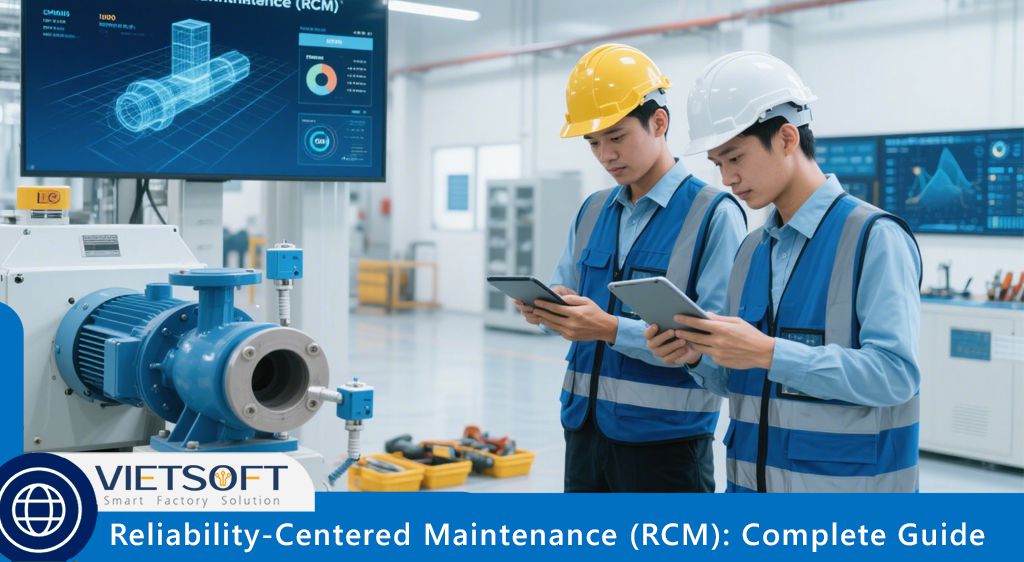
In the dynamic world of industrial operations, unexpected equipment failures can disrupt production, escalate costs, and jeopardize safety. Reliability-Centered Maintenance (RCM) provides a strategic, data-driven solution to these challenges, ensuring assets operate reliably while optimizing maintenance efforts. Originating in the aviation industry in the 1960s, RCM has evolved into a cornerstone of maintenance strategies across sectors like manufacturing, energy, and pharmaceuticals. With the integration of artificial intelligence (AI) and Industry 4.0 technologies, RCM is now more powerful, enabling businesses to predict failures, minimize downtime, and achieve significant cost savings.
This comprehensive guide delves into Reliability-Centered Maintenance, exploring its principles, implementation steps and benefits.
I. What is Reliability-Centered Maintenance (RCM)?
Reliability-Centered Maintenance is a systematic, evidence-based methodology that prioritizes preserving the functionality of critical assets over merely maintaining their condition. Unlike traditional approaches that rely on reactive repairs or rigid maintenance schedules, RCM tailors tasks to an asset’s specific functions, potential failure modes, and their consequences. By analyzing how equipment can fail and the impact of those failures, RCM ensures maintenance efforts are targeted, cost-effective, and aligned with operational and safety goals.
Key Objectives of RCM
- Maximize Equipment Reliability: Proactively address potential failures to ensure consistent asset performance.
- Enhance Safety: Prioritize maintenance tasks that mitigate risks to personnel, equipment, and the environment.
- Optimize Maintenance Costs: Focus resources on critical assets, reducing unnecessary tasks and minimizing downtime expenses.
- Ensure Regulatory Compliance: Align maintenance strategies with industry standards to meet safety and environmental regulations.
With the advent of AI and IoT, modern RCM leverages real-time data and predictive analytics to enhance decision-making, making it a vital strategy for industries aiming to stay competitive in 2025.
II. The Evolution of RCM: From Traditional to AI-Powered
1. Challenges of Traditional RCM
While Reliability-Centered Maintenance is a proven methodology, traditional implementations face several hurdles:
- Resource Intensity: Conducting detailed Failure Modes and Effects Analysis (FMEA) requires significant time and expertise, often spanning 6–18 months for complex systems.
- Static Analysis: Traditional RCM relies on point-in-time data, which may not adapt to evolving operational conditions.
