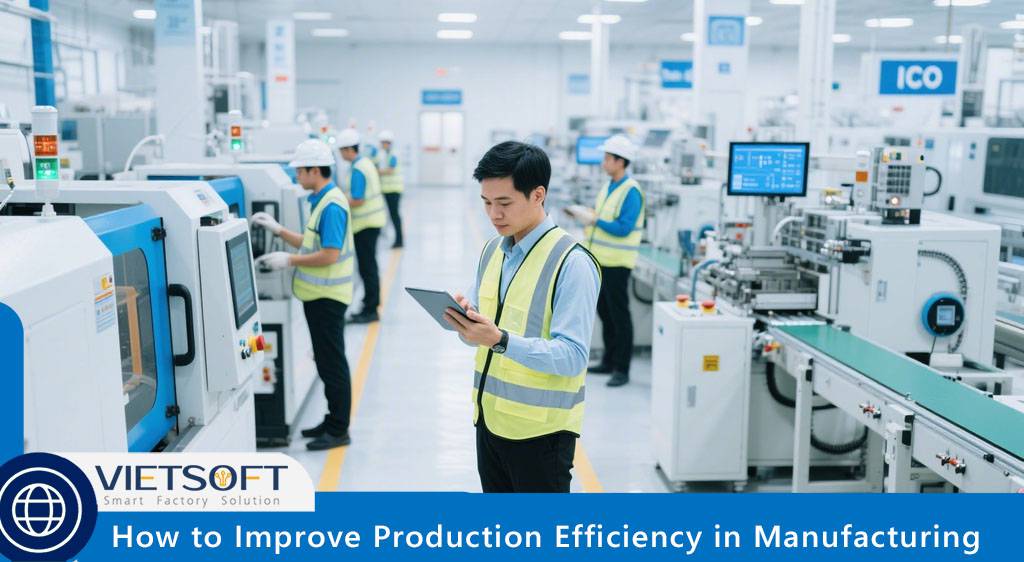
In the fast-paced world of manufacturing, achieving optimal production efficiency is a critical goal for staying competitive. Whether you’re managing a small factory or a large industrial plant, improving production efficiency can lead to reduced costs, higher output, better quality, and enhanced profitability. This comprehensive guide explores what production efficiency entails, why it matters, and actionable strategies to enhance it. We’ll also discuss how tools like CMMS EcoMaint from Vietsoft can revolutionize your maintenance processes to boost efficiency.
I. What Is Production Efficiency?
Production efficiency refers to the ability of a manufacturing operation to produce the maximum output of high-quality goods using the least amount of resources, such as labor, materials, energy, and time. It’s about optimizing every aspect of the production process to minimize waste while maximizing value.
II. Why Production Efficiency Matters
Achieving high production efficiency offers several benefits:
- Cost Reduction: Efficient processes reduce waste, lowering material and labor costs.
- Improved Quality: Streamlined operations lead to consistent product quality, reducing defects and rework.
- Increased Output: Optimized workflows allow for higher production volumes without additional investments.
- Enhanced Competitiveness: Efficient manufacturers can respond faster to market demands and offer competitive pricing.
- Sustainability: Reduced resource consumption aligns with environmental goals, minimizing waste and energy use.
- Worker Safety: Well-organized processes reduce risks, creating safer work environments.
In today’s global market, where consumer expectations are high and margins are tight, improving production efficiency is not just an option—it’s a necessity.
III. Key Metrics to Measure Production Efficiency
To improve production efficiency, you first need to measure it. Tracking key performance indicators (KPIs) provides a clear picture of your current performance and highlights areas for improvement. Below are the most critical KPIs for assessing production efficiency:
1. Overall Equipment Effectiveness (OEE)
OEE is a gold-standard metric that measures how effectively equipment is utilized during planned production time. It combines three factors:
- Availability: The percentage of time equipment is operational (e.g., Run Time ÷ Planned Production Time).
- Performance: The speed of production compared to the ideal rate (e.g., (Ideal Cycle Time × Total Count) ÷ Run Time).
- Quality: The proportion of defect-free products (e.g., Good Count ÷ Total Count).
