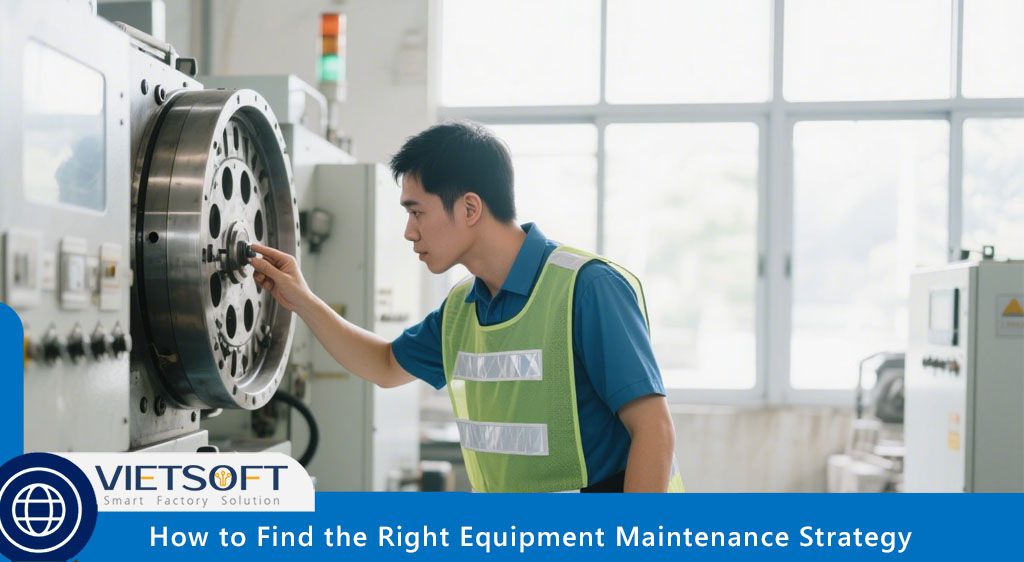
In today’s fast-paced industrial landscape, ensuring equipment reliability and minimizing downtime are critical for maintaining productivity, safety, and profitability. Selecting the right equipment maintenance strategy is not just a technical decision but a strategic one that can significantly impact your bottom line. Whether you manage a manufacturing plant, a fleet of vehicles, or a complex industrial facility, understanding and implementing an effective maintenance approach tailored to your assets is essential.
This comprehensive guide explores what an equipment maintenance strategy entails, why it matters, the different types of maintenance strategies, and how to choose the right equipment maintenance strategy for your organization.
I. Why Equipment Maintenance Strategy Matters
Equipment maintenance is the backbone of operational efficiency in any asset-intensive industry. Without a well-defined strategy, even minor equipment issues can escalate into costly breakdowns, production delays, or safety hazards. Here’s why finding the right equipment maintenance strategy is critical:
- Minimize Downtime: Unplanned equipment failures can halt production, disrupt supply chains, and lead to significant revenue losses. A robust maintenance strategy identifies issues early, reducing downtime.
- Extend Asset Lifespan: Regular maintenance, such as lubrication or calibration, can extend equipment life by years, delaying costly replacements. A well-maintained pump, for instance, might last 15 years instead of 10.
- Enhance Safety: Faulty equipment, like a malfunctioning hydraulic system, poses risks to workers. Proactive maintenance ensures safety by preventing hazardous failures.
- Boost Efficiency: Well-maintained machines operate at peak performance, reducing energy waste and improving output quality.
- Reduce Costs: Emergency repairs often come with premium costs for parts, labor, and expedited services. Proactive maintenance is typically more cost-effective.
- Ensure Compliance: Industries like manufacturing, oil and gas, or food processing often face strict regulatory requirements. Proper maintenance ensures compliance with safety and environmental standards.
- Enable Data-Driven Decisions: Maintenance logs provide insights into equipment performance trends, helping you prioritize resources and plan effectively.
By implementing the right equipment maintenance strategy, businesses can achieve operational excellence, reduce risks, and maintain a competitive edge. But with so many maintenance approaches available, how do you choose the best one for your needs?
