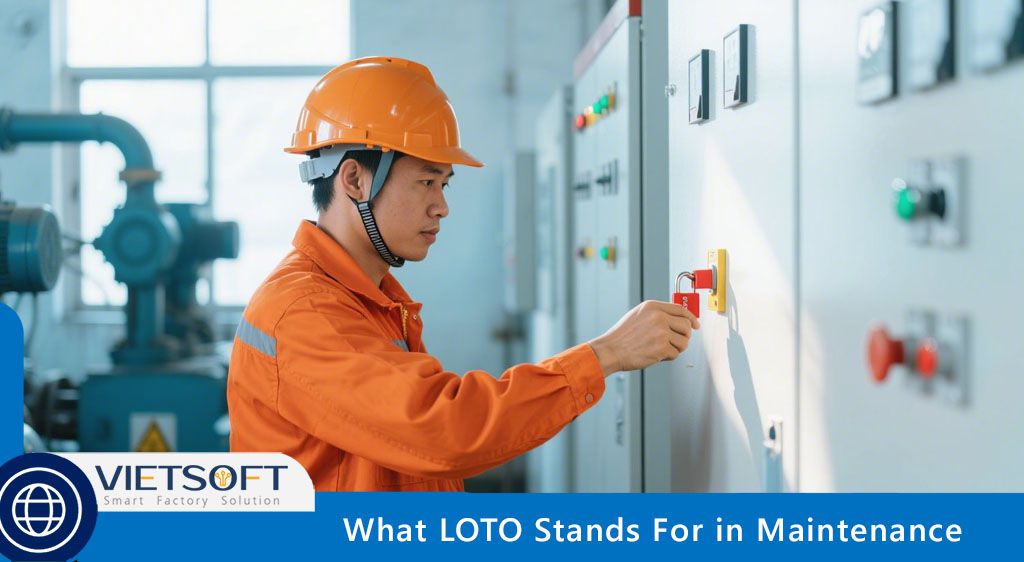
Lockout/Tagout, commonly referred to as LOTO, is a cornerstone of workplace safety in maintenance operations. This critical procedure ensures that hazardous energy sources are controlled, protecting workers from life-threatening accidents. This article dives deep into what LOTO stands for, its role in maintenance, and how it integrates with modern tools like CMMS EcoMaint to enhance safety and compliance.
I. Understanding What LOTO Stands For
LOTO stands for Lockout/Tagout, a safety protocol designed to prevent the unexpected release of hazardous energy during maintenance or servicing of equipment. The term encapsulates two key actions:
- Lockout: Physically securing an energy-isolating device (such as a switch, valve, or circuit breaker) in a safe position to prevent equipment from being energized. This ensures that machinery remains inoperative during maintenance.
- Tagout: Attaching a visible tag to the locked device, clearly indicating that the equipment is under maintenance and must not be operated. The tag typically includes details such as the name of the authorized worker and the reason for the lockout.
Together, these steps form a systematic approach to controlling energy sources like electrical, mechanical, hydraulic, pneumatic, thermal, or chemical energy. LOTO is not just a procedure but a critical safety net that protects workers from injuries caused by unintended equipment startups or energy releases.
II. Why LOTO Matters in Maintenance
Maintenance tasks often involve working with complex machinery that can pose significant risks if not properly isolated. Without LOTO, a simple oversight—such as a coworker unknowingly restarting a machine—can lead to severe injuries, including electrical shocks, amputations, or burns. According to the Occupational Safety and Health Administration (OSHA), LOTO procedures prevent approximately 50,000 injuries and 120 fatalities annually in the United States alone.
LOTO is particularly vital in industries such as manufacturing, oil and gas, food processing, and construction, where heavy machinery and high-energy systems are prevalent. For instance, a technician servicing a hydraulic press could face catastrophic injury if the system is accidentally reactivated. By implementing LOTO, maintenance teams gain control over equipment, ensuring that it remains de-energized and safe throughout the servicing process.
Beyond safety, LOTO enhances operational efficiency by reducing downtime caused by accidents and fostering clear communication across teams. It ensures that everyone—from operators to contractors—knows which equipment is off-limits, preventing costly disruptions and promoting a culture of safety.
