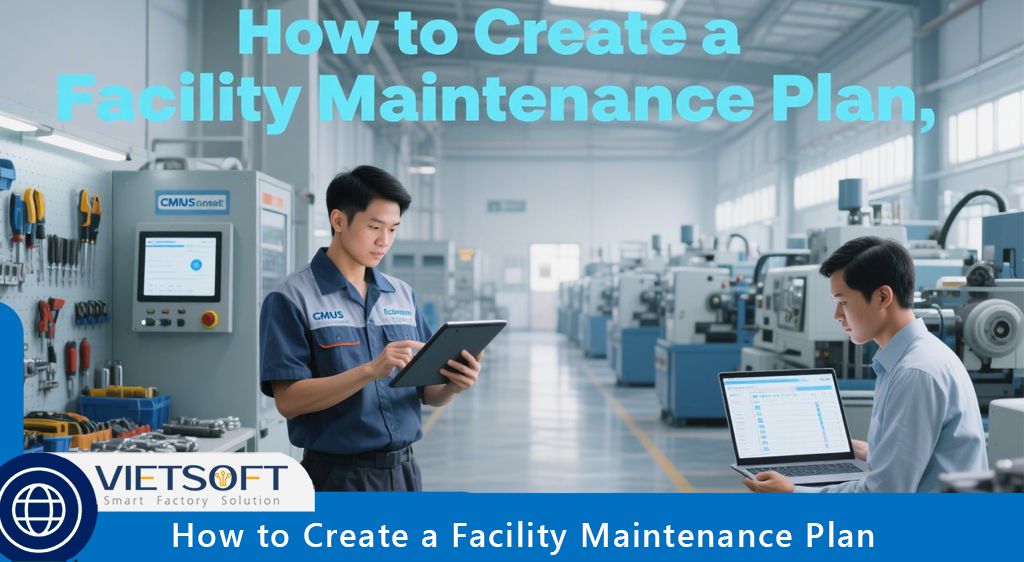
A well-crafted facility maintenance plan is the backbone of efficient facility management, ensuring that buildings, equipment, and critical systems operate at peak performance. For organizations in Vietnam and beyond, managing assets effectively is crucial to minimizing downtime, reducing costs, and ensuring a safe and productive environment. This guide provides a detailed roadmap for creating a facility maintenance plan.
I. What is a Facility Maintenance Plan?
A facility maintenance plan is a strategic framework designed to manage and maintain a facility’s physical assets, including equipment, infrastructure, and building systems. It outlines schedules, procedures, and responsibilities for preventive maintenance, inspections, and repairs to ensure optimal performance and longevity of assets. Unlike reactive maintenance, which addresses issues after they occur, a facility maintenance plan emphasizes proactive measures to prevent breakdowns, reduce costs, and enhance safety.
This plan serves as a blueprint for facility managers to streamline operations, comply with safety regulations, and align maintenance activities with organizational goals. By implementing a structured approach to create a facility maintenance plan, businesses can avoid costly disruptions and maintain a competitive edge in industries such as manufacturing, healthcare, or commercial real estate.
II. Why is a Facility Maintenance Plan Important?
A facility maintenance plan is not just a checklist; it’s a strategic tool that drives operational excellence. Here’s why it’s critical for organizations:
- Cost Savings: Preventive maintenance reduces the likelihood of expensive emergency repairs. Studies estimate that proactive maintenance can save businesses 12-18% compared to reactive approaches.
- Extended Asset Lifespan: Regular servicing minimizes wear and tear, allowing equipment and infrastructure to operate longer without replacement.
- Enhanced Safety: Routine inspections ensure compliance with safety standards, reducing workplace hazards and potential legal penalties.
- Improved Productivity: By minimizing downtime, a maintenance plan keeps operations running smoothly, allowing employees to focus on core tasks.
- Sustainability: Efficiently maintained systems consume less energy, reducing utility costs and supporting environmental goals.
III. Benefits of Creating a Facility Maintenance Plan
Understanding the advantages of a facility maintenance plan underscores its necessity. Below are the key benefits, explained in detail to provide actionable insights for maintenance professionals:
1. Prolongs Asset Lifespan
Every piece of equipment has a finite lifespan, but neglect can accelerate deterioration. A facility maintenance plan incorporates regular inspections and servicing to address wear and tear proactively. For instance, maintaining HVAC systems by cleaning filters and checking refrigerant levels can extend their operational life by years, maximizing return on investment.
