintenance personnel to recognize and react swiftly, thereby minimizing downtime.
- Enhance Operational Transparency: Every team member in the factory, from operators to senior management, can easily grasp the overall status, fostering more effective coordination and collaboration.
- Improve Maintenance Efficiency: With real-time data at their fingertips, technicians can prioritize critical repairs, plan maintenance tasks more effectively, and optimize resource allocation.
- Ensure Accurate Data Collection: Every incident, including its reported time, start of repair, and completion time, is meticulously recorded. This provides invaluable data for continuous analysis and improvement initiatives.
III. Exploring the Superior Features of the ANDON Monitoring Module
The ANDON Monitoring Module in EcoMaint CMMS software is engineered with a user-friendly and robust web-application interface, offering flexible and comprehensive display capabilities. This means you can view data not only on computers but also on large LCD screens installed at strategic points throughout your facility.
1. Real-Time Equipment Status Display
One of the core functionalities of the ANDON Monitoring Module is its ability to show the operational status of machinery and equipment in real time. An intuitive dashboard will display crucial information such as:
- Operational Status: Whether a machine is running normally, stopped, or experiencing an issue.
- Fault Type/Reason for Downtime: Specific alerts detailing the cause of the problem (e.g., “hot gas backflow to machine,” “cooling coating error,” “control panel malfunction”).
- Fault Reported Time: The exact moment the error was logged.
- Repair Start Time: The point at which the maintenance team began intervention.
- Repair Completion Time: The moment the issue was fully resolved.
- Downtime Duration: The total minutes or hours the equipment was non-operational due to the incident.
With this rich data, management and maintenance teams can easily track and assess the performance of each machine, enabling them to make timely decisions for problem resolution.
2. Detailed Overview of Machine Breakdowns
The ANDON Monitoring Module provides an in-depth overview of Machine Breakdowns, allowing users to view detailed information about past incidents. For instance, this page can display:
- Total Machines Broken Down for the Day: Providing a summary figure of the overall impact of incidents.
- Total Downtime for the Day: Indicating the cumulative production interruption.
- Detailed Incident Information: Including machine name, breakdown report time, repair start time, completion time, acceptance time, and minutes of downtime.
This feature not only helps identify immediate hotspots requiring urgent attention but also provides crucial historical data for trend analysis, root cause identification, and the implementation of preventive measures. For example, if machine GK01 was down for 336 minutes on July 16, 2025, this information would be clearly displayed, allowing management to recognize the severity and demand immediate action.
IV. Vietsoft: Committed to Empowering Vietnamese Enterprises
With over two decades of experience in manufacturing and maintenance management software, Vietsoft is continuously dedicated to researching and developing advanced solutions tailored to the unique characteristics of the Vietnamese market. EcoMaint CMMS software, along with its latest ANDON Monitoring Module, exemplifies our commitment to providing powerful tools that help Vietnamese businesses optimize operations and enhance their competitive edge in the global integration landscape.
We understand that every factory has its own specific needs, which is why EcoMaint is designed with high customizability, easy integration with existing systems, and scalability to meet evolving business requirements. Vietsoft’s team of experts is always ready to provide support, consultation, and solution deployment to ensure our valued customers achieve maximum efficiency from the software.
V. Conclusion
In the intensely competitive manufacturing sector, optimizing maintenance processes is no longer an option but a mandatory requirement. The ANDON Monitoring Module within EcoMaint CMMS software serves as a powerful tool to empower Vietnamese businesses in achieving this. By offering a real-time overview of equipment status and the capability for rapid detection and response to incidents, this module not only minimizes downtime but also optimizes costs, boosts productivity, and ensures workplace safety.
Learn more about CMMS EcoMaint here. Contact us for consultation via hotline: 0986778578 or email: sales@vietsoft.com.vn.