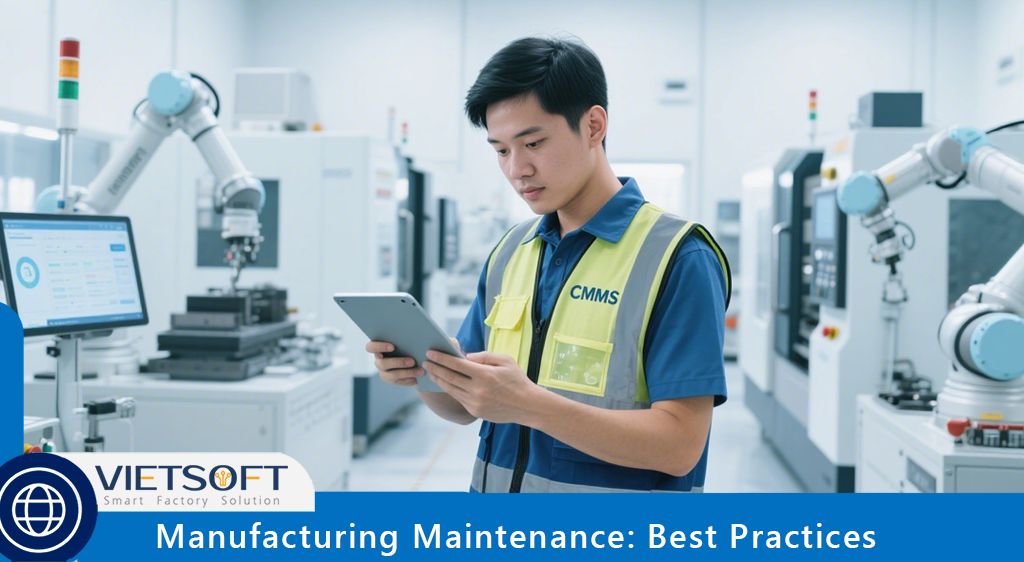
In the fast-paced world of manufacturing, ensuring equipment reliability and operational efficiency is critical to maintaining competitive advantage. Manufacturing maintenance, a cornerstone of industrial success, involves a strategic blend of processes, technologies, and best practices designed to keep machinery and systems running at peak performance. This article explores the essence of manufacturing maintenance, its key strategies, modern technologies, and actionable best practices to optimize operations, reduce downtime, and enhance productivity.
I. What is Manufacturing Maintenance?
Manufacturing maintenance refers to the systematic approach of maintaining, repairing, and optimizing machinery, equipment, and infrastructure to ensure uninterrupted production. It encompasses a range of activities, from routine inspections and preventive measures to predictive analytics and corrective repairs. The goal is to minimize downtime, extend equipment lifespan, and maintain high safety and efficiency standards.
In manufacturing, where complex machinery operates under continuous stress, maintenance is not just about fixing breakdowns—it’s about proactively managing assets to prevent failures. For instance, regular lubrication, calibration, and condition monitoring can prevent costly disruptions and maintain production quality. By integrating advanced tools like Computerized Maintenance Management Systems (CMMS), manufacturers can streamline these processes, making maintenance a strategic driver of operational excellence.
II. Why Manufacturing Maintenance Matters
Effective manufacturing maintenance is vital for several reasons:
- Minimized Downtime: Unplanned downtime can cost manufacturers significant revenue. A 2023 survey by ABB estimated that an hour of unscheduled downtime costs an average of $125,000. Regular maintenance reduces these risks.
- Enhanced Equipment Efficiency: Well-maintained machines operate at optimal performance, reducing energy waste and improving output quality.
- Extended Asset Lifespan: Proactive maintenance prevents premature wear, delaying the need for costly replacements.
- Improved Safety: Regular inspections and repairs ensure equipment operates safely, reducing workplace accidents.
- Cost Savings: By addressing issues early, manufacturers avoid expensive emergency repairs and rushed part orders.
III. Key Objectives of Manufacturing Maintenance
The primary objectives of manufacturing maintenance align with operational and financial goals:
1. Prevent Unplanned Downtime: Routine maintenance catches minor issues before they escalate into major failures.
2. Optimize Production Capacity: Properly maintained equipment ensures consistent output, avoiding bottlenecks and inefficiencies.
3. Ensure Workplace Safety: Functional safety mechanisms, like emergency stops and sensors, protect workers and comply with regulations like OSHA.
4. Reduce Operational Costs: Efficient maintenance minimizes energy waste, repair costs, and inventory overstocking.
5. Maintain Quality Standards: Calibration and upkeep ensure machines meet precise manufacturing tolerances, reducing defects.