2. Reduces Operational Costs
Unplanned repairs can strain budgets, often costing significantly more than scheduled maintenance. A facility maintenance plan identifies potential issues early, allowing for cost-effective interventions. For example, replacing a worn belt in a conveyor system during a scheduled maintenance window is far cheaper than addressing a complete system failure.
3. Enhances Safety and Compliance
Poorly maintained facilities pose safety risks, from faulty electrical systems to malfunctioning fire alarms. A facility maintenance plan ensures regular checks to meet safety codes, protecting employees and avoiding fines. In Vietnam, compliance with TCVN (Vietnam National Standards) for workplace safety is critical, and a well-executed plan helps achieve this.
4. Boosts Operational Efficiency
Equipment failures disrupt workflows, leading to lost productivity. A facility maintenance plan minimizes these interruptions by ensuring systems operate reliably. For instance, a hospital maintaining its medical equipment ensures uninterrupted patient care, enhancing overall efficiency.
5. Promotes Sustainability
Efficient systems consume less energy and produce less waste. A facility maintenance plan optimizes equipment performance, such as ensuring HVAC systems run at peak efficiency, which reduces energy costs and supports sustainability goals. This is particularly relevant in Vietnam, where businesses are increasingly adopting green practices to meet global standards.
IV. Key Components of a Facility Maintenance Plan
To create a facility maintenance plan that delivers results, several core components must be included. These elements ensure the plan is comprehensive and actionable:
1. Asset Inventory and Assessment
A detailed inventory of all assets—equipment, machinery, and building systems—is the foundation of a facility maintenance plan. Include details such as asset type, location, condition, and maintenance history. Categorizing assets by criticality (e.g., critical production equipment vs. non-essential fixtures) helps prioritize maintenance tasks. Tools like CMMS EcoMaint can streamline this process by providing a centralized database for asset management.
2. Preventive Maintenance Schedule
A preventive maintenance schedule outlines regular inspections and servicing tasks to prevent failures. For example, scheduling quarterly checks for air conditioning units or monthly lubrication for machinery can catch issues early. This schedule should align with manufacturer recommendations and operational needs.
3. Standard Operating Procedures (SOPs)
SOPs standardize maintenance tasks, ensuring consistency and efficiency. They outline step-by-step procedures for tasks like equipment servicing, safety checks, and emergency responses. For instance, an SOP for inspecting a generator might include checking fuel levels, testing battery voltage, and recording results.
4. Budgeting and Resource Allocation
A well-funded maintenance plan prevents delays due to insufficient resources. Budget for routine maintenance, emergency repairs, and spare parts inventory. Allocate resources efficiently by forecasting needs based on asset usage and condition.
5. Staffing and Role Assignment
Clearly defined roles ensure accountability. Assign tasks based on technician expertise and availability. For example, a senior technician might handle complex machinery repairs, while a junior technician performs routine inspections. Outsourcing non-critical tasks to vendors can also optimize resources.
6. Integration of CMMS Software
A Computerized Maintenance Management System (CMMS) like CMMS EcoMaint is a game-changer for facility maintenance. It automates work order management, tracks asset performance, and provides real-time insights. For instance, CMMS EcoMaint can send alerts for upcoming maintenance tasks, reducing the risk of oversight.
V. Steps to Create a Facility Maintenance Plan
Creating a facility maintenance plan requires a structured approach. Below are the detailed steps to guide you through the process, optimized for clarity and SEO:
1. Step 1: Conduct a Comprehensive Facility Audit
Begin by assessing the facility’s current condition. Inspect all systems—HVAC, electrical, plumbing, and structural components—to identify maintenance needs. Document asset conditions and prioritize those critical to operations. For example, a data center might prioritize cooling systems to prevent server overheating.
2. Step 2: Build an Asset Inventory
Create a detailed registry of all assets, including specifications, maintenance history, and criticality. Use CMMS EcoMaint to digitize this inventory, making it easy to update and access. For instance, a manufacturing plant might list CNC machines, noting their model, age, and last service date.
3. Step 3: Define Maintenance Strategies
Choose a mix of maintenance approaches:
- Preventive Maintenance: Regular servicing to prevent failures (e.g., monthly filter replacements).
- Predictive Maintenance: Using data from IoT sensors or CMMS to predict failures (e.g., vibration analysis for motors).
- Reactive Maintenance: Addressing issues as they occur, reserved for non-critical assets.
A balanced approach, leaning heavily on preventive and predictive methods, ensures efficiency. For example, predictive maintenance can reduce downtime by 30% in high-traffic facilities.