III. Core Components of a LOTO Program
A robust LOTO program is more than just applying locks and tags; it’s a comprehensive system that integrates procedures, training, equipment, and oversight. Below are the essential components that make a LOTO program effective:
1. Detailed Written Procedures
Each piece of equipment requires a specific LOTO procedure tailored to its energy sources and operational characteristics. These procedures should include step-by-step instructions for shutting down, isolating, locking, tagging, and verifying the equipment’s de-energized state. Generic procedures are insufficient, as they fail to address the unique hazards of individual machines.
2. Standardized LOTO Devices
LOTO relies on high-quality, durable devices such as padlocks, hasps, valve covers, and circuit breaker locks. Each lock should be uniquely keyed and assigned to a specific worker, ensuring that only the authorized person can remove it. Tags must be clear, durable, and include critical information like the worker’s name and the date of application.
3. Comprehensive Training
Training is the backbone of LOTO compliance. Workers are divided into two categories:
- Authorized Employees: Those trained to perform LOTO procedures, including applying and removing locks and tags.
- Affected Employees: Those who work near the equipment and need to understand LOTO to avoid interfering with locked-out systems.
Training should cover the purpose of LOTO, specific procedures, and the consequences of non-compliance. Regular refresher courses are essential to keep skills sharp and incorporate updates to equipment or regulations.
4. Periodic Inspections
OSHA mandates annual audits of LOTO programs to ensure compliance and effectiveness. These inspections verify that procedures are followed, devices are functional, and training is up to date. Audits also identify gaps in the program, such as outdated procedures or inadequate training, allowing for continuous improvement.
5. Six-Step LOTO Process
A standard LOTO procedure follows these six critical steps:
· Notify Affected Employees: Inform all relevant personnel that the equipment will be shut down for maintenance.
· Shut Down Equipment: Power off the machine using standard controls.
· Isolate Energy Sources: Disconnect the equipment from all energy sources, such as electrical breakers or hydraulic valves.
· Apply Lockout/Tagout Devices: Secure the energy-isolating devices with locks and attach tags to indicate the equipment’s status.
· Release Stored Energy: Drain or block any residual energy, such as pressure in pneumatic systems or tension-Net neutrality
· Verify Isolation: Confirm that the equipment is fully de-energized before starting work.
Skipping any step can compromise safety, making strict adherence essential.
IV. Regulatory Framework for LOTO
In the United States, LOTO is governed by OSHA’s standard 29 CFR 1910.147, which outlines requirements for controlling hazardous energy during maintenance. This regulation mandates:
- Written LOTO procedures for each piece of equipment.
- Employee training on LOTO protocols.
- Use of standardized lockout and tagout devices.
- Annual inspections to ensure compliance.
Non-compliance can lead to significant fines, ranging from thousands to hundreds of thousands of dollars, depending on the severity of the violation. Beyond financial penalties, violations can result in lawsuits, increased insurance costs, and reputational damage. Globally, similar standards exist, such as the UK’s PUWER (Provision and Use of Work Equipment Regulations) and Canada’s CSA Z460, emphasizing the universal importance of LOTO in industrial safety.
V. Common LOTO Mistakes and How to Avoid Them
Even with a LOTO program in place, mistakes can undermine safety. Here are common errors and strategies to avoid them:
- Skipping Verification Steps: Failing to confirm that all energy sources are isolated can lead to accidents. Always perform a final check to ensure the equipment is fully de-energized.
- Inadequate Training: New or temporary workers may lack proper LOTO knowledge. Implement regular, role-specific training to ensure all employees understand the procedures.
- Using Generic Tags: Handwritten or unclear tags can cause confusion. Use standardized, durable tags with clear information about the lockout.
- Unauthorized Lock Removal: Allowing someone other than the authorized worker to remove a lock violates OSHA standards. Enforce strict policies to ensure only the lock’s owner removes it.
- Neglecting Stored Energy: Residual energy, such as pressure in hydraulic lines, can pose risks. Always check for and release stored energy before starting work.
To prevent these issues, foster a safety-first culture, conduct regular audits, and use high-quality, individualized LOTO devices. Integrating LOTO procedures into a CMMS like EcoMaint can streamline documentation and ensure compliance.
