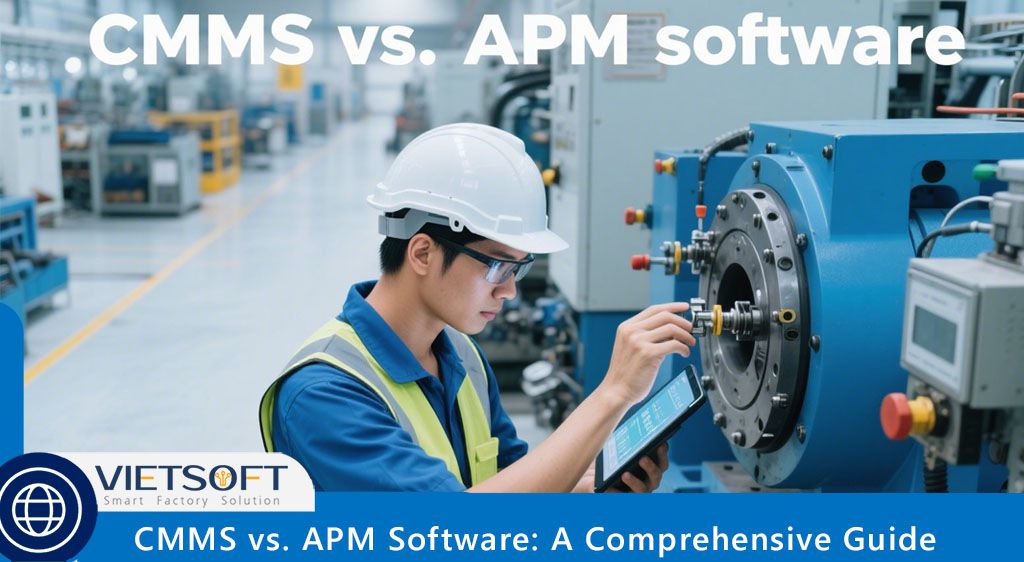
In the ever-evolving landscape of industrial operations, optimizing asset performance and maintenance processes is critical for businesses aiming to stay competitive. Two powerful tools that have transformed how organizations manage their assets are Computerized Maintenance Management Systems (CMMS) and Asset Performance Management (APM) software. While both systems aim to enhance operational efficiency, they serve distinct purposes and offer unique functionalities. This article provides an in-depth exploration of CMMS vs. APM Software, highlighting their differences, similarities, and how they can work together to drive business success.
I. What is CMMS Software?
1. Definition and Core Functions of CMMS
Computerized Maintenance Management System (CMMS) software is a digital platform designed to streamline and automate maintenance operations. It acts as a centralized hub for managing assets, scheduling preventive maintenance, tracking work orders, and overseeing inventory. The primary goal of CMMS is to reduce equipment downtime, extend asset lifecycles, and improve operational efficiency.
Key features of CMMS software include:
- Work Order Management: Automates the creation, assignment, and tracking of maintenance tasks.
- Preventive Maintenance Scheduling: Enables proactive maintenance to prevent unexpected failures.
- Inventory Management: Tracks spare parts and ensures availability for repairs.
- Reporting and Analytics: Generates insights into maintenance performance, costs, and asset health.
2. Benefits of CMMS for Maintenance Teams
CMMS software empowers maintenance teams by:
- Reducing manual paperwork and improving workflow efficiency.
- Providing real-time visibility into maintenance activities.
- Enhancing communication between departments, such as maintenance and procurement.
- Supporting data-driven decisions through comprehensive reports.
II. What is APM Software?
1. Definition and Core Functions of APM
Asset Performance Management (APM) software takes a more strategic approach to asset management by focusing on optimizing the performance, reliability, and longevity of critical assets. Unlike CMMS, which focuses on day-to-day maintenance, APM leverages advanced technologies like predictive analytics, machine learning, and Internet of Things (IoT) data to monitor asset health in real time and predict potential failures.
Key features of APM software include:
- Asset Condition Monitoring: Uses sensors to track metrics like vibration, temperature, and pressure.
- Predictive Maintenance: Analyzes historical and real-time data to forecast equipment failures.
- Root Cause Analysis: Identifies underlying issues to prevent recurring problems.
- Integration with Enterprise Systems: Connects with ERP, SCADA, and IoT platforms for a holistic view of operations.
2. Benefits of APM for Asset-Intensive Industries
APM software is particularly valuable in industries with high-value assets, such as oil and gas, energy, and transportation. Its benefits include:
- Maximizing asset uptime through predictive insights.
- Reducing maintenance costs by addressing issues before they escalate.
- Enhancing safety by identifying potential risks in critical equipment.
- Aligning maintenance strategies with broader business objectives.
