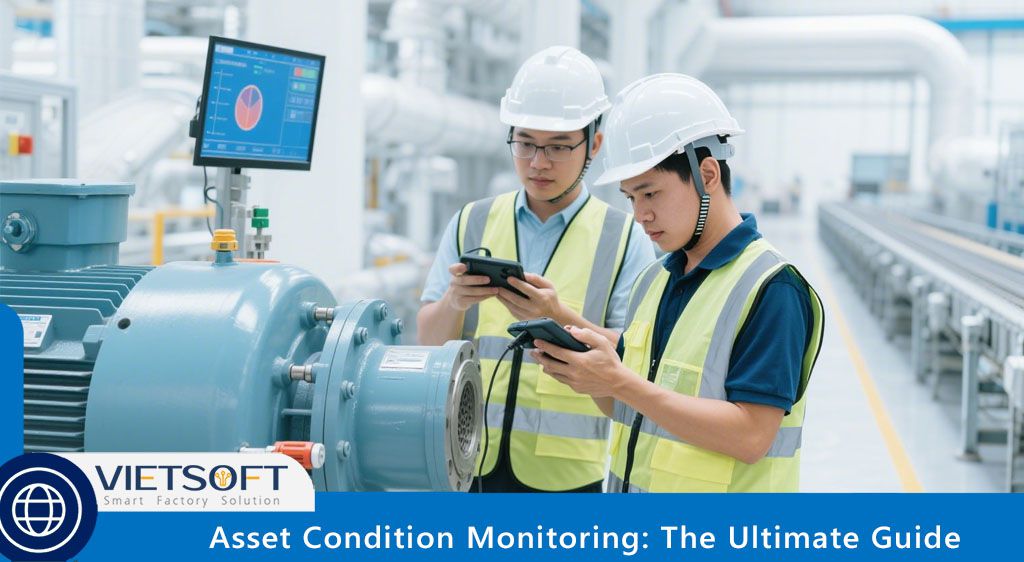
In today’s fast-paced industrial landscape, unexpected equipment failures can lead to costly downtime, safety risks, and reduced productivity. Imagine a production line halting because a critical motor fails without warning—disruptions like these can ripple across operations, impacting deadlines and budgets. Asset Condition Monitoring (ACM) is the solution to this challenge, offering a proactive approach to tracking equipment health and preventing failures before they occur. By leveraging real-time data and advanced technologies, businesses can optimize maintenance, extend asset lifespans, and boost operational efficiency.
This comprehensive guide explores what Asset Condition Monitoring is, why it’s critical for industries like manufacturing, energy, and transportation, and how to implement it effectively.
I. What is Asset Condition Monitoring?
Asset Condition Monitoring is the process of continuously or periodically assessing the health and performance of physical assets—such as machinery, equipment, or infrastructure—using data-driven techniques. By monitoring parameters like vibration, temperature, pressure, and fluid quality, businesses can detect early signs of wear, inefficiencies, or potential failures. This proactive approach allows for timely maintenance, reducing the risk of unexpected breakdowns and optimizing asset performance.
Unlike traditional reactive maintenance, where repairs are made after a failure, ACM focuses on predictive and preventive strategies. It uses sensors, IoT devices, and analytical software to gather real-time data, enabling maintenance teams to make informed decisions based on actual asset conditions rather than fixed schedules or guesswork.
II. Why Asset Condition Monitoring Matters
Asset Condition Monitoring is a cornerstone of modern maintenance strategies, offering significant advantages across industries. Here’s why it’s indispensable:
- Prevent Downtime: By identifying issues before they escalate, ACM minimizes unplanned outages, keeping operations running smoothly.
- Reduce Costs: Proactive maintenance reduces the need for emergency repairs and extends equipment lifespan, saving on replacement costs.
- Enhance Safety: Early detection of faults like overheating or structural stress reduces workplace hazards, protecting employees and assets.
- Optimize Performance: Continuous monitoring ensures equipment operates at peak efficiency, reducing energy waste and boosting productivity.
- Data-Driven Decisions: Real-time insights enable better planning for repairs, replacements, and resource allocation.
In industries like oil and gas, where downtime can cost millions, or manufacturing, where precision is critical, ACM is not just beneficial—it’s essential.
III. Key Elements of Asset Condition Monitoring
Effective Asset Condition Monitoring relies on collecting and analyzing various types of data to assess equipment health comprehensively. Below are the five key elements commonly used in ACM programs:
1. Vibration Analysis
Vibration analysis measures the frequency and intensity of vibrations in rotating machinery, such as motors, pumps, or turbines. Excessive or irregular vibrations can indicate issues like misalignment, imbalance, or bearing wear. By using sensors to track vibration patterns, maintenance teams can pinpoint problems early and schedule repairs before failures occur.