IV. Types of Manufacturing Maintenance Strategies
Manufacturing maintenance strategies vary based on equipment needs, budget, and operational goals. Below, we explore the main types, their pros and cons, and when to use them.
1. Preventive Maintenance
What It Is: Preventive maintenance involves scheduled tasks, such as lubrication, cleaning, and part replacements, performed at regular intervals (e.g., every 90 days or after 10,000 operating hours) to prevent failures.
Pros:
- Reduces unexpected breakdowns.
- Extends equipment lifespan.
- Improves reliability and production consistency.
Cons:
- May lead to over-maintenance, increasing costs.
- Requires significant planning and resources.
When to Use: Ideal for critical equipment, like CNC machines or assembly lines, where downtime would cause significant disruptions.
2. Predictive Maintenance
System: Predictive Maintenance
What It Is: Predictive maintenance uses real-time data from IoT sensors, AI, and analytics to predict equipment failures before they occur. It monitors indicators like vibration, temperature, or pressure to schedule timely interventions.
Pros:
- Minimizes unnecessary maintenance.
- Reduces downtime by addressing issues proactively.
- Enhances efficiency with data-driven decisions.
Cons:
- High initial costs for sensors and software.
- Requires skilled personnel for data analysis.
When to Use: Best for high-value assets where downtime is costly, and technology infrastructure is available.
3. Corrective Maintenance
What It Is: Corrective maintenance addresses equipment failures after they occur, either immediately (unscheduled) or at a planned time (deferred).
Pros:
- Low upfront costs for non-critical assets.
- Simple to implement for easily replaceable parts.
Cons:
- Can lead to costly downtime.
- Not ideal for critical equipment.
When to Use: Suitable for non-critical, low-cost assets like filters or small tools.
4. Condition-Based Maintenance
What It Is: Condition-based maintenance monitors equipment conditions (e.g., wear, temperature) and performs maintenance only when needed, based on real-time data.
Pros:
- Avoids unnecessary maintenance.
- Optimizes resource use.
Cons:
- Requires investment in monitoring systems.
- Data management can be complex.
When to Use: Effective for equipment with variable operating conditions, such as motors or pumps.
5. Total Productive Maintenance (TPM)
What It Is: TPM involves all employees in daily maintenance tasks, combining preventive, predictive, and corrective strategies to foster a culture of continuous improvement.
Pros:
- Enhances accountability across teams.
- Reduces downtime through early detection.
Cons:
- Requires extensive training and commitment.
- Time-intensive to implement.
When to Use: Ideal for organizations prioritizing high standards and employee involvement.
6. Run-to-Failure Maintenance
What It Is: Run-to-failure allows equipment to operate until it breaks down, with repairs or replacements performed afterward.
Pros:
- Minimal planning required.
- Cost-effective for non-critical assets.
Cons:
- Risks unplanned downtime.
- Can lead to safety hazards.
When to Use: Suitable for inexpensive, easily replaceable parts that don’t impact operations.
V. Challenges in Manufacturing Maintenance
Despite its importance, manufacturing maintenance faces several challenges:
- Skilled Labor Shortages: A 2024 UpKeep survey noted that 72% of manufacturers face labor shortages, making it difficult to maintain complex equipment.
- Supply Chain Issues: A Limble study found that 34.1% of maintenance professionals struggle with spare parts availability, causing delays and increased costs.
- Budget Constraints: Limited budgets often force reactive maintenance, leading to long-term inefficiencies.
- Technological Complexity: Rapid advancements in IoT and AI require continuous training to keep up with modern systems.
- Regulatory Compliance: Strict standards, such as OSHA and ISO, demand rigorous documentation and safety protocols.
VI. Best Practices for Effective Manufacturing Maintenance
To overcome these challenges and optimize manufacturing maintenance, consider the following best practices:
1. Implement a Robust CMMS
A Computerized Maintenance Management System (CMMS) like Vietsoft’s CMMS EcoMaint streamlines maintenance operations by centralizing work orders, tracking KPIs, and managing inventory. It provides real-time insights into equipment performance, enabling data-driven decisions. For example, CMMS EcoMaint offers mobile access, allowing technicians to update tasks on the go, improving efficiency and reducing downtime.
2. Leverage Predictive Maintenance Technologies
Integrate IoT sensors and AI analytics to monitor equipment health in real time. For instance, vibration sensors can detect misalignments in motors, while temperature sensors can prevent overheating. Predictive maintenance can reduce breakdowns by up to 70% and maintenance costs by 25%, according to industry studies.
3. Optimize Preventive Maintenance Schedules
Regularly update preventive maintenance schedules based on historical data and manufacturer recommendations. For example, a conveyor belt may require lubrication every 1,000 hours of operation to prevent wear. Dynamic scheduling ensures tasks are relevant and cost-effective.