III. CMMS vs. APM Software: Key Differences
While both CMMS and APM aim to improve asset management, their scopes, functionalities, and applications differ significantly. Below, we explore the primary differences between CMMS vs. APM Software to help organizations choose the right solution for their needs.
1. Scope of Functionality
CMMS Software:
- Focuses on operational maintenance tasks, such as work order management, scheduling, and inventory control.
- Streamlines day-to-day maintenance activities to ensure assets are functional and compliant.
APM Software:
- Emphasizes strategic asset performance optimization using advanced analytics and predictive tools.
- Monitors asset health in real time to prevent failures and improve long-term reliability.
Key Takeaway: CMMS is tactical, focusing on maintenance execution, while APM is strategic, aiming to enhance overall asset performance.
2. Data Utilization and Analytics
CMMS Software:
- Collects and stores maintenance-related data, such as work order history and inventory levels.
- Provides basic analytics and reports to track maintenance performance and costs.
APM Software:
- Leverages advanced analytics, machine learning, and IoT data to provide real-time insights into asset health.
- Uses predictive models to forecast failures and optimize maintenance schedules.
Key Takeaway: CMMS offers foundational data management, while APM provides advanced, predictive analytics for proactive decision-making.
3. Integration and Connectivity
CMMS Software:
- Integrates with systems like ERP and accounting to streamline maintenance workflows.
- Focuses on internal maintenance data, such as work orders and inventory records.
APM Software:
- Connects with a broader range of data sources, including IoT devices, SCADA systems, and external databases.
- Provides a holistic view of asset performance across the organization.
Key Takeaway: CMMS focuses on maintenance-specific integrations, while APM offers broader connectivity for comprehensive asset insights.
4. Focus on Optimization
CMMS Software:
- Optimizes maintenance processes by automating scheduling, tracking costs, and managing spare parts.
- Reduces downtime through preventive maintenance and efficient work order management.
APM Software:
- Optimizes overall asset performance by predicting failures and improving utilization.
- Uses data-driven insights to align maintenance with business goals, such as sustainability and cost reduction.
Key Takeaway: CMMS optimizes maintenance operations, while APM enhances asset performance and strategic outcomes.
5. Industry Applications
CMMS Software:
- Ideal for organizations with routine maintenance needs, such as manufacturing, healthcare, and facilities management.
- Best suited for managing physical assets and ensuring operational efficiency.
- Example: A university uses CMMS to maintain campus facilities, scheduling repairs for HVAC systems and tracking maintenance costs.
APM Software:
- Suited for asset-intensive industries like energy, oil and gas, and transportation, where downtime is costly.
- Focuses on high-value, critical assets requiring continuous monitoring and optimization.
- Example: A railway company uses APM to monitor the health of locomotives, predicting maintenance needs to ensure safe and reliable operations.
Key Takeaway: CMMS is versatile for general maintenance, while APM is specialized for high-stakes, asset-heavy environments.
IV. Overlaps Between CMMS and APM Software
Despite their differences, CMMS and APM software share common goals and functionalities, making them complementary tools in many scenarios. Below are key areas where CMMS vs. APM Software overlap:
1. Asset Management
Both systems focus on managing assets, though their approaches differ. CMMS tracks maintenance activities and asset history, while APM monitors performance and predicts failures. Together, they provide a comprehensive view of asset health and maintenance needs.
2. Preventive and Predictive Maintenance
CMMS supports preventive maintenance by scheduling regular inspections and repairs. APM takes this further with predictive maintenance, using data analytics to forecast failures. Both approaches aim to reduce downtime and improve reliability.
3. Data-Driven Decision Making
Both systems collect and analyze data to support informed decisions. CMMS provides reports on maintenance performance, while APM offers insights into asset health and performance trends.
4. Integration with Enterprise Systems
Both CMMS and APM integrate with ERP, IoT, and other systems to streamline workflows and enhance visibility. This connectivity ensures that maintenance and performance data align with broader business objectives.
5. Example of Combined Use
A manufacturing plant might use CMMS to manage daily maintenance tasks, such as scheduling oil changes for machines, while using APM to monitor real-time data from sensors, predicting when a machine is likely to fail. By combining both systems, the plant achieves operational efficiency and long-term asset reliability.
V. CMMS vs. APM Software: Which is Right for Your Organization?
Choosing between CMMS and APM—or deciding to use both—depends on your organization’s needs, industry, and goals. Here’s a breakdown to guide your decision:
1. When to Choose CMMS Software
- Best For: Organizations focused on streamlining maintenance operations and managing routine tasks.
- Industries: Manufacturing, healthcare, facilities management, transportation.
- Use Case: A small to medium-sized factory that needs to automate work orders and track maintenance costs.
2. When to Choose APM Software
- Best For: Asset-intensive organizations aiming to optimize performance and prevent costly downtime.
- Industries: Energy, oil and gas, aerospace, mining.
