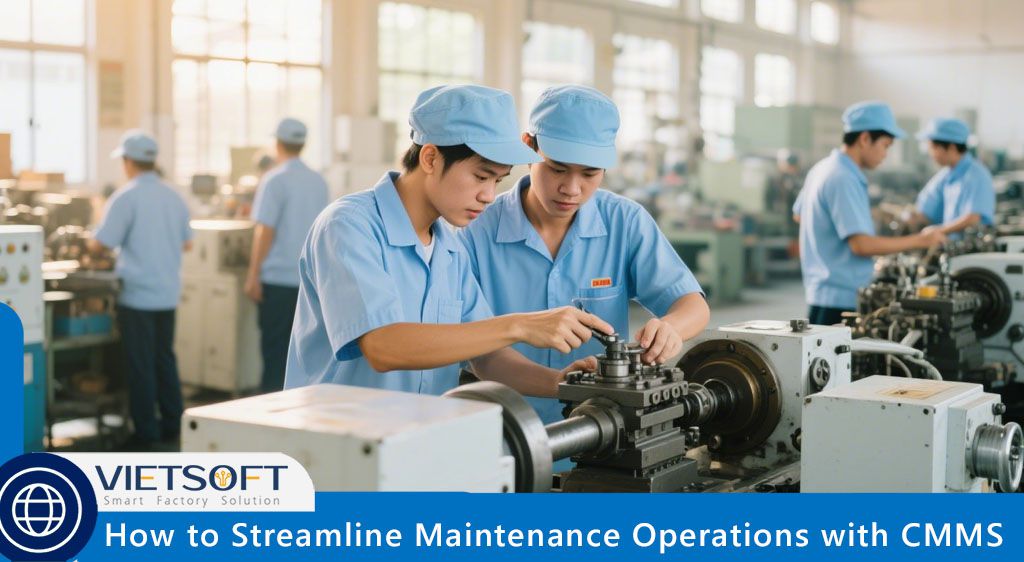
In today’s fast-paced industrial environment, optimizing maintenance operations is critical for ensuring equipment reliability, minimizing downtime, and boosting overall productivity. A Computerized Maintenance Management System (CMMS) is a powerful tool that helps organizations streamline maintenance operations by centralizing processes, automating tasks, and providing actionable insights. This comprehensive guide will explore how to streamline maintenance operations using CMMS, offering practical strategies, data-backed benefits, and actionable steps to transform your maintenance workflows.
I. What Is a CMMS and Why Does It Matter?
A Computerized Maintenance Management System (CMMS) is a software platform designed to simplify and optimize maintenance operations. It serves as a centralized hub for managing work orders, tracking asset performance, scheduling preventive maintenance, monitoring inventory, and ensuring compliance with regulatory standards. By replacing outdated manual processes like spreadsheets or paper logs, a CMMS provides real-time visibility into maintenance activities, enabling data-driven decision-making.
Key Features of a CMMS
A robust CMMS, such as CMMS EcoMaint by Vietsoft, offers the following features to streamline maintenance operations:
- Work Order Management: Assign, track, and complete tasks with full visibility into progress and status.
- Asset Management: Maintain detailed records of equipment history, including maintenance schedules, repairs, and warranties.
- Preventive Maintenance Scheduling: Automate recurring tasks to prevent equipment failures.
- Inventory Management: Track spare parts, automate reordering, and optimize stock levels.
- Compliance and Reporting: Generate audit-ready reports for regulatory compliance and internal reviews.
- Mobile Access: Empower technicians with real-time data access via mobile devices, even in offline environments.
II. Why Streamline Maintenance Operations?
Streamlining maintenance operations involves optimizing workflows to reduce inefficiencies, minimize downtime, and lower costs. According to McKinsey, companies adopting streamlined maintenance strategies can reduce maintenance costs by 18-25% and cut unexpected equipment failures by up to 50%. These improvements translate into longer asset lifespans, improved operational efficiency, and significant cost savings.
By implementing a CMMS, businesses can shift from reactive maintenance (fixing equipment after it fails) to proactive strategies like preventive and predictive maintenance, ensuring smoother operations and better resource allocation.
