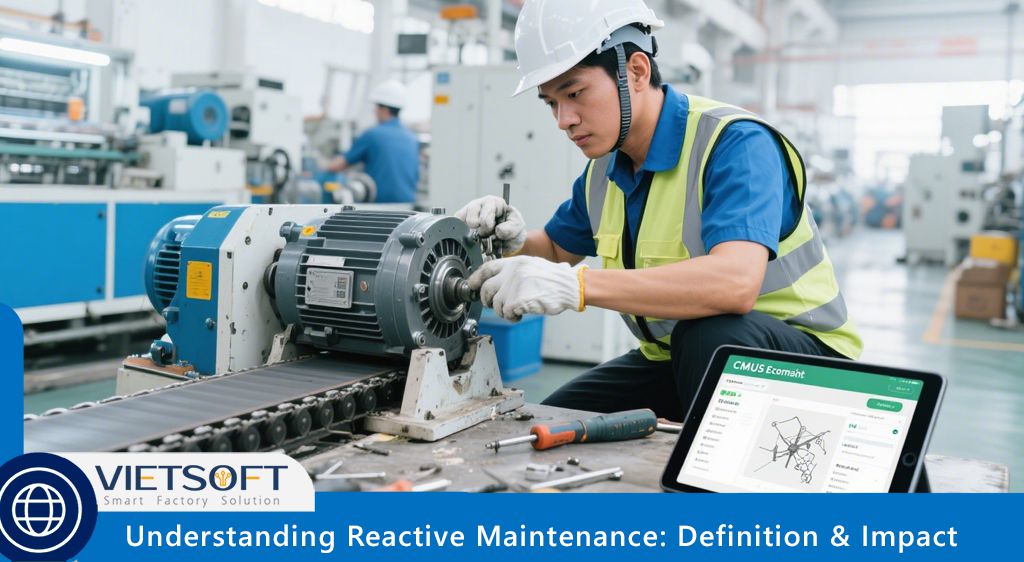
Reactive maintenance, often referred to as breakdown or run-to-failure maintenance, is a widely used strategy in industrial settings, particularly in manufacturing and production facilities. This approach involves repairing or replacing equipment only after it fails, prioritizing immediate fixes over preventive measures. While reactive maintenance may seem cost-effective at first glance, its long-term implications can significantly affect operational efficiency, safety, and profitability. In this comprehensive guide, we explore the essence of reactive maintenance, its role in industrial maintenance strategies, its benefits and challenges.
I. What is Reactive Maintenance? A Core Industrial Strategy
Reactive maintenance is a maintenance approach where repairs are initiated only after equipment failure or significant performance degradation occurs. Unlike preventive or predictive maintenance, which rely on scheduled inspections or data-driven predictions, reactive maintenance adopts a “fix it when it breaks” philosophy. This strategy is common in facilities with limited maintenance budgets or for non-critical assets where downtime has minimal impact.
In manufacturing, reactive maintenance typically involves a sequence of steps triggered by equipment failure:
- Failure Detection: Operators or sensors identify a malfunction, such as a machine stopping or producing defective outputs.
- Diagnosis: Maintenance technicians assess the issue to determine the cause and extent of the damage.
- Resource Allocation: Teams source necessary spare parts, often under time pressure, which may involve expedited shipping or external vendors.
- Repair or Replacement: Technicians perform the necessary repairs or replace the failed component, following safety protocols like Lockout/Tagout (LOTO).
- Testing and Restart: The equipment is tested to ensure it meets operational standards before resuming production.
A key metric for evaluating reactive maintenance is the Mean Time To Repair (MTTR), which measures the average time from failure to restoration. High MTTR in reactive-heavy environments can lead to significant production losses, making it critical to understand when and how this strategy should be applied.
II. The Role of Reactive Maintenance in Industrial Operations
Reactive maintenance plays a specific role in industrial maintenance strategies, particularly in scenarios where proactive measures may not be cost-effective. Its simplicity makes it appealing for certain applications, but its limitations require careful consideration. Below, we explore the role of reactive maintenance in modern manufacturing:
1. Addressing Non-Critical Assets
Reactive maintenance is often suitable for equipment with low criticality, where failure does not disrupt core production processes or compromise safety. For example, a light bulb in a non-essential area of a factory or a non-driven conveyor roller can be replaced after failure without significant operational impact.
2. Emergency Response to Unexpected Failures
Even in facilities with robust preventive maintenance programs, unexpected failures can occur. Reactive maintenance serves as a fallback strategy to address these incidents, ensuring operations resume as quickly as possible.
3. Cost-Driven Decision-Making
In smaller manufacturing plants or those under financial constraints, reactive maintenance may be adopted to minimize upfront maintenance costs. By focusing resources on repairs only when needed, companies can allocate budgets to other priorities, though this often comes at the expense of long-term efficiency.