For instance, a sudden increase in vibration in a turbine might suggest bearing degradation, prompting technicians to lubricate or replace the component during planned downtime.
2. Thermography
Thermography uses infrared cameras to detect abnormal heat patterns in equipment. Overheating can signal issues like electrical faults, worn components, or inadequate lubrication. By monitoring temperature changes, businesses can address problems like motor overloads or circuit breaker issues before they lead to failures or safety hazards.
For example, in an electrical substation, thermography can identify hot spots in transformers, allowing for timely interventions to prevent outages.
3. Oil Analysis
Oil analysis involves testing lubricants and hydraulic fluids for contaminants, wear particles, or chemical degradation. This technique is critical for machinery like engines or gearboxes, where fluid quality directly impacts performance. Detecting metal particles in oil, for instance, can indicate internal component wear, while water contamination might suggest seal failures.
Regular oil analysis ensures machinery operates smoothly and helps predict maintenance needs, reducing the risk of costly repairs.
4. Ultrasonic Testing
Ultrasonic testing uses high-frequency sound waves to detect leaks, electrical discharges, or mechanical faults. This method is ideal for identifying subtle issues, such as gas leaks or bearing friction, that other techniques might miss. For example, ultrasonic sensors can detect air leaks in compressed air systems, improving energy efficiency and reducing operational costs.
5. Visual Inspections
While technology-driven, ACM also includes visual inspections to identify visible signs of wear, corrosion, or damage. Regular checks by trained technicians can catch issues like cracks in structural components or leaks in pipelines, complementing data from sensors.
By combining these elements, businesses gain a holistic view of asset health, enabling proactive maintenance and informed decision-making.
IV. Benefits of Asset Condition Monitoring
Implementing Asset Condition Monitoring delivers measurable benefits that enhance operational efficiency and reduce costs. Here are eight key advantages:
1. Optimize Asset Performance
ACM provides real-time insights into how equipment is performing compared to historical data. By identifying inefficiencies, such as a motor running hotter than usual, businesses can make adjustments to optimize performance and reduce energy consumption.
2. Prevent Unplanned Downtime
Early detection of issues allows maintenance to be scheduled during off-hours, avoiding disruptions to production. For example, a monitored pump showing abnormal pressure readings can be serviced before it fails, keeping operations on track.
3. Increase Visibility
Continuous monitoring provides a clear picture of asset health, enabling maintenance teams to address issues proactively. Dashboards and alerts offer real-time updates, ensuring no problem goes unnoticed.
4. Monitor Remote Assets
For assets in hard-to-reach locations, like offshore wind turbines or underground pipelines, ACM enables remote monitoring, reducing the need for on-site inspections and saving time and resources.
5. Enable Predictive Maintenance
By analyzing data trends, ACM supports predictive maintenance, allowing businesses to address issues based on actual conditions rather than fixed schedules. This reduces unnecessary maintenance and lowers costs.
6. Minimize Downtime
Proactive interventions based on ACM data ensure minimal interruptions, boosting overall productivity. For instance, scheduling repairs during planned maintenance windows avoids costly production halts.
7. Enhance Safety
Faulty equipment can pose risks to workers. ACM identifies hazards like overheating machinery or structural weaknesses, ensuring a safer workplace and compliance with safety regulations.
8. Real-Time Alerts
Automated systems send instant notifications when anomalies are detected, enabling rapid response. For example, a temperature spike in a compressor can trigger an alert, allowing technicians to act before damage occurs.
V. Advanced Technologies in Asset Condition Monitoring
Modern Asset Condition Monitoring leverages cutting-edge technologies to enhance accuracy and efficiency. Here are the key technologies driving ACM forward:
1. Industrial IoT (IIoT)
IIoT connects sensors and devices to collect and transmit data in real time. By integrating data from multiple sources, such as SCADA systems and asset management’software, IIoT provides end-to-end visibility into asset performance. For example, Eldorado Brasil used an IIoT-based system to detect bearing failure in a pump motor, saving $1.8 million by avoiding unplanned downtime.
2. Inspection Drones
Drones equipped with cameras, ultrasonic sensors, or LiDAR can inspect hard-to-reach assets like bridges or storage tanks. They reduce inspection costs and improve data accuracy. For instance, a UK authority saved £1 million by using drones for bridge inspections, identifying corrosion early.
3. Machine Learning and AI
Machine learning algorithms analyze historical and real-time data to predict failures and recommend maintenance actions. In mining, Razor Labs’ AI platform reduced downtime by 25% by predicting conveyor failures. AI-driven models also optimize maintenance schedules, reducing manual inspections.
4. Digital Twins
Digital twins create virtual replicas of physical assets, allowing real-time monitoring and scenario modeling. For example, a digital twin of a solar farm can optimize panel positioning based on weather data, improving energy output and maintenance planning.
