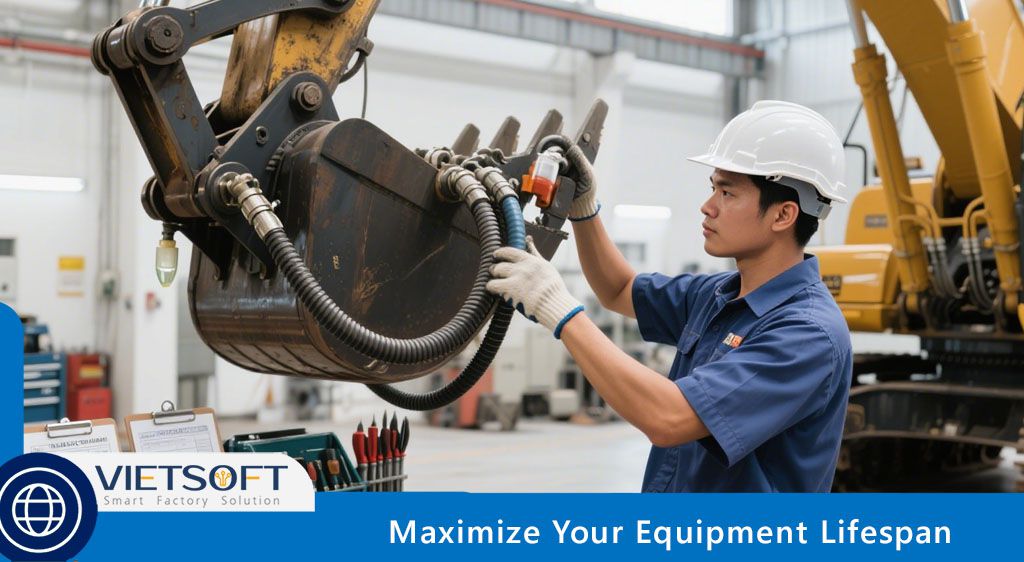
In today’s fast-paced industrial landscape, ensuring the longevity of your equipment is critical to maintaining productivity, reducing costs, and boosting return on investment (ROI). Equipment downtime, whether due to unexpected breakdowns or inadequate maintenance, can cost businesses significantly—sometimes up to 20% of productivity, according to the International Society of Automation (ISA). By focusing on strategies to maximize your equipment lifespan, companies can avoid costly disruptions and extend the operational life of their assets.
This guide dives deep into what equipment lifespan means, why it matters, and how to achieve it through proactive maintenance, cutting-edge technology, and employee training.
I. What Is Equipment Lifespan?
The lifespan of equipment refers to the duration a machine or tool can operate effectively before it requires replacement or becomes uneconomical to maintain. This period varies depending on the equipment type, usage intensity, and maintenance practices. For example, a well-maintained excavator may last between 7,000 and 10,000 hours, while neglect can reduce this to under 5,000 hours.
Maximizing equipment lifespan involves implementing strategies to extend this operational period while maintaining peak performance. Key factors influencing lifespan include:
- Usage Patterns: Overloading or improper operation accelerates wear.
- Maintenance Practices: Regular upkeep prevents minor issues from escalating.
- Environmental Conditions: Harsh environments, like extreme temperatures or humidity, can degrade components.
- Technological Upgrades: Modern tools like IoT sensors can optimize performance and detect issues early.
By addressing these factors, businesses can significantly enhance equipment durability, reduce downtime, and improve ROI.
II. Why Maximizing Equipment Lifespan Matters
Extending the lifespan of your equipment offers multiple benefits:
- Cost Savings: Fewer replacements and repairs lower long-term expenses.
- Reduced Downtime: Proactive maintenance minimizes unexpected breakdowns, ensuring consistent productivity.
- Enhanced Safety: Well-maintained equipment reduces workplace hazards.
- Improved Efficiency: Properly cared-for machines consume less energy and deliver better output.
- Sustainability: Extending equipment life reduces waste and supports eco-friendly operations.
In industries like manufacturing, construction, and mining, where equipment represents a significant investment, these benefits translate into substantial financial and operational advantages.
III. Key Strategies to Maximize Your Equipment Lifespan
To help you achieve optimal equipment longevity, we’ve outlined proven strategies grounded in decades of maintenance expertise. These approaches combine traditional best practices with modern technologies, ensuring your equipment performs at its best for as long as possible.
1. Implement a Robust Preventive Maintenance Program
Preventive maintenance is the cornerstone of equipment longevity. By scheduling regular inspections, cleanings, and part replacements, you can catch issues before they lead to costly breakdowns. Studies show that effective preventive maintenance can extend equipment life by 20-30%.
A. How to Build a Preventive Maintenance Schedule
- Consult Manufacturer Guidelines: Use the equipment’s manual to establish baseline maintenance intervals.