III. Types of Reactive Maintenance in Industrial Settings
Reactive maintenance encompasses several subcategories, each with distinct characteristics and applications. Understanding these types helps maintenance teams decide when reactive maintenance is appropriate:
1. Breakdown Maintenance
Breakdown maintenance occurs when equipment completely fails and requires immediate repair or replacement. This is the most reactive form, often applied to non-critical assets where downtime has minimal impact. For example, replacing a worn belt on a secondary conveyor system after it breaks is a classic case of breakdown maintenance.
2. Run-to-Failure (RTF) Maintenance
Run-to-Failure is a deliberate strategy where equipment is allowed to operate until it fails, with repairs planned in advance. This approach is suitable for low-cost, easily replaceable components, such as small motors or fuses, where the cost of preventive maintenance outweighs replacement costs. RTF requires careful planning to ensure spare parts and labor are readily available to minimize downtime.
3. Corrective Maintenance
Corrective maintenance involves addressing faults identified before complete failure, often during unrelated inspections. For instance, a technician might notice a loose bearing during a routine check and schedule its replacement. While reactive, this approach can prevent more severe breakdowns if issues are caught early.
4. Emergency Maintenance
Emergency maintenance is the most urgent form of reactive maintenance, triggered by sudden failures that pose safety risks or halt critical operations. For example, a hydraulic leak in a press machine may require immediate action to prevent safety hazards or production stoppages. This type is costly due to overtime labor, expedited parts, and production losses.
IV. Benefits of Reactive Maintenance in Manufacturing
While reactive maintenance is often criticized for its inefficiencies, it offers specific advantages in certain contexts:
1. Lower Initial Costs
Reactive maintenance requires minimal upfront investment in planning, scheduling, or monitoring technologies. For small facilities or non-critical assets, this can reduce immediate maintenance expenses, allowing resources to be allocated elsewhere.
2. Simplified Operations
With no need for complex maintenance schedules or predictive analytics, reactive maintenance is straightforward. Maintenance teams focus solely on addressing failures as they occur, reducing administrative overhead.
3. Resource Efficiency for Non-Critical Assets
For low-value or easily replaceable equipment, reactive maintenance avoids unnecessary labor or parts costs. For instance, replacing a burned-out light bulb only when it fails is more cost-effective than scheduling regular replacements.
4. Flexibility in Resource Allocation
Reactive maintenance allows maintenance teams to prioritize other tasks until a failure occurs, providing flexibility in workforce management. This can be beneficial in facilities with limited maintenance staff.
V. Challenges of Reactive Maintenance in Industrial Environments
Despite its benefits, reactive maintenance poses significant challenges, particularly for critical assets in manufacturing plants. Below are the key drawbacks:
1. Unplanned Downtime
Unexpected equipment failures lead to unplanned downtime, which can halt production lines and disrupt supply chains. For example, a sudden failure in a CNC machine can stop an entire assembly line, causing delays and financial losses.
2. Higher Long-Term Costs
While reactive maintenance saves on upfront costs, emergency repairs are often three to ten times more expensive than planned interventions. Expedited shipping, overtime labor, and collateral damage to equipment drive up expenses.
3. Reduced Equipment Lifespan
Running equipment to failure accelerates wear and tear, shortening asset lifespan. For instance, a motor left unmaintained may fail prematurely, necessitating costly replacements sooner than expected.
4. Safety Risks
Sudden equipment failures can create hazardous conditions, such as electrical faults or uncontrolled machine movements. Rushed repairs may also lead to compromised safety protocols, increasing the risk of accidents.
5. Impact on Product Quality
Degraded equipment often produces substandard outputs, leading to higher scrap rates, rework, and customer returns. For example, a worn cutting tool may produce out-of-spec parts, increasing the Cost of Poor Quality (COPQ).
6. Employee Burnout
The constant “firefighting” mode of reactive maintenance creates stress for technicians, leading to burnout and high turnover. This also affects operators, who face frustration from unreliable equipment.
7. Energy and Environmental Impact
Faulty equipment often consumes more energy, increasing utility costs. Fluid leaks or improper disposal of failed components can also harm the environment, conflicting with sustainability goals.
VI. Strategic Applications of Reactive Maintenance
While reactive maintenance is not ideal for critical assets, it can be strategically applied in specific scenarios:
1, Non-Critical Equipment
Assets with minimal impact on production, such as general lighting or non-essential tools, are suitable for reactive maintenance. The cost of failure is low, making proactive measures unnecessary.
2. Low-Cost Replacements
For inexpensive components, like standard bolts or small sensors, the cost of replacement is often lower than the cost of regular maintenance. Reactive maintenance is a practical choice in these cases.
3. End-of-Life Equipment
Equipment nearing the end of its service life may not benefit from preventive maintenance. Allowing it to run to failure and replacing it can be more cost-effective than prolonging its operation.
4. Complementary Strategy
Reactive maintenance can complement proactive strategies in a balanced maintenance program. For instance, a facility might use predictive maintenance for critical machinery and reactive maintenance for secondary assets.
VII. Reactive vs. Proactive Maintenance: A Comparative Analysis
To understand the role of reactive maintenance, it’s essential to compare it with proactive strategies like preventive and predictive maintenance:
- Reactive Maintenance:
- Timing: Performed after failure.