II. Understanding Equipment Maintenance Strategies
An equipment maintenance strategy is a structured plan to manage and maintain assets to ensure optimal performance, reliability, and longevity. It involves selecting the appropriate maintenance type based on equipment criticality, usage patterns, and organizational goals. Below, we explore the primary types of maintenance strategies, their applications, and their benefits:
1. Reactive Maintenance (Run-to-Failure)
Reactive maintenance involves repairing or replacing equipment only after it fails. It’s the simplest approach, requiring minimal planning and upfront investment.
- How It Works: Maintenance is triggered by a failure event, such as a motor burnout or a conveyor belt snapping. Teams focus on restoring functionality as quickly as possible.
- When to Use: Best for non-critical, low-cost assets where downtime has minimal impact, like replacing light bulbs or office printers.
- Pros:
- No upfront costs or planning required.
- Suitable for assets with low replacement costs.
- Cons:
- High risk of unplanned downtime, which can disrupt operations.
- Emergency repairs are often costly and time-consuming.
- Potential safety risks from unexpected failures.
2. Preventive Maintenance (Scheduled Maintenance)
Preventive maintenance involves performing regular maintenance tasks based on time or usage intervals, regardless of the equipment’s condition. It aims to prevent failures before they occur.
- How It Works: Tasks like oil changes, filter replacements, or inspections are scheduled based on manufacturer recommendations or historical data (e.g., every 3 months or 1,000 operating hours).
- When to Use: Ideal for equipment with predictable wear patterns or critical assets where failure is costly, such as production line machinery or HVAC systems.
- Pros:
- Reduces unexpected breakdowns.
- Extends equipment lifespan.
- Simplifies compliance with regulatory requirements.
- Cons:
- Risk of over-maintenance, leading to unnecessary costs.
- May not catch issues that arise between scheduled intervals.
3. Condition-Based Maintenance (CBM)
Condition-based maintenance relies on monitoring the actual condition of equipment to determine when maintenance is needed. It uses visual inspections or simple sensors to detect signs of wear.
- How It Works: Maintenance is triggered by measurable indicators, such as abnormal vibrations or oil contamination, identified through tools like vibration meters or oil analysis kits.
- When to Use: Suitable for assets with variable operating conditions, like pumps or compressors, where wear isn’t always predictable.
- Pros:
- Reduces unnecessary maintenance by focusing on actual needs.
- Cost-effective for mid-priority assets.
- Cons:
- Requires investment in monitoring tools and trained personnel.
- May miss subtle issues without advanced analytics.
4. Predictive Maintenance (PdM)
Predictive maintenance uses advanced analytics and real-time data to predict when equipment is likely to fail, allowing maintenance to be scheduled just in time.
- How It Works: Sensors monitor parameters like temperature, pressure, or vibration, and machine learning algorithms analyze data to predict failures. For instance, a spike in motor temperature might indicate an impending failure.
- When to Use: Best for critical, high-value assets where downtime is costly, such as turbines in power plants or heavy machinery in mining.
- Pros:
- Minimizes downtime by addressing issues before they cause failures.
- Optimizes maintenance schedules, reducing unnecessary work.
- Extends equipment life through precise interventions.
- Cons:
- High initial costs for sensors, software, and training.
- Requires expertise in data analysis.
5. Reliability-Centered Maintenance (RCM)
Reliability-centered maintenance is a strategic approach that combines multiple maintenance types based on equipment criticality and failure modes. It aims to maximize reliability while optimizing resources.
- How It Works: RCM involves analyzing each asset’s functions, failure modes, and consequences to assign the most appropriate maintenance strategy. For example, critical assets might use predictive maintenance, while non-critical ones use reactive maintenance.
- When to Use: Ideal for facilities with diverse equipment, such as manufacturing plants or utilities, where a one-size-fits-all approach isn’t feasible.
- Pros:
- Tailors maintenance to specific asset needs.
- Optimizes resource allocation.
- Enhances overall reliability and safety.
- Cons:
- Complex to implement, requiring detailed data and analysis.
- Time-intensive setup process.
6. Risk-Based Maintenance (RbM)
Risk-based maintenance prioritizes maintenance tasks based on the likelihood and consequences of equipment failure. It focuses resources on high-risk assets.