Formula: OEE = Availability × Performance × Quality
Example: If a machine is available 90% of the time, runs at 80% of its ideal speed, and produces 95% defect-free products, its OEE is 0.90 × 0.80 × 0.95 = 68.4%. World-class OEE scores are typically 85% or higher.
2. Throughput
Throughput measures the average number of units produced per unit of time (e.g., units per hour). It helps identify bottlenecks and quantify the cost of downtime.
Example: If a production line generates $1 million worth of goods per hour, a 20-minute downtime event costs $333,333 in lost production.
3. Capacity Utilization
This KPI calculates the percentage of a facility’s maximum production capacity being used.
Formula: (Actual Output ÷ Maximum Possible Output) × 100
Example: If a plant produces 800 units daily but could produce 1,000 units at full capacity, its capacity utilization is (800 ÷ 1,000) × 100 = 80%. Aim for 85–90% to balance efficiency and flexibility.
4. Yield Rate
Yield rate measures the percentage of products meeting quality standards without requiring rework or scrapping.
Formula: (Good Units ÷ Total Units) × 100
Example: If 950 out of 1,000 units produced meet quality standards, the yield rate is (950 ÷ 1,000) × 100 = 95%.
5. Scrap Rate
Scrap rate tracks the percentage of materials wasted during production.
Formula: (Scrap Weight ÷ Total Material Weight) × 100
Example: If 50 kg of material is wasted out of 1,000 kg used, the scrap rate is (50 ÷ 1,000) × 100 = 5%.
By monitoring these KPIs, manufacturers can pinpoint inefficiencies and track progress toward improving production efficiency.
IV. 10 Proven Strategies to Improve Production Efficiency
Enhancing production efficiency requires a holistic approach that integrates process optimization, technology adoption, workforce development, and data-driven decision-making. Below are ten detailed strategies, grounded in lean manufacturing principles and modern maintenance practices, to help manufacturers improve production efficiency and achieve sustainable results.
1. Conduct a Comprehensive Production Audit
A thorough production audit is the foundation for identifying inefficiencies and opportunities to improve production efficiency. This process involves analyzing every aspect of your operations to uncover bottlenecks, waste, and underperforming areas.
- Steps to Conduct an Audit:
- Map the Production Process: Create a flowchart of all production stages, from raw material intake to finished goods.
- Collect Data: Gather data on cycle times, equipment downtime, defect rates, and resource consumption.
- Engage Stakeholders: Involve operators, maintenance teams, and managers to gain insights into daily challenges.
- Use Technology: Leverage tools like CMMS EcoMaint to track equipment performance and maintenance history.
- Key Focus Areas:
- Identify bottlenecks where work accumulates (e.g., slow machines or manual processes).
- Assess energy usage to find opportunities for conservation.
- Evaluate inventory levels to avoid overstocking or shortages.
2. Optimize Workspace and Workflow Design
The physical layout of your factory and the design of your workflows directly impact production efficiency. Poorly organized workspaces lead to wasted time, increased errors, and reduced productivity.
- Workspace Optimization Tips:
- Minimize Movement: Arrange workstations to reduce the distance materials and workers travel. For example, adopt a U-shaped cellular manufacturing layout to streamline material flow.
- Ergonomic Design: Ensure tools and supplies are within arm’s reach to reduce operator fatigue.
- Environmental Control: Maintain proper lighting (at least 500 lux for general tasks), ventilation, and temperature (ideally 20–24°C) to enhance equipment performance and worker comfort.
- Maintenance Access: Ensure sufficient space around equipment for maintenance tasks to prevent delays during repairs.
- Workflow Optimization Techniques:
- Value Stream Mapping: Visualize the entire production process to identify non-value-adding steps and streamline workflows.
- Cellular Manufacturing: Group machines and workers into cells based on production steps to reduce material transport time.
- Standardized Workstations: Equip each workstation with identical tools and setups to ensure consistency across shifts.
3. Embrace Automation and Technology
Modern technology, including automation and data-driven tools, is a game-changer for improving production efficiency. By reducing manual tasks and providing real-time insights, technology enhances precision and productivity.
- Technologies to Adopt:
- IoT Sensors: Monitor equipment parameters like vibration, temperature, or pressure to detect issues before they cause failures.