4. Step 4: Develop a Maintenance Schedule
Create a schedule for daily, weekly, monthly, and annual maintenance tasks. Align with manufacturer guidelines and operational demands. For instance, a commercial building might schedule weekly fire alarm tests and quarterly HVAC inspections. Use CMMS EcoMaint to automate scheduling and send reminders.
5. Step 5: Allocate Budget and Resources
Estimate costs for labor, parts, and emergency repairs. Allocate funds strategically, ensuring critical assets are prioritized. For example, a hospital might allocate 15% of its budget to medical equipment maintenance to ensure patient safety. Maintain a reserve for unexpected repairs to avoid disruptions.
6. Step 6: Implement a Work Order System
A work order system tracks maintenance requests and ensures timely completion. Use CMMS EcoMaint to create, assign, and monitor work orders. For example, a technician receiving a work order to repair a faulty pump can access detailed instructions and update progress in real-time.
7. Step 7: Train Staff and Establish SOPs
Train maintenance teams on procedures, safety protocols, and CMMS usage. SOPs ensure consistency, reducing errors. For instance, an SOP for electrical panel maintenance might include steps for locking out power, testing circuits, and documenting results.
8. Step 8: Monitor and Optimize the Plan
Track key performance indicators (KPIs) like Mean Time Between Failures (MTBF) and Mean Time to Repair (MTTR) to evaluate the plan’s effectiveness. For example:
- MTBF = Total operational hours ÷ Number of failures
- MTTR = Total downtime hours ÷ Number of repairs
Use CMMS EcoMaint to generate reports and identify areas for improvement. Regularly update the plan based on performance data and changing facility needs.
VI. Best Practices for a Resilient Facility Maintenance Plan
To ensure your facility maintenance plan is effective and sustainable, follow these best practices:
1. Leverage Data and Analytics
Use data from CMMS and IoT devices to predict failures and optimize schedules. For example, analyzing motor vibration data can predict bearing failures, allowing proactive repairs.
2. Conduct Regular Inspections
Schedule routine inspections to catch issues early. For instance, monthly checks of plumbing systems can prevent costly leaks.
3. Standardize Processes
SOPs and checklists ensure consistency. For example, a checklist for HVAC maintenance might include inspecting filters, checking belts, and testing airflow.
4. Integrate Advanced Technology
Combine CMMS with IoT for real-time monitoring. CMMS EcoMaint integrates with IoT sensors to track equipment performance, reducing downtime by up to 20%.
5. Prepare for Emergencies
Develop an emergency response plan for critical failures, such as power outages or equipment breakdowns. Include evacuation routes, contact lists, and backup systems.
VII. Common Mistakes to Avoid
Avoid these pitfalls to ensure your facility maintenance plan succeeds:
- Lack of Documentation: Failing to record maintenance activities leads to oversight. Use CMMS EcoMaint to maintain detailed records.
- Neglecting Preventive Maintenance: Relying solely on reactive maintenance increases costs and downtime.
- Underfunding Maintenance: Insufficient budgets lead to deferred maintenance, causing larger issues.
- Ignoring Technology: Manual tracking is error-prone. Adopt CMMS EcoMaint for automation and efficiency.
VIII. How CMMS EcoMaint Enhances Your Facility Maintenance Plan
For businesses in Vietnam, CMMS EcoMaint by Vietsoft is a powerful tool to streamline facility maintenance. This cloud-based software offers features like:
- Automated Work Orders: Create and track work orders with ease, ensuring timely task completion.
- Real-Time Asset Monitoring: Monitor equipment performance and receive alerts for potential issues.
- Data-Driven Insights: Generate reports on KPIs like MTBF and MTTR to optimize maintenance strategies.
- Mobile Access: Technicians can access tasks and update progress on the go, improving efficiency.
By integrating CMMS EcoMaint, businesses can reduce downtime by 25%, cut maintenance costs by 15%, and improve compliance with safety standards. Learn more about CMMS EcoMaint here.
Contact us for consultation via hotline: 0986778578 or email: sales@vietsoft.com.vn
IX. Conclusion
Creating a facility maintenance plan is a strategic investment in operational efficiency, safety, and sustainability. By following the steps outlined—conducting audits, building asset inventories, defining strategies, and leveraging tools like CMMS EcoMaint—businesses can minimize downtime, extend asset lifespans, and reduce costs. A well-executed plan not only protects investments but also enhances workplace safety and productivity, making it indispensable for modern facility management.
Ready to take your maintenance strategy to the next level? Start building your facility maintenance plan today with CMMS EcoMaint and see the difference a proactive approach can make.