- How It Works: Assets are evaluated using a risk matrix that considers the probability of failure (PoF) and consequence of failure (CoF). Maintenance is prioritized for assets with high risk scores.
- When to Use: Suitable for organizations with limited budgets or resources, such as small factories or startups.
- Pros:
- Focuses resources on critical assets.
- Reduces costs by avoiding over-maintenance of low-risk equipment.
- Cons:
- Requires accurate risk assessments.
- May overlook low-risk assets until failures occur.
7. Prescriptive Maintenance (RxM)
Prescriptive maintenance goes beyond predicting failures by recommending specific actions to prevent them, using advanced analytics and AI.
- How It Works: AI systems analyze sensor data, historical records, and operational conditions to suggest precise interventions, such as adjusting machine speed to delay failure.
- When to Use: Best for highly automated systems or critical assets in industries like aerospace or energy, where precision is paramount.
- Pros:
- Offers actionable solutions to prevent failures.
- Maximizes efficiency by tailoring interventions.
- Cons:
- Extremely high setup costs for AI and analytics infrastructure.
- Requires highly skilled personnel.
III. How to Choose the Right Equipment Maintenance Strategy
Selecting the right equipment maintenance strategy requires a systematic approach that balances equipment needs, operational goals, and available resources. Below is a step-by-step guide to help you make an informed decision, enriched with practical insights and examples.
1. Step 1: Assess Your Equipment Inventory
To choose the right equipment maintenance strategy, start by understanding your assets. Create a detailed inventory that includes:
- Equipment Type and Function: Identify each asset’s role in operations (e.g., a conveyor belt in a factory or a generator in a hospital).
- Age and Condition: Older equipment may require more frequent maintenance, while newer assets might need less.
- Criticality: Conduct a criticality analysis to rank assets based on their impact on safety, production, and costs. For example, a failure in a production line motor might halt operations, while a backup generator failure might have less immediate impact.
- Usage Patterns: Note whether equipment runs continuously or intermittently, as this affects wear rates.
2. Step 2: Evaluate Current Maintenance Processes
Analyze your existing maintenance practices to identify strengths and weaknesses. Key questions include:
- What’s the current downtime rate? Use metrics like Mean Time Between Failures (MTBF) to gauge reliability.
- Are maintenance costs sustainable? Review work order expenses to spot inefficiencies.
- Are there recurring issues? Frequent breakdowns may indicate a need for a more proactive strategy.
3. Step 3: Define Maintenance Goals
Set clear, measurable objectives to guide your strategy. Common goals include:
- Reducing Downtime: Aim to cut unplanned downtime by 20% within a year.
- Lowering Costs: Target a 15% reduction in maintenance expenses by optimizing schedules.
- Improving Safety: Ensure zero safety incidents related to equipment failures.
- Extending Asset Life: Increase the lifespan of critical assets by 25%.
4. Step 4: Compare Maintenance Strategies
Evaluate each maintenance strategy based on its suitability for your equipment, budget, and goals. Use a comparison table like the one below to weigh options:
Strategy |
Trigger |
Best For |
Cost |
Complexity |
Reactive |
Equipment failure |
Non-critical assets |
Low |
Low |
Preventive |
Time/usage-based |
Predictable wear, critical assets |
Medium |
Medium |
Condition-Based |
Measurable indicators |
Variable conditions |
Medium |
Medium |
Predictive |
Sensor data, analytics |
High-value, critical assets |
High |
High |
Reliability-Centered |
Asset-specific analysis |
Diverse equipment |
High |
High |
Risk-Based |
Risk assessment |
Limited budgets, high-risk assets |
Medium |
Medium |
Prescriptive |
AI-driven recommendations |
Highly automated systems |
Very High |
Very High |
5. Step 5: Consider Resources and Capabilities
Assess your organization’s resources, including:
- Budget: Predictive and prescriptive maintenance require significant investments in sensors and software.
- Staff Skills: Ensure your team has the expertise to implement and maintain the chosen strategy.
- Technology: Check if you have access to tools like CMMS software or IoT sensors.
6. Step 6: Implement and Monitor the Strategy
Once you’ve selected the right equipment maintenance strategy, implement it with a clear plan:
- Develop a Maintenance Plan: Outline tasks, schedules, and responsibilities. For example, schedule monthly inspections for preventive maintenance or set sensor thresholds for condition-based maintenance.