- Customize for Usage: Adjust schedules based on operational intensity (e.g., daily checks for heavy machinery, weekly for lighter tools).
- Include Key Tasks:
- Lubrication: Apply manufacturer-recommended lubricants to reduce friction on moving parts.
- Cleaning: Remove dirt, dust, and debris to prevent wear on joints and bearings.
- Component Checks: Inspect belts, seals, and hoses for signs of wear.
- Minimize Downtime: Schedule maintenance during off-peak hours to reduce productivity losses.
For example, a construction company might schedule weekly fluid checks for hydraulic systems and monthly inspections for engine components to ensure consistent performance.
B. Benefits of Preventive Maintenance
- Reduces unexpected downtime by up to 30%.
- Extends component life (e.g., hydraulic systems can last 20% longer with regular fluid changes).
- Lowers repair costs by addressing issues early.
2. Leverage CMMS Software for Streamlined Maintenance
Modern Computerized Maintenance Management Systems (CMMS) like Vietsoft’s CMMS EcoMaint revolutionize how businesses manage equipment maintenance. These platforms centralize maintenance data, automate scheduling, and provide real-time insights into equipment health.
A. How CMMS EcoMaint Helps Maximize Your Equipment Lifespan
- Automated Scheduling: Set reminders for maintenance tasks based on usage or time intervals.
- Real-Time Monitoring: Track equipment performance and receive alerts for anomalies.
- Digital Work Orders: Assign tasks to technicians and monitor progress through a mobile app.
- Inventory Management: Ensure spare parts and lubricants are always in stock.
- Compliance Tracking: Generate reports to meet industry safety and regulatory standards.
By integrating CMMS EcoMaint, businesses can reduce manual tracking errors, improve team collaboration, and ensure no maintenance task is overlooked.
3. Train Employees for Proper Equipment Use
Improper operation is a leading cause of premature equipment wear. For instance, using an excavator to lift loads beyond its capacity can strain components, reducing its lifespan significantly. Comprehensive training ensures employees operate equipment correctly and follow safety protocols.
Training Best Practices
- Onboarding Programs: Train new hires on equipment-specific procedures.
- Refresher Courses: Conduct annual or biannual training to reinforce best practices.
- Focus Areas:
- Correct operation techniques (e.g., avoiding unnatural angles for machinery).
- Safety protocols (e.g., using lockout/tagout systems during maintenance).
- Recognizing early signs of wear, such as unusual noises or vibrations.
- Certification: Ensure operators are certified for complex machinery.
A trained workforce not only extends equipment life but also reduces operator-caused downtime by up to 18%, according to industry studies.
4. Conduct Regular Safety and Performance Inspections
Routine inspections are critical for identifying wear, ensuring compliance, and maintaining performance. By catching issues early, you can prevent minor problems from escalating into major failures.
Inspection Checklist
- Visual Checks: Look for rust, cracks, or worn components.
- Performance Metrics: Monitor output, energy consumption, and operational speed.
- Safety Compliance: Verify lockout/tagout labels and safety mechanisms are in place.
- Environmental Factors: Check for corrosion or damage caused by humidity or dust.
For example, a manufacturing plant might inspect a laser cutter weekly for alignment issues, ensuring precision and preventing costly repairs.
5. Adopt Modern Maintenance Technologies
Technology plays a pivotal role in maximizing equipment lifespan. Tools like IoT sensors, predictive analytics, and AI-driven systems provide real-time insights into equipment health, enabling proactive maintenance.
Key Technologies to Consider
- IoT Sensors: Monitor temperature, vibration, and pressure to detect anomalies. For instance, a spike in vibration might indicate a misaligned component.
- Predictive Analytics: Use historical and real-time data to predict when parts are likely to fail.
- Digital Documentation: Replace paper records with digital systems for instant access to maintenance histories and compliance reports.
Studies show that predictive maintenance can reduce downtime by up to 30% and extend equipment life by identifying issues before they cause failures.
6. Follow Usage and Storage Best Practices
Proper usage and storage are essential for preventing unnecessary wear. Overloading equipment or storing it in harsh conditions can lead to permanent damage.
Usage Guidelines
- Adhere to Limits: Operate within the manufacturer’s specified weight, speed, and material guidelines.
- Avoid Overloading: For example, lifting beyond a crane’s capacity can strain cables and motors.
- Monitor Conditions: Adjust operations in extreme temperatures or dusty environments to minimize stress.
Storage Tips
- Controlled Environments: Store equipment in dry, temperature-controlled areas to prevent corrosion.
- Lockout Cabinets: Use clearly marked storage for tools and lockout kits to ensure easy access and safety.
- Cover Equipment: Protect machinery from dust and moisture when not in use.