- Robotics: Automate repetitive tasks such as assembly, packaging, or material handling to reduce labor costs and errors.
- Data Analytics Platforms: Analyze production data to identify trends, inefficiencies, and optimization opportunities.
- CMMS EcoMaint: Centralize maintenance management, automate work orders, and provide mobile access to SOPs and equipment history.
- Implementation Tips:
- Start with small-scale automation for high-impact areas, such as automating quality inspections.
- Integrate IoT with CMMS EcoMaint to enable predictive maintenance and real-time performance tracking.
- Train employees to use new technologies effectively to maximize ROI.
4. Shift to Proactive Maintenance
Reactive maintenance—fixing equipment only after it fails—is costly and disruptive. A proactive maintenance strategy, combining preventive and predictive approaches, is essential to improve production efficiency.
- Preventive Maintenance:
- Schedule regular inspections, lubrication, and part replacements based on manufacturer recommendations or usage patterns.
- Use CMMS EcoMaint to automate maintenance schedules and ensure timely task completion.
- Predictive Maintenance:
- Deploy IoT sensors to monitor equipment health in real-time (e.g., detecting abnormal vibrations in a motor).
- Use data analytics to predict failures and schedule repairs during planned downtime.
- Benefits:
- Reduces unplanned downtime by up to 50%.
- Extends equipment lifespan by 20–30%.
- Improves production consistency and quality.
5. Identify and Eliminate Bottlenecks
Bottlenecks are choke points in the production process that limit overall output, regardless of other improvements. Addressing them is critical to improve production efficiency.
- How to Identify Bottlenecks:
- Map the production process to visualize workflow.
- Measure cycle times at each stage to pinpoint delays.
- Monitor work-in-progress (WIP) inventory for accumulation points.
- Analyze downtime data using CMMS EcoMaint to identify problematic equipment.
- Solutions:
- Add capacity (e.g., additional machines or staff) at bottleneck points.
- Redesign processes to balance workload across stages.
- Use automation to speed up slow processes.
6. Reduce Waste with Lean Manufacturing
Lean manufacturing principles focus on eliminating waste to maximize value. The DOWNTIME acronym highlights eight types of waste: Defects, Overproduction, Waiting, Non-utilized talent, Transportation, Inventory, Motion, and Excess processing.
- Lean Strategies:
- 5S Methodology: Sort (remove unnecessary items), Set in order (organize tools), Shine (keep the workplace clean), Standardize (create consistent processes), and Sustain (maintain discipline).
- Just-in-Time (JIT): Produce only what is needed, when it’s needed, to reduce inventory costs.
- Kaizen: Encourage continuous, incremental improvements through employee involvement.
- Value Stream Mapping: Identify and eliminate non-value-adding activities in the production process.
- Implementation Tips:
- Conduct 5S workshops to train employees on workplace organization.
- Use CMMS EcoMaint to track waste metrics, such as scrap rates and downtime causes.
- Involve operators in Kaizen events to generate improvement ideas.
7. Optimize Supply Chain Management
Supply chain inefficiencies, such as material shortages or delayed deliveries, can halt production and increase costs. Optimizing the supply chain is crucial to improve production efficiency.
- Key Actions:
- Build Strong Supplier Relationships: Establish clear communication channels and performance metrics for suppliers.
- Demand Forecasting: Use historical data and market trends to predict material needs accurately.
- Vendor-Managed Inventory (VMI): Allow suppliers to monitor and replenish inventory, reducing stockouts and overstocking.
- Use CMMS EcoMaint: Track spare parts inventory and integrate with purchasing systems to avoid delays.
8. Standardize Processes and Procedures
Standardized processes ensure consistency, reduce errors, and simplify training, all of which contribute to improving production efficiency.
- Key Actions:
- Document best practices in clear, visual Standard Operating Procedures (SOPs).
- Implement Poka-Yoke (error-proofing) techniques, such as color-coded tools or automated checks, to prevent mistakes.
- Conduct regular audits to ensure compliance with SOPs.
- Use CMMS EcoMaint to create digital SOP libraries accessible via mobile devices.
- Benefits:
- Reduces defect rates by ensuring consistent quality.
- Shortens training time for new employees.
- Enables faster problem identification and resolution.
