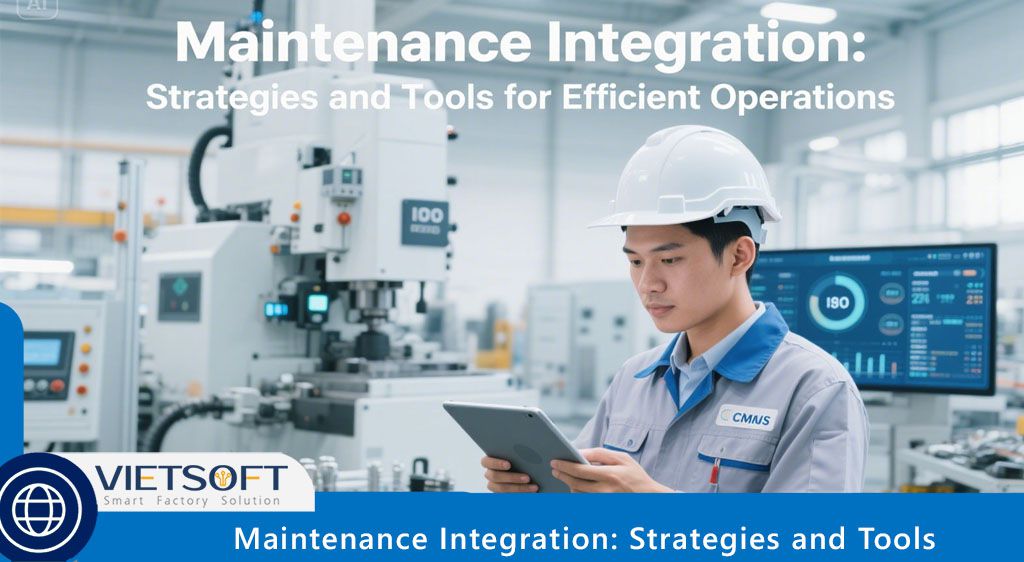
In today’s fast-evolving industrial landscape, ensuring seamless operations is critical for businesses aiming to maintain competitiveness and operational efficiency. Maintenance integration has emerged as a pivotal approach, enabling organizations to streamline processes, reduce downtime, and optimize asset performance. By aligning maintenance systems with broader business operations, companies can achieve a cohesive, data-driven ecosystem that enhances productivity and reliability.
This article explores the concept of maintenance integration, its importance, key strategies, tools, and real-world applications.
I. What is Maintenance Integration?
Maintenance integration refers to the process of connecting maintenance management systems, tools, and processes with other business functions to create a unified operational framework. This approach ensures that data flows seamlessly across platforms, enabling real-time decision-making and coordinated workflows. By integrating maintenance activities with inventory, production, and business intelligence systems, organizations can eliminate silos, reduce inefficiencies, and enhance overall performance.
For example, a manufacturing plant might integrate its maintenance system with inventory management to automatically reorder spare parts when stocks run low, ensuring repairs are completed without delays. This interconnected approach not only streamlines operations but also aligns maintenance with organizational goals, such as cost reduction and improved equipment reliability.
II. Why Maintenance Integration Matters
Effective maintenance integration is essential for modern businesses, particularly in asset-intensive industries like manufacturing, healthcare, and energy. Without integration, maintenance processes often operate in isolation, leading to data fragmentation, delayed responses, and increased costs. Here’s why maintenance integration is critical:
- Improved Efficiency: Integrated systems reduce manual processes, enabling faster task execution and better resource allocation.
- Cost Reduction: By anticipating issues and optimizing maintenance schedules, businesses can avoid costly emergency repairs and downtime.
- Enhanced Asset Reliability: Integration allows for proactive maintenance, extending equipment lifespan and improving performance.
- Data-Driven Decisions: Centralized data provides actionable insights, enabling managers to make informed decisions.
- Regulatory Compliance: Integrated systems maintain detailed records, simplifying audits and ensuring compliance with industry standards.
For instance, a hospital integrating its maintenance system with a CMMS like CMMS EcoMaint can ensure critical equipment, such as MRI machines, is serviced on time, minimizing disruptions to patient care. This level of coordination is only possible through robust maintenance integration strategies.
III. Key Strategies for Effective Maintenance Integration
To achieve seamless maintenance integration, organizations must adopt a strategic approach that aligns systems, processes, and people. Below are eight proven strategies to implement, each designed to enhance operational efficiency and reliability.