4. Conduct Root Cause Analysis
When failures occur, perform root cause analysis to identify underlying issues. For example, if a hydraulic system leaks repeatedly, check for improper seals or pressure inconsistencies rather than applying temporary fixes. This approach prevents recurring problems and saves costs.
5. Prioritize Critical Assets
Focus maintenance efforts on high-impact equipment, such as production line robots or compressors, to minimize production halts. Use KPIs like Mean Time Between Failures (MTBF) and Mean Time to Repair (MTTR) to prioritize assets based on criticality.
6. Maintain Spare Parts Inventory
Efficient inventory management ensures critical parts, like belts or bearings, are available during emergencies. Automated reordering systems can prevent stockouts, while organized storage reduces retrieval time.
7. Train and Upskill Workforce
Invest in training programs for IoT, predictive analytics, and CMMS tools. Certifications like Certified Maintenance and Reliability Professional (CMRP) enhance technical skills, while OSHA compliance training ensures safety adherence.
8. Establish Clear Communication Protocols
Effective communication between maintenance teams, production staff, and management ensures alignment on priorities. Digital work orders and real-time updates via CMMS platforms enhance transparency and coordination.
9. Collaborate with Reliable Vendors
Partner with trusted suppliers for timely delivery of spare parts and specialized services. Service-Level Agreements (SLAs) ensure quality and responsiveness, reducing delays.
10. Monitor and Analyze KPIs
Track metrics like MTBF, MTTR, and Overall Equipment Effectiveness (OEE) to evaluate maintenance performance. For example, an MTBF of 1,000 hours for a pump indicates reliable performance, while a low MTTR suggests efficient repairs. Regular analysis refines strategies and reduces downtime.
VII. Modern Technologies in Manufacturing Maintenance
Advancements in technology have revolutionized manufacturing maintenance, offering tools to enhance efficiency and predictability:
- IoT Sensors: Monitor real-time data on vibration, temperature, and pressure, enabling early detection of issues.
- AI and Machine Learning: Analyze historical and real-time data to predict failures and recommend maintenance actions. Companies like General Motors have saved millions by using AI to monitor assembly line robots.
- CMMS Software: Platforms like CMMS EcoMaint centralize maintenance tasks, track inventory, and generate performance reports, streamlining operations.
- Augmented Reality (AR): AR tools guide technicians through complex repairs, reducing errors and training time.
- Digital Twins: Virtual models of equipment simulate performance, allowing predictive testing and optimization.
VIII. How CMMS EcoMaint Enhances Manufacturing Maintenance
Vietsoft’s CMMS EcoMaint is a game-changer for manufacturing maintenance in Vietnam. This user-friendly software integrates predictive and preventive maintenance strategies, offering features like:
- Real-Time Monitoring: Tracks equipment performance and alerts technicians to anomalies.
- Work Order Management: Streamlines task assignments and progress tracking.
- Inventory Optimization: Manages spare parts to prevent stockouts and overstocking.
- Mobile Access: Enables technicians to update tasks and access data on the production floor.
By centralizing maintenance operations, CMMS EcoMaint reduces downtime, enhances efficiency, and supports data-driven decisions. Curious about how it can transform your operations? Learn more about CMMS EcoMaint here.
Contact us via hotline: 0986778578 or email: sales@vietsoft.com.vn.
IX. Practical Tips for Implementing Manufacturing Maintenance
1. Start with a Maintenance Audit: Assess current equipment conditions, maintenance schedules, and KPIs to identify gaps.
2. Set Clear Goals: Define objectives like reducing downtime by 20% or extending asset lifespan by 10 years.
3. Integrate Gradually: Begin with critical assets for predictive maintenance, then scale to other equipment.
4. Engage Employees: Involve all staff in TPM practices to foster accountability and early issue detection.
5. Review Regularly: Analyze maintenance data quarterly to adjust strategies and improve outcomes.
X. Conclusion
Manufacturing maintenance is a critical pillar of industrial success, ensuring equipment reliability, safety, and efficiency. By adopting a mix of preventive, predictive, and corrective strategies, manufacturers can minimize downtime, optimize performance, and reduce costs. Tools like Vietsoft’s CMMS EcoMaint empower maintenance teams with real-time insights, streamlined workflows, and data-driven decision-making, making it easier to achieve operational excellence.
Whether you’re managing a small factory or a large production line in Vietnam, implementing these best practices and leveraging modern technologies can transform your maintenance operations. Ready to take the next step? Discover how CMMS EcoMaint can elevate your manufacturing maintenance strategy to new heights.