VI. Integrating LOTO with CMMS EcoMaint for Enhanced Safety
Managing LOTO procedures across a large facility can be complex, especially when dealing with multiple machines and teams. This is where CMMS EcoMaint, developed by Vietsoft, comes into play. This cloud-based Computerized Maintenance Management System (CMMS) offers tools to streamline LOTO processes, ensuring safety and compliance while boosting operational efficiency.
Key Features of CMMS EcoMaint for LOTO Management
- Digital LOTO Procedures: Store and access equipment-specific LOTO procedures within the system, ensuring that workers always have the latest instructions.
- Real-Time Status Tracking: Monitor the LOTO status of equipment in real time, reducing the risk of accidental re-energization.
- Task Assignment and Communication: Assign LOTO tasks to authorized employees and notify affected workers, ensuring clear communication across teams.
- Audit and Compliance Tracking: Schedule and document annual LOTO audits, maintaining compliance with OSHA standards.
- Mobile Accessibility: Access LOTO procedures and update statuses on the go, improving responsiveness and accuracy.
By integrating LOTO with CMMS EcoMaint, maintenance teams can reduce errors, enhance communication, and ensure that safety protocols are followed consistently. Curious about how CMMS EcoMaint can transform your maintenance operations? Learn more about CMMS EcoMaint here.
Contact us via hotline: 0986778578 or email: sales@vietsoft.com.vn.
VII. Practical Examples of LOTO in Action
To illustrate LOTO’s importance, consider these real-world scenarios:
· Conveyor System Maintenance: A technician needs to repair a jammed conveyor belt. Without LOTO, another worker might attempt to restart the conveyor, causing the technician to be caught in the mechanism. By following LOTO procedures—shutting down the system, isolating the power source, applying a lock and tag, and verifying de-energization—the technician can work safely.
· Hydraulic Press Repair: A maintenance worker is servicing a hydraulic press. LOTO ensures that the hydraulic fluid pressure is released and the system is locked out, preventing accidental activation that could crush the worker.
· Electrical Panel Maintenance: An electrician working on a high-voltage panel applies LOTO to isolate the power supply, preventing electrical shocks or arc flash incidents.
These examples highlight how LOTO transforms hazardous tasks into controlled, safe processes, protecting workers and minimizing downtime.
VIII. The Broader Impact of LOTO
Beyond regulatory compliance, LOTO is about protecting people and fostering a culture of safety. A single accident can lead to devastating consequences, including medical costs, legal liabilities, and loss of trust among employees. By prioritizing LOTO, organizations demonstrate a commitment to their workers’ well-being, which boosts morale and productivity.
From a business perspective, effective LOTO programs reduce downtime, prevent equipment damage, and enhance operational efficiency. They also position companies as responsible employers, improving their reputation in the industry.
IX. Conclusion: Making LOTO a Priority
Understanding what LOTO stands for—Lockout/Tagout—is the first step toward creating a safer workplace. This critical safety procedure protects workers from hazardous energy, reduces accidents, and ensures compliance with regulations like OSHA’s 29 CFR 1910.147. By implementing a robust LOTO program, conducting regular training, and leveraging tools like CMMS EcoMaint, organizations can streamline maintenance processes and prioritize safety.
Whether you’re managing a single facility or multiple sites, LOTO is an investment in safety, efficiency, and peace of mind.
X. FAQs
1. What Does LOTO Stand For in Maintenance?
LOTO stands for Lockout/Tagout, a safety procedure that isolates and locks equipment to prevent hazardous energy release during maintenance, ensuring worker safety.
2. Why Is LOTO Important in Industrial Settings?
LOTO prevents accidents caused by unexpected equipment startups or energy releases, protecting workers from injuries like electrical shocks, burns, or amputations.
3. What Are the Key Steps in a LOTO Procedure?
The six key steps are: notify employees, shut down equipment, isolate energy sources, apply lockout/tagout devices, release stored energy, and verify isolation.
4. How Does CMMS EcoMaint Support LOTO?
CMMS EcoMaint streamlines LOTO by providing digital procedures, real-time tracking, task assignment, and compliance documentation, enhancing safety and efficiency.