III. Key Strategies to Streamline Maintenance Operations with CMMS
To achieve operational excellence, organizations must adopt a structured approach to streamline maintenance operations. Below are five key strategies, enhanced with insights from industry expertise and practical applications of CMMS technology.
1. Centralize Maintenance Processes with CMMS
Centralizing maintenance activities is the foundation of streamlining operations. A CMMS acts as a single source of truth, consolidating all maintenance-related data into one platform. This eliminates the chaos of scattered records, manual logs, and miscommunication among teams.
How CMMS Centralizes Operations
- Unified Data Repository: Store all asset details, work orders, and maintenance histories in one place, accessible to all team members.
- Automated Workflows: Automate task assignments, reminders, and notifications to ensure timely execution of maintenance activities.
- Real-Time Updates: Provide instant updates on task progress, reducing delays caused by miscommunication.
For example, Vietsoft’s CMMS EcoMaint allows maintenance teams to access asset histories, manuals, and safety checklists from a single dashboard, ensuring technicians have the information they need to act quickly and efficiently.
2. Automate Preventive Maintenance Scheduling
Preventive maintenance (PM) involves performing regular maintenance tasks to prevent equipment failures before they occur. A CMMS automates PM scheduling, ensuring tasks are performed consistently and on time, without disrupting production.
Benefits of Automated PM
- Reduced Downtime: Scheduling maintenance during low-production periods minimizes operational disruptions.
- Extended Asset Life: Regular maintenance prevents wear and tear, extending equipment lifespan.
- Cost Savings: Preventive maintenance reduces the need for costly emergency repairs.
A CMMS like CMMS EcoMaint allows users to set up recurring PM tasks based on time intervals, usage metrics, or manufacturer recommendations.
3. Leverage Predictive Maintenance with Data Analytics
Predictive maintenance (PdM) takes preventive maintenance a step further by using data analytics and IoT sensors to predict equipment failures before they occur. By integrating IoT devices with a CMMS, organizations can monitor real-time equipment conditions and act proactively.
How Predictive Maintenance Works
- IoT Integration: Sensors collect data on temperature, vibration, and other performance metrics.
- Data Analytics: A CMMS analyzes this data to identify patterns or anomalies that indicate potential issues.
- Prescriptive Actions: The system provides recommendations for maintenance tasks, such as replacing a worn component before it fails.
Deloitte’s research highlights that predictive maintenance can boost equipment uptime by 10-20% and reduce maintenance costs by up to 25%. By anticipating failures, companies avoid costly downtime and optimize resource allocation.
4. Optimize Spare Parts Management
Effective spare parts management is critical to streamlining maintenance operations. A CMMS tracks inventory levels, automates reordering, and ensures critical parts are available when needed, reducing delays and costs.
Strategies for Spare Parts Optimization
- Inventory Tracking: Monitor stock levels across multiple locations and set low-stock alerts.
- Usage Analytics: Analyze consumption patterns to predict future needs and avoid overstocking.
- Just-in-Time Inventory: Order parts only when needed to minimize storage costs.
For example, CMMS EcoMaint ’s inventory module allows users to scan barcodes or QR codes to track parts usage, ensuring accurate inventory records. This reduces emergency orders and prevents stockouts, keeping maintenance on schedule.
5. Empower Your Workforce with Training and Mobile Access
A skilled and empowered workforce is essential for efficient maintenance operations. A CMMS enhances workforce productivity by providing mobile access to critical information and supporting continuous training.
Mobile Access Benefits
- Real-Time Data: Technicians can view work orders, asset histories, and manuals on mobile devices, even offline.
- Faster Response Times: Mobile access enables technicians to close work orders in the field, reducing delays.
- Improved Collaboration: Teams can share updates and troubleshoot issues in real time.
Training for Success
Regular training ensures technicians are proficient in using CMMS tools and performing maintenance tasks. Training should cover:
- Operating and maintaining specific equipment.
- Using CMMS software to manage work orders and inventory.
- Recognizing early signs of equipment issues through data analysis.
CMMS EcoMaint ’s mobile-friendly interface allows technicians to access work orders and update task statuses on the go, boosting productivity and reducing administrative overhead.