- Cultural Resistance: Shifting from reactive to proactive maintenance requires organizational buy-in, which can be challenging in traditional settings.
- Integration Complexity: Connecting RCM outcomes with existing Computerized Maintenance Management Systems (CMMS) can be difficult without proper tools.
2. The RCM 4.0 Revolution
The integration of AI, IoT, and predictive analytics has transformed Reliability-Centered Maintenance into a dynamic, data-driven process, often referred to as RCM 4.0. This modern approach addresses traditional limitations by:
- Automating Failure Mode Detection: Machine learning algorithms analyze historical maintenance data, sensor inputs, and operational patterns to identify failure modes faster and more accurately than manual methods.
- Dynamic Risk Assessment: IoT sensors provide continuous equipment health data, enabling real-time prioritization of maintenance tasks based on current conditions.
- Intelligent Task Optimization: AI optimizes maintenance schedules, ensuring tasks are performed at the right time to maximize reliability and minimize costs.
- Continuous Learning: AI systems refine maintenance strategies over time, adapting to new failure patterns and operational changes.
By leveraging these technologies, RCM 4.0 delivers measurable improvements in reliability, safety, and cost efficiency, making it an essential strategy for modern industries.
III. Core Principles of Reliability-Centered Maintenance
Reliability-Centered Maintenance is built on five foundational principles that guide the development of effective maintenance programs:
· Preserve System Function: Ensure assets perform their intended functions, whether primary (e.g., a pump delivering fluid) or secondary (e.g., maintaining safety or environmental compliance).
· Identify Failure Modes: Analyze all possible ways an asset can fail to meet performance standards, considering both mechanical and operational failures.
· Prioritize Based on Risk: Rank failure modes by their impact on safety, operations, and costs to focus maintenance efforts on high-priority risks.
· Select Effective Maintenance Tasks: Choose the most appropriate strategies—predictive, preventive, or corrective—based on technical and economic feasibility.
· Sustain Continuous Improvement: Regularly monitor and refine maintenance strategies to adapt to changing equipment conditions and operational needs.
These principles ensure that Reliability-Centered Maintenance aligns maintenance efforts with business objectives, maximizing asset performance while minimizing costs.
IV. Where is Reliability-Centered Maintenance Applied?
Reliability-Centered Maintenance is widely adopted in industries where equipment reliability is critical to safety, production, and cost management. Key sectors include:
- Aviation: Ensures aircraft reliability and safety, reducing maintenance costs by 25–35% compared to traditional methods.
- Manufacturing: Optimizes production lines, minimizing downtime and ensuring consistent product quality.
- Oil and Gas: Enhances the reliability of drilling equipment and pipelines, reducing safety risks and costly shutdowns.
- Power Generation: Maintains turbines and generators to prevent power outages and ensure grid stability.
- Pharmaceuticals: Ensures equipment reliability to meet stringent regulatory standards and avoid production delays.
- Transportation: Keeps rail and fleet vehicles operational, minimizing delays and safety hazards.
In Vietnam, industries such as manufacturing and oil and gas are increasingly adopting RCM to enhance operational efficiency and comply with global standards.
V. Benefits of Reliability-Centered Maintenance
Implementing Reliability-Centered Maintenance offers numerous benefits that transform maintenance operations:
· Enhanced Equipment Reliability: Proactively addressing failure modes minimizes unexpected downtime, ensuring consistent asset performance.
· Improved Safety: Prioritizing safety-critical failure modes reduces the risk of accidents and injuries.
· Cost Optimization: Targeted maintenance tasks eliminate unnecessary work, reducing costs by up to 40% in some cases.
· Extended Asset Lifespan: Proactive maintenance extends equipment life, delaying costly replacements.
· Regulatory Compliance: RCM ensures maintenance practices align with industry standards, avoiding fines and reputational damage.
· Operational Efficiency: Focusing on critical assets improves production continuity and resource allocation.
These benefits make Reliability-Centered Maintenance a strategic tool for achieving operational excellence and competitive advantage in Vietnam’s industrial landscape.