1. Centralize Data Management for Unified Insights
Centralizing maintenance data creates a single source of truth, enabling teams to access real-time information on equipment performance, repair histories, and maintenance schedules. A centralized system eliminates the challenges of fragmented data across multiple platforms, reducing miscommunication and duplicate efforts.
For example, a factory with multiple production lines can use a centralized platform to track equipment performance across all sites. This visibility allows maintenance managers to identify patterns, such as recurring issues with a specific machine, and address them proactively. Tools like CMMS EcoMaint provide centralized dashboards that consolidate data, making it easier to monitor and manage maintenance activities.
2. Integrate Maintenance with Inventory Systems
Effective inventory management is crucial for maintenance operations. By integrating maintenance systems with inventory platforms, organizations can track spare parts in real time, automate reordering, and prevent delays due to stock shortages. This integration ensures that technicians have the right components available when needed, minimizing downtime.
Consider a logistics company managing a fleet of vehicles. By linking its maintenance system to inventory management, the company can automatically reorder critical parts, such as brake pads, when stocks fall below a set threshold. This proactive approach reduces repair times and keeps vehicles operational.
3. Leverage Predictive Maintenance for Proactive Solutions
Predictive maintenance uses data analytics, machine learning, and IoT sensors to predict equipment failures before they occur. By integrating these technologies with maintenance systems, businesses can schedule maintenance at optimal times, reducing unexpected downtime.
For example, a power plant can use vibration sensors integrated with a CMMS to monitor turbine performance. If the sensors detect abnormal vibrations, the system triggers a work order for inspection, preventing a costly breakdown. Predictive maintenance relies on seamless maintenance integration to ensure data from sensors flows into the maintenance platform for analysis and action.
4. Automate Workflow Management for Efficiency
Automation is a cornerstone of modern maintenance integration. By automating work orders, scheduling, and reporting, businesses can reduce manual errors and streamline operations. Automated workflows prioritize tasks, assign responsibilities, and track progress without requiring constant oversight.
For instance, a manufacturing facility can use automation to assign urgent repair tasks to available technicians based on their skills and location. This reduces response times and ensures critical issues are addressed promptly. Tools like CMMS EcoMaint offer customizable automation features, allowing businesses to tailor workflows to their specific needs.
5. Connect Maintenance with Business Operations
Maintenance is not an isolated function; it impacts production, supply chain, and overall business performance. Integrating maintenance systems with business operations, such as production scheduling or procurement, ensures alignment across departments.
For example, integrating maintenance with production scheduling allows managers to plan repairs during low-demand periods, minimizing disruptions. This level of coordination requires robust maintenance integration to ensure data flows between systems in real time.
6. Implement Mobile Maintenance Solutions
Mobile technologies have transformed maintenance operations by enabling technicians to access critical information on the go. By integrating mobile apps with maintenance systems, technicians can view work orders, update statuses, and access equipment manuals from their smartphones or tablets.
In a hotel, for instance, maintenance staff can use a mobile app to receive real-time alerts about a faulty HVAC system, access troubleshooting guides, and update repair progress. This integration enhances responsiveness and reduces paperwork, improving overall efficiency.
7. Harness Cloud Computing for Scalability
Cloud-based maintenance platforms offer flexibility, scalability, and remote access, making them ideal for maintenance integration. These systems enable real-time data updates, collaboration across locations, and secure storage without the need for extensive on-site infrastructure.
For example, a multi-site manufacturing company can use a cloud-based CMMS to manage maintenance across all facilities, ensuring consistent data access and updates. Cloud solutions also simplify scaling operations as businesses grow, adding new users or tools without significant investment.
8. Prioritize Employee Training and Collaboration
Technology alone is not enough; successful maintenance integration requires a skilled and engaged workforce. Regular training ensures employees understand how to use integrated systems effectively, while open communication fosters collaboration between maintenance and other departments.
For instance, training technicians on a CMMS like CMMS EcoMaint equips them to log issues, track repairs, and interpret predictive maintenance data. Encouraging cross-departmental communication ensures maintenance aligns with production and inventory goals, creating a cohesive operational strategy.
IV. Tools Driving Maintenance Integration
Several tools are essential for achieving effective maintenance integration. These tools, when connected through APIs or other integration methods, create a seamless ecosystem that enhances maintenance efficiency. Below are the key tools and their roles in integration.