VI. Challenges in Traditional Asset Condition Monitoring
While Asset Condition Monitoring offers significant benefits, traditional systems face challenges:
- Manual Data Collection: Manual inspections are time-consuming and prone to human error.
- Limited Real-Time Insights: Older systems often lack real-time analytics, delaying issue detection.
- High Costs: Specialized tools and frequent inspections can be expensive.
- Remote Asset Access: Monitoring assets in remote locations is logistically challenging without advanced technology.
Modern solutions, like mobile EAM systems and IoT integration, address these challenges by enabling real-time data access and automated analytics.
VII. How CMMS EcoMaint Enhances Asset Condition Monitoring
To overcome the limitations of traditional ACM, Vietsoft’s CMMS EcoMaint offers a powerful solution for modern maintenance management. This cloud-based software integrates seamlessly with IoT sensors and mobile devices, providing real-time insights into asset health. Key features include:
- Real-Time Monitoring: EcoMaint collects data from sensors to track vibration, temperature, and other parameters, displaying them on user-friendly dashboards.
- Predictive Analytics: The software analyzes trends to predict failures, enabling proactive maintenance planning.
- Mobile Access: Technicians can access asset data and log inspections from anywhere, even offline, ensuring flexibility for remote operations.
- Automated Alerts: Instant notifications alert teams to anomalies, reducing response times and preventing downtime.
- Integration with ERP Systems: EcoMaint integrates with platforms like SAP or Oracle, streamlining data flow and maintenance workflows.
By implementing CMMS EcoMaint, businesses can transform their Asset Condition Monitoring strategy, achieving greater efficiency and reliability. Explore the CMMS EcoMaint solution here.
Contact us for consultation via hotline: 0986778578 or email: sales@vietsoft.com.vn.
VIII. How to Implement an Asset Condition Monitoring Program
Building an effective Asset Condition Monitoring program requires a structured approach. Here are the key steps:
1. Step 1: Gather Historical Data
Collect data on past maintenance, repairs, and equipment performance. Manufacturer documentation and historical records provide insights into normal operating conditions and potential failure points.
2. Step 2: Install Sensors
Deploy sensors to monitor critical parameters like vibration, temperature, and pressure. Ensure sensors are placed strategically to capture accurate data. For example, vibration sensors on rotating equipment should be positioned near bearings or critical components.
3. Step 3: Establish Baselines
Use initial sensor data to set baseline measurements for each asset. These baselines represent normal operating conditions, allowing you to detect deviations that indicate potential issues.
4. Step 4: Continuous Monitoring and Analysis
Implement software like CMMS EcoMaint to collect and analyze sensor data in real time. Regularly review trends and set thresholds for alerts to ensure timely interventions.
5. Step 5: Act on Insights
Use data insights to schedule maintenance, prioritize repairs, or plan replacements. For example, if vibration levels exceed 60% of the allowable limit, schedule an inspection; at 80%, plan a repair or replacement.
IX. Practical Example: Applying Asset Condition Monitoring
Consider a manufacturing plant with a critical pump used in production. By implementing Asset Condition Monitoring:
- Sensors Installed: Vibration and temperature sensors are placed on the pump.
- Baseline Set: Normal vibration levels are established at 0.5 mm/s, and the operating temperature is 40°C.
- Monitoring: Over a month, vibration increases to 0.8 mm/s, and the temperature rises to 50°C, triggering an alert.
- Action Taken: Technicians inspect the pump, identify a misaligned shaft, and correct it during a planned maintenance window, avoiding a shutdown.
Using CMMS EcoMaint, the plant tracks these metrics, receives real-time alerts, and logs maintenance actions, ensuring seamless operations.
X. The Future of Asset Condition Monitoring
As technology evolves, Asset Condition Monitoring is becoming more sophisticated. Emerging trends include:
- AI-Powered Predictive Models: Advanced algorithms will predict failures with greater accuracy, reducing maintenance costs further.
- Augmented Reality (AR): AR tools will allow technicians to visualize asset data in real-time during inspections.
- Blockchain for Data Integrity: Blockchain can ensure secure, tamper-proof data collection for compliance and auditing.
These advancements will make ACM more accessible and effective, driving even greater efficiency and reliability.
XI. Final Thoughts
Asset Condition Monitoring is a game-changer for industries reliant on machinery and infrastructure. By proactively tracking equipment health, businesses can prevent downtime, reduce costs, enhance safety, and optimize performance. With solutions like Vietsoft’s CMMS EcoMaint, implementing ACM has never been easier, offering real-time insights and predictive capabilities to keep your operations running smoothly.
Ready to transform your maintenance strategy? Discover how CMMS EcoMaint can help you monitor assets effectively, reduce downtime, and boost efficiency. Start your journey to smarter asset management today!