VI. Step-by-Step Guide to Implementing RCM
Implementing Reliability-Centered Maintenance requires a structured approach to ensure success. Below is a detailed guide:
1. Step 1: Select Critical Equipment
Identify assets with the highest impact on safety, production, or costs. Use a criticality matrix to prioritize equipment based on failure consequences, repair costs, and operational importance. For example, a critical pump in a manufacturing plant may be prioritized over a non-essential air compressor.
2. Step 2: Define System Functions
Outline the primary and secondary functions of each asset, including performance expectations. For instance, a conveyor belt’s primary function is to transport goods at 50 meters per minute, while secondary functions include maintaining safety and energy efficiency.
3. Step 3: Identify Functional Failures
List all ways the asset can fail to meet its functions, such as reduced output, complete breakdown, or safety violations. For a conveyor, failures might include inability to transport goods or operating below required speed.
4. Step 4: Conduct Failure Mode and Effects Analysis (FMEA)
Analyze potential failure modes, their causes, and consequences using FMEA. For example, a conveyor failure might be caused by bearing wear, lack of lubrication, or belt misalignment. Use a risk matrix to prioritize failures based on severity, likelihood, and detectability.
Example Risk Matrix Calculation:
- Severity (S): Rated 1–10, where 10 is catastrophic (e.g., production shutdown).
- Likelihood (L): Rated 1–10, where 10 is very likely.
- Detectability (D): Rated 1–10, where 1 is easily detectable.
- Risk Priority Number (RPN) = S × L × D. Higher RPNs indicate priority failure modes.
For a bearing failure: S = 8 (major production impact), L = 4 (moderate likelihood), D = 3 (detectable with sensors). RPN = 8 × 4 × 3 = 96, indicating a high-priority failure.
5. Step 5: Select Maintenance Strategies
Choose the most effective maintenance tasks for each failure mode:
- Predictive Maintenance: Use condition-monitoring tools like vibration sensors to detect early signs of failure (e.g., bearing wear).
- Preventive Maintenance: Schedule regular tasks like lubrication based on historical failure patterns.
- Corrective Maintenance: Address failures after they occur, suitable for non-critical assets.
- Redesign or Modification: For high-risk failures, consider redesigning the asset to eliminate failure modes.
6. Step 6: Develop Detailed Maintenance Plans
Create specific maintenance tasks, including frequency, procedures, and required resources. For example, schedule monthly lubrication for a conveyor and weekly vibration checks for a pump, using historical data to optimize intervals.
7. Step 7: Implement and Monitor
Execute the maintenance plan using a CMMS to track tasks and performance. Monitor KPIs like Mean Time Between Failures (MTBF) and Overall Equipment Effectiveness (OEE) to assess effectiveness.
8. Step 8: Continuous Improvement
Regularly review and refine maintenance strategies based on performance data, feedback, and new failure patterns. AI-powered tools can automate this process, ensuring ongoing optimization.
VII. Technologies Enhancing RCM in 2025
Modern Reliability-Centered Maintenance leverages advanced technologies to enhance its effectiveness:
- IoT Sensors: Monitor equipment health in real time, tracking parameters like vibration, temperature, and pressure to detect early failure signs. For example, a sensor on a pump can detect abnormal vibrations, triggering a maintenance alert.
- AI and Predictive Analytics: Analyze historical and real-time data to predict failures and optimize maintenance schedules. AI can identify patterns, such as recurring bearing failures, and recommend targeted interventions.
- Digital Twins: Create virtual models of assets to simulate failure scenarios and test maintenance strategies without risking production. For instance, a digital twin of a turbine can predict wear under different operating conditions.
- CMMS Software: Centralize maintenance data, streamline work orders, and track KPIs for continuous improvement. Vietsoft’s CMMS EcoMaint, for example, integrates seamlessly with RCM processes.
These technologies make RCM more proactive, efficient, and data-driven, enabling organizations to stay ahead of failures and optimize resources.
VIII. Measuring RCM Success: Key Performance Indicators
To evaluate the effectiveness of Reliability-Centered Maintenance, track these KPIs:
- Overall Equipment Effectiveness (OEE): Measures availability, performance, and quality. World-class facilities achieve 85% OEE, while RCM can improve OEE by 15–25%.
Example: A factory with 60% OEE improves to 75% after RCM, indicating better uptime and performance. - Mean Time Between Failures (MTBF): Tracks average operational time between failures. An increase from 500 to 750 hours reflects improved reliability.