- Use Case: A power plant that needs to monitor turbine performance in real time and predict maintenance needs.
3. When to Use Both
- Best For: Organizations with complex asset management needs that require both operational efficiency and strategic optimization.
- Use Case: A large manufacturing company that uses CMMS for daily maintenance tasks and APM to monitor critical equipment performance.
VI. How CMMS EcoMaint Bridges the Gap
For organizations seeking a robust solution to manage maintenance operations effectively, CMMS EcoMaint by Vietsoft offers a powerful and user-friendly platform tailored to the Vietnamese market. EcoMaint streamlines work order management, preventive maintenance scheduling, and inventory tracking, making it an ideal choice for industries like manufacturing, healthcare, and facilities management. Its intuitive interface and comprehensive reporting tools empower maintenance teams to reduce downtime, optimize resources, and ensure compliance.
What sets EcoMaint apart is its ability to integrate with advanced technologies, paving the way for organizations to transition toward predictive maintenance and asset performance optimization. By adopting EcoMaint, businesses can lay a strong foundation for maintenance management while preparing for future integration with APM solutions. Curious about how EcoMaint can transform your maintenance operations? Learn more about CMMS EcoMaint here.
Contact us via hotline: 0986778578 or email: sales@vietsoft.com.vn.
VII. Practical Examples of CMMS and APM in Action
1. Example 1: CMMS in a Manufacturing Plant
A medium-sized factory uses CMMS to manage its production equipment. The system schedules monthly inspections for conveyor belts, tracks repair histories, and ensures spare parts are available. When a belt shows signs of wear, the CMMS generates a work order, assigns it to a technician, and updates inventory levels after the repair. This proactive approach reduces downtime by 20% and ensures compliance with safety regulations.
2. Example 2: APM in an Energy Facility
A wind farm uses APM to monitor turbine performance. Sensors track vibration, temperature, and rotational speed, feeding data into the APM system. When an anomaly is detected, the system predicts a potential bearing failure and alerts the maintenance team. By addressing the issue early, the wind farm avoids a $50,000 outage and extends the turbine’s lifespan by two years.
3. Example 3: Combined CMMS and APM in a Transportation Company
A railway company uses CMMS to schedule routine maintenance for its trains, such as brake inspections and oil changes. Simultaneously, APM monitors real-time data from onboard sensors, predicting when critical components, like wheel bearings, are likely to fail. By integrating both systems, the company reduces maintenance costs by 15% and improves train availability by 10%.
VIII. Advanced Considerations for CMMS vs. APM Software
1. Scalability and Flexibility
- CMMS: Typically easier to implement and scale for small to medium-sized organizations. It requires less initial investment and is ideal for businesses starting their digital transformation journey.
- APM: More complex and resource-intensive, requiring significant data infrastructure and expertise. It’s best suited for large organizations with complex assets and existing IoT capabilities.
2. Cost Implications
- CMMS: Generally more affordable, with costs focused on software licenses, implementation, and training. For example, a CMMS like EcoMaint offers cost-effective solutions for businesses of all sizes.
- APM: Higher upfront costs due to the need for sensors, advanced analytics, and integration with IoT systems. However, the return on investment can be significant in asset-intensive industries.
3. Implementation Time
- CMMS: Can be implemented in weeks to months, depending on the organization’s size and complexity. For instance, EcoMaint’s implementation typically takes 8–12 weeks.
- APM: Requires longer implementation periods (often 10–20 weeks) due to the need for sensor installation, data integration, and staff training.
IX. Future Trends in CMMS and APM Software
As technology evolves, both CMMS and APM software are becoming more sophisticated. Here are some trends to watch in 2025 and beyond:
· Artificial Intelligence and Machine Learning: APM systems are increasingly incorporating AI to improve predictive accuracy, while CMMS platforms are adopting AI for smarter scheduling and resource allocation.
· IoT Integration: Both systems are leveraging IoT for real-time data collection, enabling more accurate monitoring and maintenance.
· Mobile Accessibility: Modern CMMS and APM solutions offer mobile apps, allowing technicians to access work orders and asset data on the go.
· Sustainability Focus: APM systems are aligning with sustainability goals by optimizing energy usage and reducing waste, while CMMS platforms support efficient resource management.
· Cloud-Based Solutions: Cloud-hosted CMMS and APM systems, like EcoMaint, offer scalability, accessibility, and reduced IT overhead.
X. Conclusion
In the debate of CMMS vs. APM Software, there’s no one-size-fits-all answer. CMMS excels at streamlining maintenance operations, making it ideal for organizations focused on efficiency and compliance. APM, with its advanced analytics and predictive capabilities, is perfect for asset-intensive industries aiming to maximize performance and reliability. For many organizations, combining both systems offers the best of both worlds, providing operational efficiency and strategic insights.