1. Computerized Maintenance Management Systems (CMMS)
A CMMS is the backbone of maintenance integration, providing a centralized platform to manage work orders, assets, and maintenance schedules. For example, CMMS EcoMaint from Vietsoft automates work order creation, tracks equipment history, and integrates with inventory and production systems. In a hospital, CMMS EcoMaint can schedule preventive maintenance for critical equipment, ensuring compliance with healthcare regulations.
2. Enterprise Resource Planning (ERP) Systems
ERP systems integrate maintenance with broader business functions, such as finance, procurement, and production. For example, when a maintenance team logs a repair request, the ERP system can automatically generate a purchase order for spare parts, aligning maintenance with budgeting and inventory processes.
3. Condition Monitoring Tools
Condition monitoring tools, such as vibration sensors and thermal imaging devices, provide real-time data on equipment health. When integrated with a CMMS, these tools trigger maintenance actions based on detected anomalies. For instance, a manufacturing plant can use sensors to monitor conveyor belt performance, feeding data into the CMMS for predictive maintenance scheduling.
4. Mobile Maintenance Apps
Mobile apps enable technicians to access maintenance data in the field, improving responsiveness and documentation. By integrating these apps with a CMMS, technicians can update work orders in real time, reducing delays and improving accuracy.
5. Business Intelligence (BI) Tools
BI tools analyze maintenance data to identify trends and optimize strategies. By integrating BI with maintenance systems, managers can generate reports on equipment performance, downtime, and costs, enabling data-driven decisions. For example, a logistics company can use BI to assess the cost-effectiveness of replacing versus repairing aging vehicles.
V. Benefits of Maintenance Integration
Implementing maintenance integration delivers a range of benefits that enhance operational efficiency and competitiveness. These include:
- Reduced Downtime: Proactive maintenance minimizes unexpected equipment failures, keeping operations running smoothly.
- Cost Savings: Optimized maintenance schedules and inventory management reduce repair and replacement costs.
- Extended Asset Lifespan: Regular, data-driven maintenance extends the useful life of equipment, maximizing ROI.
- Improved Safety: Well-maintained equipment reduces the risk of accidents, ensuring a safer workplace.
- Enhanced Compliance: Integrated systems maintain detailed records, simplifying regulatory audits.
- Better Workforce Productivity: Automation and mobile tools free up technicians to focus on high-value tasks, improving job satisfaction.
VI. Trends Shaping Maintenance Integration in 2025
As industries evolve, several trends are driving the future of maintenance integration:
- AI and Machine Learning: Advanced algorithms are improving predictive maintenance accuracy, enabling earlier detection of potential issues.
- Digital Twins: Virtual replicas of assets allow for simulation-based maintenance planning, reducing risks and costs.
- Sustainability: Maintenance integration is increasingly focused on optimizing energy use and reducing waste, aligning with environmental goals.
- Augmented Reality (AR): AR tools guide technicians through complex repairs, improving efficiency and reducing errors.
VII. How CMMS EcoMaint Enhances Maintenance Integration
For businesses in Vietnam seeking a robust solution for maintenance integration, CMMS EcoMaint from Vietsoft offers a powerful platform to streamline operations. This cloud-based system integrates seamlessly with inventory, production, and BI tools, providing a centralized hub for managing maintenance tasks. Key features include:
- Automated Work Orders: Streamline task assignment and tracking.
- Real-Time Analytics: Gain insights into equipment performance and maintenance trends.
- Mobile Access: Empower technicians with on-the-go access to work orders and manuals.
- Predictive Maintenance: Leverage IoT and analytics to anticipate equipment issues.
By adopting CMMS EcoMaint, businesses can achieve seamless maintenance integration, reducing downtime, optimizing costs, and ensuring compliance. To learn more about how CMMS EcoMaint can transform your maintenance operations, Discover CMMS EcoMaint here.
Contact us via hotline: 0986778578 or email: sales@vietsoft.com.vn.
VIII. Conclusion
Maintenance integration is a game-changer for businesses aiming to optimize operations, reduce costs, and enhance asset reliability. By adopting strategies like centralized data management, predictive maintenance, and automation, and leveraging tools like CMMS, ERP, and IoT sensors, organizations can create a cohesive maintenance ecosystem. Solutions like CMMS EcoMaint from Vietsoft are paving the way for smarter, more efficient maintenance in Vietnam and beyond, helping businesses stay competitive in a rapidly changing industrial landscape.
By embracing maintenance integration, companies can transform maintenance from a reactive task into a strategic asset, driving productivity, safety, and profitability. Start your journey today by exploring how integrated tools can elevate your maintenance operations to new heights.