9. Invest in Employee Training and Engagement
A skilled and motivated workforce is a cornerstone of production efficiency. Untrained or disengaged employees lead to errors, slower work, and increased downtime.
- Training Strategies:
- Structured Onboarding: Provide comprehensive training for new hires to ensure baseline knowledge.
- Cross-Training: Train employees to perform multiple roles, increasing flexibility during staffing shortages or bottlenecks.
- Continuous Learning: Offer regular training on new technologies, safety protocols, and lean principles.
- Engagement Programs: Recognize employee contributions and encourage feedback to foster a culture of continuous improvement.
- Implementation Tips:
- Use CMMS EcoMaint to track training completion and skill matrices.
- Conduct hands-on workshops to reinforce practical skills.
- Create incentive programs to reward efficiency improvements.
10. Leverage Data for Continuous Improvement
Data-driven decision-making is essential for sustaining efficiency gains. Real-time data helps identify trends, set improvement targets, and measure progress.
- Key Actions:
- Install real-time production monitoring systems to track KPIs like OEE, throughput, and yield rate.
- Create visual dashboards to display performance metrics for all teams.
- Hold weekly review meetings to discuss KPIs and assign action items.
- Use CMMS EcoMaint to analyze maintenance and production data, identifying recurring issues and optimization opportunities.
- Benefits:
- Enables proactive problem-solving before issues escalate.
- Provides accountability through measurable targets.
- Supports continuous improvement cycles.
V. The Role of CMMS EcoMaint in Improving Production Efficiency
To achieve and sustain high production efficiency, manufacturers need robust tools to manage maintenance and optimize operations. CMMS EcoMaint, developed by Vietsoft, is a powerful computerized maintenance management system designed to streamline maintenance processes and boost productivity.
Why Choose CMMS EcoMaint?
- Automated Maintenance Scheduling: Ensure preventive maintenance tasks are performed on time to minimize downtime.
- Real-Time Asset Tracking: Monitor equipment performance and predict failures using IoT integration.
- Digital SOP Libraries: Provide technicians with instant access to procedures and checklists via mobile devices.
- Inventory Management: Optimize spare parts inventory to avoid delays during repairs.
- Analytics Dashboards: Gain insights into maintenance and production performance to drive continuous improvement.
Real-World Impact
A Vietnamese manufacturing plant implemented CMMS EcoMaint and saw a 35% reduction in unplanned downtime within six months. By automating maintenance schedules and optimizing spare parts inventory, the plant increased its OEE from 65% to 80%, significantly improving production efficiency.
Discover the CMMS EcoMaint solution here.
Contact us for consultation via hotline: 0986778578 or email: sales@vietsoft.com.vn.
VI. FAQs on Improving Production Efficiency
1. What are the key steps to improve production efficiency?
To improve production efficiency, conduct a production audit, optimize workflows, invest in technology, implement proactive maintenance, eliminate bottlenecks, reduce waste, optimize the supply chain, standardize processes, train employees, and leverage data for continuous improvement.
2. How can I measure production efficiency?
Use KPIs like Overall Equipment Effectiveness (OEE), throughput, capacity utilization, yield rate, and scrap rate. For example, OEE is calculated as Availability × Performance × Quality, with world-class scores at 85% or higher.
3. What tools can help improve production efficiency?
Tools like CMMS EcoMaint, IoT sensors, automation systems, and data analytics platforms are essential for streamlining maintenance, monitoring performance, and optimizing processes.
4. How does proactive maintenance impact production efficiency?
Proactive maintenance, including preventive and predictive strategies, reduces unplanned downtime, extends equipment life, and ensures consistent production, directly improving production efficiency.
VII. Conclusion: A Path to Sustainable Efficiency
Improving production efficiency is a continuous journey that requires a strategic blend of process optimization, technology adoption, and workforce empowerment. By implementing the ten strategies outlined above and leveraging tools like CMMS EcoMaint, manufacturers can achieve significant gains in productivity, quality, and profitability.
Start by auditing your current processes, addressing bottlenecks, and investing in proactive maintenance. With the right approach and tools, you can transform your manufacturing operation into a model of efficiency, ready to meet the demands of today’s competitive market.