IV. Measurable Benefits of Streamlining Maintenance with CMMS
Implementing a CMMS to streamline maintenance operations delivers tangible benefits that impact both operational efficiency and the bottom line. Below are key metrics supported by industry research:
- Reduced Downtime: organizations using CMMS experience 17% less downtime compared to industry averages.
- Cost Savings: predictive maintenance strategies enabled by CMMS can reduce maintenance costs by 18-25%.
- Improved Productivity: 20% improvement in operational efficiency for companies optimizing maintenance resources.
- Enhanced Asset Productivity: maintenance optimization can increase asset productivity by 25-30%.
- Higher Employee Satisfaction: structured maintenance programs improve employee satisfaction by 28%, boosting retention and morale.
These benefits demonstrate the transformative impact of a CMMS on maintenance operations, making it a strategic investment for any industrial organization.
V. Why Choose CMMS EcoMaint by Vietsoft for Streamlined Maintenance?
When it comes to streamlining maintenance operations, selecting the right CMMS is critical. CMMS EcoMaint , developed by Vietsoft, is a user-friendly, customizable, and scalable solution designed to meet the needs of industries ranging from manufacturing to logistics. With over a decade of experience serving the Vietnamese market, Vietsoft has crafted CMMS EcoMaint to address real-world maintenance challenges with precision and flexibility.
Key Features of CMMS EcoMaint
- Fast Implementation: Get up and running in days, not months, with minimal disruption.
- Customizable Workflows: Tailor dashboards, reports, and processes to match your organization’s needs.
- Mobile Accessibility: Access all features on smartphones and tablets, with offline capabilities for remote sites.
- Seamless Integration: Connect with ERP systems, IoT devices, and other business tools for streamlined data flow.
- Dedicated Support: Vietsoft’s Vietnam-based support team provides expert guidance tailored to local industries.
Learn more about CMMS EcoMaint here. Or contact us via hotline: 0986778578 or email: sales@vietsoft.com.vn.
VI. Best Practices for Implementing a CMMS
To maximize the benefits of a CMMS and streamline maintenance operations, follow these best practices:
· Assess Current Processes: Conduct a thorough audit of existing maintenance workflows to identify inefficiencies and set clear goals.
· Choose the Right CMMS: Select a system like CMMS EcoMaint that aligns with your industry needs, budget, and scalability requirements.
· Train Your Team: Provide comprehensive training to ensure all team members can use the CMMS effectively.
· Monitor Key Performance Indicators (KPIs): Track metrics like Mean Time to Repair (MTTR), downtime, and PM completion rates to measure success.
· Continuously Improve: Regularly review CMMS data and adjust maintenance strategies to stay aligned with business goals.
VII. Conclusion
Streamlining maintenance operations with a CMMS is a game-changer for industrial organizations aiming to reduce downtime, cut costs, and improve efficiency. By centralizing processes, automating preventive maintenance, leveraging predictive analytics, optimizing spare parts, and empowering your workforce, a CMMS like CMMS EcoMaint by Vietsoft can transform your maintenance strategy.
The data speaks for itself: organizations using CMMS solutions see up to 50% fewer equipment failures, 25% lower maintenance costs, and 20% higher operational efficiency. Whether you’re managing a single facility or a multi-site operation, now is the time to rethink your maintenance approach.
VIII. FAQs
1. What is the purpose of a CMMS in maintenance operations?
A CMMS organizes and automates maintenance tasks, including work orders, asset tracking, and inventory management, to reduce downtime and improve efficiency.
2. How does a CMMS help streamline maintenance operations?
By automating scheduling, centralizing data, and enabling predictive maintenance, a CMMS reduces manual work, prevents equipment failures, and optimizes resources.
3. Why is CMMS EcoMaint a good choice for maintenance management?
CMMS EcoMaint offers a user-friendly interface, mobile access, and customizable workflows tailored to industries in Vietnam, backed by Vietsoft’s expert support.
4. How can predictive maintenance improve operations?
Predictive maintenance uses data analytics to anticipate equipment failures, reducing downtime by 10-20% and maintenance costs by up to 25%.