7. Address Issues Promptly
Ignoring minor issues, such as unusual noises or slight performance drops, can lead to major failures. Establish a reporting system to ensure operators notify technicians immediately.
How to Encourage Prompt Reporting
- Clear Policies: Define procedures for reporting issues, including who to contact.
- Training: Educate employees on the importance of early reporting.
- Feedback Loop: Use CMMS software to track reported issues and resolutions.
For example, a technician noticing a grinding noise in a conveyor belt can schedule a bearing replacement before it causes a shutdown.
8. Build a Maintenance Culture
A strong maintenance culture empowers employees to take ownership of equipment care. Companies with robust training and accountability systems see 218% higher income per employee, according to industry research.
Steps to Build a Maintenance Culture
- Leadership Buy-In: Ensure management prioritizes maintenance as a strategic investment.
- Accountability Systems: Use CMMS software to track tasks and assign responsibilities.
- Recognition Programs: Reward technicians and operators for proactive maintenance efforts.
- Continuous Improvement: Regularly review maintenance data to identify trends and optimize processes.
9. Monitor Maintenance Costs and ROI
Tracking maintenance expenses helps balance repair costs against replacement costs. CMMS EcoMaint provides detailed expense reports, allowing managers to make data-driven decisions about when to repair or replace equipment.
Cost Monitoring Tips
- Track Expenses: Log all maintenance costs, including parts, labor, and downtime.
- Analyze ROI: Compare maintenance investments to savings from reduced downtime and replacements.
- Set Budgets: Use software to monitor spending and stay within budget.
For example, if repair costs for a 10-year-old machine exceed 50% of its replacement cost, it may be time to consider upgrading.
IV. Component-Specific Maintenance Strategies
Different equipment components require tailored maintenance approaches to maximize lifespan. Below are strategies for key systems:
1. Hydraulic Systems
- Regular Fluid Checks: Inspect fluid levels and quality every 500-1,000 hours.
- H Hose Inspections: Look for leaks or wear and replace hoses as needed.
- Fluid Changes: Replace hydraulic fluid every 1,000 hours to prevent contamination.
2. Engines
- Oil Management: Change oil every 7,000-10,000 miles or as recommended.
- Cooling Systems: Check coolant levels and clean radiators to prevent overheating.
- Filter Replacements: Replace air and fuel filters regularly to maintain efficiency.
3. Electrical Systems
- Connection Checks: Inspect for corrosion or loose connections monthly.
- Component Testing: Test sensors and emergency systems to ensure functionality.
- Wiring Maintenance: Replace worn wiring to prevent short circuits.
By focusing on component-specific care, you can reduce failures by up to 30%, according to industry data.
V. The Role of Vietsoft’s CMMS EcoMaint in Equipment Longevity
For businesses looking to streamline maintenance and maximize equipment lifespan, Vietsoft’s CMMS EcoMaint offers a comprehensive solution. This software integrates seamlessly into your operations, providing tools to:
- Automate maintenance scheduling and reminders.
- Monitor equipment health in real-time with IoT integration.
- Manage work orders and track technician performance.
- Generate compliance reports for audits.
- Optimize inventory to ensure critical parts are always available.
By adopting CMMS EcoMaint, companies can reduce downtime, improve efficiency, and extend equipment life, all while maintaining compliance with industry standards. Interested in transforming your maintenance strategy? Learn more about CMMS EcoMaint here.
Contact us via hotline: 0986778578 or email: sales@vietsoft.com.vn.
VI. FAQs About Maximizing Equipment Lifespan
1. What is the most effective way to maximize equipment lifespan?
Regular preventive maintenance, including lubrication, cleaning, and inspections, is key. Using CMMS software like EcoMaint can streamline these tasks and extend equipment life by 20-30%.
2. How does technology help extend equipment life?
IoT sensors and predictive analytics detect issues early, while CMMS software automates scheduling and tracks performance, reducing downtime by up to 30%.
3. Why is employee training important for equipment longevity?
Proper training reduces operator errors, which can cause 18% of downtime. It also ensures employees recognize early signs of wear, preventing major issues.
4. How do environmental factors impact equipment lifespan?
Extreme temperatures, humidity, and dust can accelerate wear. Proper storage and maintenance in harsh environments are critical to longevity.
5. When should I replace equipment instead of repairing it?
If repair costs exceed 50% of replacement costs or the equipment no longer meets performance needs, consider upgrading. Use CMMS software to track expenses and make informed decisions.
VII. Conclusion
Maximizing your equipment lifespan is not just about extending operational hours—it’s about optimizing performance, reducing costs, and ensuring safety. By implementing preventive maintenance, leveraging tools like CMMS EcoMaint, training employees, and adopting modern technologies, businesses can achieve significant savings and operational efficiency. A proactive approach to maintenance, supported by data-driven insights, ensures your equipment remains a valuable asset for years to come.