- Cost Structure: Low upfront costs, high emergency repair costs.
- Downtime: Unpredictable and often significant.
- Workload: High-pressure, reactive tasks with minimal planning.
- Suitability: Best for non-critical, low-cost assets.
- Preventive Maintenance:
- Timing: Scheduled based on time or usage intervals.
- Cost Structure: Predictable costs, but may include unnecessary servicing.
- Downtime: Planned downtime, reducing unexpected interruptions.
- Workload: Structured, with regular inspections and maintenance tasks.
- Suitability: Ideal for critical assets with predictable wear patterns.
- Predictive Maintenance:
- Timing: Based on real-time data and condition monitoring.
- Cost Structure: Optimized costs, targeting maintenance only when needed.
- Downtime: Minimized through early intervention.
- Workload: Data-driven, requiring advanced tools and analytics.
- Suitability: Best for high-value, complex assets in smart manufacturing.
A balanced maintenance strategy often combines these approaches, using reactive maintenance for non-critical assets and proactive methods for critical ones to optimize costs and performance.
VIII. Optimizing Reactive Maintenance with CMMS EcoMaint
While reactive maintenance has its place, relying solely on it can lead to inefficiencies and risks. Modern tools like CMMS EcoMaint, developed by Vietsoft, offer a powerful solution to manage and optimize maintenance workflows, including reactive maintenance, while transitioning to proactive strategies.
1. Streamlined Issue Reporting
CMMS EcoMaint enables instant failure reporting through mobile apps or QR code scanning. Operators can log issues directly from the shop floor, attaching photos or videos to aid diagnosis. This reduces response times and ensures technicians have the information needed for efficient repairs.
2. Comprehensive Asset Tracking
The software provides real-time visibility into asset performance, maintenance history, and spare parts inventory. This helps maintenance teams prepare for reactive repairs by ensuring parts are available, minimizing downtime.
3. Data-Driven Insights
CMMS EcoMaint integrates condition-based monitoring and predictive analytics, allowing facilities to shift from reactive to proactive maintenance. By analyzing failure patterns, the system identifies opportunities to implement preventive or predictive measures, reducing the frequency of reactive interventions.
4. Work Order Management
The platform streamlines work order creation, assignment, and tracking, ensuring reactive maintenance tasks are prioritized and completed efficiently. Automated workflows reduce administrative burdens and improve response times.
5. Cost Optimization
By combining reactive and proactive strategies, CMMS EcoMaint helps facilities balance maintenance budgets. For non-critical assets, reactive maintenance can be applied cost-effectively, while critical assets benefit from preventive and predictive approaches.
To learn how CMMS EcoMaint can transform your maintenance strategy, Explore the CMMS EcoMaint solution here.
Contact us for consultation via hotline: 0986778578 or email: sales@vietsoft.com.vn.
IX. Best Practices for Integrating Reactive Maintenance
To maximize the benefits of reactive maintenance while minimizing its drawbacks, consider the following best practices:
· Prioritize Asset Criticality: Use reactive maintenance only for non-critical assets. Conduct a criticality analysis to identify equipment where failure has minimal impact.
· Maintain Spare Parts Inventory: Stock commonly used parts for quick replacements during reactive repairs, reducing downtime.
· Train Maintenance Teams: Equip technicians with the skills and tools to diagnose and repair failures efficiently, minimizing MTTR.
· Document Failures: Log all reactive maintenance activities in a CMMS to analyze failure patterns and identify opportunities for proactive measures.
· Balance with Proactive Strategies: Combine reactive maintenance with preventive and predictive approaches to optimize asset performance and reduce overall costs.
X. The Future of Maintenance: Moving Beyond Reactive Strategies
As manufacturing evolves toward Industry 4.0, the reliance on reactive maintenance is diminishing. Smart factories leverage IoT sensors, AI, and CMMS platforms like EcoMaint to predict failures and optimize maintenance schedules. While reactive maintenance will always have a role in addressing unexpected failures, its use should be strategic and limited to specific scenarios.
By adopting a balanced maintenance approach, facilities can achieve:
- Higher Overall Equipment Effectiveness (OEE): Minimizing downtime and preventative maintenance improves availability and performance.
- Improved Safety: Proactive strategies reduce the risk of hazardous failures.
- Cost Savings: Optimized maintenance reduces emergency repair costs and extends asset lifespan.
- Sustainability: Efficient equipment consumes less energy and produces less waste.
XI. Conclusion: Strategic Reactive Maintenance for Modern Manufacturing
Reactive maintenance remains a viable strategy for non-critical assets or resource-constrained environments, but its limitations make it unsuitable as a primary approach for critical equipment. By understanding its role, benefits, and challenges, maintenance teams can strategically apply reactive maintenance while transitioning to proactive strategies for critical assets. Tools like CMMS EcoMaint from Vietsoft empower facilities to streamline reactive repairs, track asset performance, and adopt data-driven maintenance practices.