- Mean Time to Repair (MTTR): Measures average repair duration. Reducing MTTR from 4 to 2 hours indicates more efficient repairs.
- Planned vs. Unplanned Maintenance Ratio: Aims for 80% planned maintenance to minimize emergency repairs.
- Maintenance Cost Savings: Tracks reductions in maintenance costs, typically 22–40% with effective RCM.
Regularly reviewing these metrics ensures RCM delivers measurable results and aligns with organizational goals.
IX. Integrating RCM with Asset Management Systems
To maximize the impact of Reliability-Centered Maintenance, integration with asset management systems like CMMS is critical. A robust CMMS enhances RCM by:
- Centralizing Data: Stores maintenance history, failure data, and sensor inputs for accurate FMEA and risk analysis.
- Automating Workflows: Schedules and tracks RCM-derived maintenance tasks, ensuring timely execution.
- Providing Analytics: Offers dashboards to monitor KPIs like OEE and MTBF, enabling data-driven decisions.
- Supporting Compliance: Tracks maintenance activities to ensure alignment with industry regulations.
X. Overcoming Common RCM Implementation Challenges
Despite its benefits, Reliability-Centered Maintenance can face implementation hurdles:
- Resource Constraints: Start with a pilot project on 3–5 critical systems to demonstrate ROI before scaling up. For instance, focus on a critical production line in a manufacturing plant.
- Cultural Resistance: Overcome through training, leadership support, and showcasing early wins, such as a 20% reduction in downtime after initial RCM implementation.
- Data Gaps: Use IoT sensors and CMMS software to collect and centralize data, ensuring accurate failure analysis.
- Integration Issues: Select a CMMS like Vietsoft’s EcoMaint that seamlessly integrates with RCM processes and existing workflows.
By addressing these challenges, organizations can ensure successful RCM adoption and long-term reliability improvements.
XI. How Vietsoft’s CMMS EcoMaint Supports RCM
Vietsoft’s CMMS EcoMaint is a powerful tool designed to enhance Reliability-Centered Maintenance for industries like manufacturing, oil and gas, and pharmaceuticals in Vietnam. Key features include:
- Real-Time Monitoring: IoT sensors track equipment health, providing data for predictive maintenance and failure mode analysis.
- Automated Work Orders: Streamlines scheduling and tracking of RCM-derived tasks, ensuring timely execution.
- AI-Driven Insights: Analyzes failure patterns and optimizes maintenance schedules, reducing downtime and costs.
- Compliance Management: Ensures maintenance activities align with Vietnam’s industry regulations, supporting RCM’s focus on safety and compliance.
By integrating with RCM methodologies, EcoMaint empowers maintenance teams to proactively manage assets, improve reliability, and achieve operational excellence. Discover the CMMS EcoMaint solution here.
Contact us for consultation via hotline: 0986778578 or email: sales@vietsoft.com.vn.
XII. The Future of Reliability-Centered Maintenance
As industries embrace Industry 4.0, Reliability-Centered Maintenance is evolving to incorporate advanced technologies and sustainability goals:
- Autonomous Maintenance: AI systems will execute routine tasks and make repair decisions, freeing technicians for strategic work.
- Augmented Reality (AR): AR tools will guide technicians through complex repairs, improving efficiency and accuracy.
- Sustainability Focus: RCM will prioritize energy efficiency and waste reduction, aligning maintenance with environmental goals.
- Prescriptive Maintenance: Next-generation RCM will automatically prescribe and execute optimal maintenance strategies based on real-time data.
These advancements will make RCM more efficient, sustainable, and aligned with Vietnam’s growing focus on smart manufacturing and sustainability.
XIII. Conclusion: Unlocking the Power of RCM
Reliability-Centered Maintenance is a transformative approach that ensures equipment reliability, enhances safety, and optimizes costs. By integrating AI, IoT, and modern CMMS platforms like Vietsoft’s EcoMaint, organizations can overcome traditional RCM challenges and achieve superior outcomes. Whether in manufacturing, oil and gas, or pharmaceuticals, RCM provides a structured, data-driven framework to maximize asset performance and drive operational excellence in Vietnam’s industrial sector.