- Train Staff: Ensure technicians understand the new strategy and tools.
- Use a CMMS: Tools like CMMS EcoMaint can automate scheduling, track work orders, and provide real-time insights.
Monitor performance using key metrics like downtime, maintenance costs, and MTBF. Adjust the strategy as needed based on data and feedback.
7. Step 7: Continuously Improve
Maintenance strategies evolve with equipment age, operational demands, and technological advancements. Regularly review your strategy by:
- Analyzing Data: Use CMMS reports to identify trends, such as recurring failures or over-maintenance.
- Gathering Feedback: Consult technicians for insights on practical challenges.
- Adopting New Technologies: Explore emerging tools like IoT or AI to enhance your strategy.
IV. How Vietsoft’s CMMS EcoMaint Supports Your Maintenance Strategy
Implementing the right equipment maintenance strategy requires robust tools to streamline processes and provide actionable insights. Vietsoft’s CMMS EcoMaint is a powerful, mobile-first computerized maintenance management system designed to support various maintenance strategies, from preventive to predictive. Here’s how it can transform your maintenance operations:
- Automated Scheduling: EcoMaint allows you to schedule preventive and usage-based maintenance tasks automatically, ensuring no critical work is missed.
- Real-Time Monitoring: Integrate with IoT sensors to track equipment conditions, enabling condition-based and predictive maintenance. Alerts are triggered when parameters like vibration or temperature exceed thresholds.
- Mobile Accessibility: Technicians can log issues, complete checklists, and upload images from the field, even offline, ensuring seamless communication.
- Data-Driven Insights: EcoMaint’s dashboards provide analytics on downtime, costs, and asset performance, helping you refine your strategy.
- Compliance Management: Store maintenance records for audits, ensuring compliance with industry regulations.
- Scalability: Whether you manage a single facility or multiple sites, EcoMaint adapts to your needs, supporting hybrid strategies like RCM or RbM.
By leveraging CMMS EcoMaint, your team can move from reactive firefighting to proactive control, maximizing equipment reliability and efficiency. Learn more about CMMS EcoMaint here.
Contact us via hotline: 0986778578 or email: sales@vietsoft.com.vn.
V. Emerging Trends in Equipment Maintenance
Staying ahead in maintenance requires adopting new technologies and trends. Here are some innovations shaping the right equipment maintenance strategy in 2025:
- Internet of Things (IoT): IoT sensors provide real-time data on equipment health, enabling predictive and condition-based maintenance. For example, IoT-enabled pumps can alert technicians to pressure drops before failures occur.
- Artificial Intelligence (AI): AI analyzes vast datasets to predict failures and recommend precise interventions, as seen in prescriptive maintenance.
- Augmented Reality (AR): AR headsets guide technicians through complex repairs, reducing errors and downtime.
- Energy Efficiency: Maintenance strategies now focus on optimizing energy use, such as scheduling maintenance to reduce machine idling.
- Digital Twins: Virtual models of equipment simulate performance, helping predict maintenance needs and optimize schedules.
VI. Common Mistakes to Avoid
When selecting the right equipment maintenance strategy, avoid these pitfalls:
- Ignoring Equipment Needs: Applying the same strategy to all assets can lead to inefficiencies. Tailor strategies to each asset’s criticality and usage.
- Focusing Solely on Costs: Choosing the cheapest option, like reactive maintenance, may increase long-term costs due to downtime.
- Excluding Stakeholders: Involve maintenance teams, operators, and management to ensure buy-in and practical implementation.
- Overcomplicating Strategies: Start with simple approaches like preventive maintenance before scaling to predictive or prescriptive methods.
- Neglecting Reviews: Failing to monitor and adjust your strategy can result in outdated practices that don’t meet evolving needs.
VII. Conclusion
Choosing the right equipment maintenance strategy is a critical decision that impacts your organization’s efficiency, safety, and profitability. By assessing your equipment, setting clear goals, comparing strategies, and leveraging tools like CMMS EcoMaint, you can build a tailored maintenance plan that maximizes asset performance while minimizing costs. Regularly review and adapt your strategy to stay ahead of operational challenges and technological advancements.